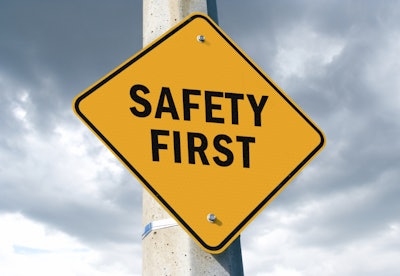
One of the biggest trends in safety expert circles is the push for improving safety culture within facilities, according to Denise Aronson, president and founder of Safety Partners.
It’s a simple idea that can be implemented right away with quick changes, alongside a broader strategy. Here are three ways Aronson says facilities can improve safety culture among employees:
Safety Moments
At a recent National Safety Council event, Aronson says she heard William Tolman, who runs the Tolman Group Laboratory at the University of Minnesota, give a valuable tip on how he encourages a safety culture among chemistry students.
“Whenever there was a meeting with his department of chemists, he required that the meeting started with everyone reporting ‘safety moment,’” Aaronson explains. “It could be 30 seconds or five minutes. The idea is to bring up something that happened that has relevance to creating a safety culture.”
Near-Misses
“Get the company excited about near-miss reporting,” Aronson says.
Why? If a situation has happened once, it could happen again. While companies often emphasize learning from disasters, near-misses provide ample opportunity to avoid those worst-case scenarios.
Near-miss reporting can be a part of sharing “safety moments.” Aronson says this exchange between employees is a good way for everyone to learn from each other, because hearing stories helps the lessons stick.
Job Safety Analyses
For a more in-depth approach, companies can also opt for a comprehensive safety analysis. Using information gathered from meetings in the board room to visits in the work area, the goal is to develop best practices for processing procedures.
Aronson says this analysis should look at protective equipment, engineering controls and equipment to determine the best mechanisms for minimizing safety risks. The analysis should also involve staff to boost institutional knowledge.
Once established, the analysis should be reviewed at least once a year.
Companies like Safety Partners offer consulting services that can help develop a partial or complete Job Safety Analysis. Click here for more.