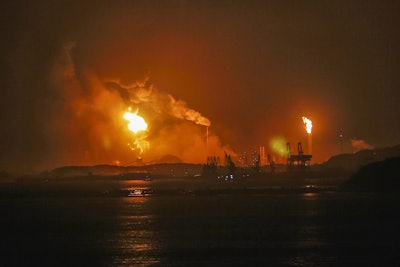
Explosions in manufacturing plants are almost always serious, often catastrophic — and, in most cases, very preventable. While obvious risks exist in facilities using flammable gases and liquids, there are many other potential catalysts that aren’t nearly as obvious, but can be just as dangerous. Dust is a prime example.
While some facility managers view the containment of dust and other air particulates as mainly a quality control issue, its benefits go much further. Since the buildup of air particulates can result in devastating explosions, the control and dispersion of them is equally important for safety. A common byproduct of operations like cutting, grinding, welding and mixing, in-plant particulates are simply too dangerous to ignore. Any company engaged in a process handling or particulate-generating operation will benefit from proper control practices.
Air Particulate Is Bad For Business And Safety
Uncontrolled particulate matter can lead to dust-encased workspaces and even spoil or ruin finished products. While these problems are bad for business, even greater issues than diminished product quality can arise.
Immediate safety problems — including fires and explosions — can occur when there is a high enough concentration of airborne dust-sized particulate in an enclosed space. Additionally, long-term health concerns exist for employees working where airborne particulate is present. These risks can range from a skin, eye, or bronchial irritation to more serious issues for people with asthma. There’s even potential for particulates to cause lung diseases like cancer.
Traditional Air Particulate Control Methods
There are several methods facilities usually employ when it comes to deterring dust accumulation and contamination from space to space. These include:
- Local exhaust systems — in these systems, a high velocity airflow stream captures particles at the point they are generated and carries them away.
- Exhaust with filtration — here, a high velocity airflow stream captures particles and recirculates them through a filter medium, where they are removed.
- Area exhaust — with this approach, a high volume exhaust fan draws air from the full room volume to an outside vent or recirculates through a filtration/separation device.
- Barrier separation — the simplest approach, this involves a wall or partition between affected areas.
The separation methods outlined above are dependent on moving a volume of air containing the dust particles, which is generally accomplished through the use of exhaust fans through ducts. A local exhaust set up would incorporate some type of hood designed to collect the air and particulate being moved and funnel it into the exhaust ductwork. Area exhaust would include multiple draw points through louvered openings in the ceiling or wall. Either of these methods could, and most likely would, include some type of filtration or particle separator in line to remove particulate from the air stream. This is necessary prior to either recirculation of the air back into the space, or discharge of the air into the atmosphere.
Proven Methods To Control Particulate Contamination
In some cases, a simple partition or wall between a clean space and an uncontrolled ambient space (such as between a processing area and a loading dock) is an effective means of separation. If negative air pressure differential exists across the wall between the clean and ambient space, the wall acts as a physical barrier, blocking most of the foreign matter from crossing the barrier.
The smaller a space can be made, the smaller the exhaust equipment can be specified. Partitioning around a dust source takes full advantage of this relationship. Reducing the volume of the space to be exhausted means a smaller fan(s) can be used, which reduces total air movement. Lower air velocity through filter media increases the effective particle separation of the device. Additionally, lower airflow through the filter reduces the frequency required for change out or cleaning.
However, plants with frequently changing layouts mean that permanent walls are rarely a good option.
Fabric Curtain Walls Boost Exhaust Efficiency
Thanks to flexible, easy-to-install fabric curtain walls, facility managers now have a solution to effectively separate processing areas from clean/finishing areas. If and when the layout of the facility changes, curtain walls can easily be reconfigured to fit the newest needs.
In a situation where a positive pressure space is desired, some sort of enclosure (or “box”) around the space would be optimal to maintain the pressure differential. Fabric curtain walls are an ideal partition solution as they are less expensive to install than hard walls and create a comparable enclosure seal to a hard wall. In many installation cases, they can be just as effective as hard walls if there are many penetrations through the partition like piping, conduit, etc.
The inclusion of standalone, high-speed roll-up doors in the curtain wall allows for efficient traffic flow, while minimizing time the interior is open to the processing area. Infiltration could be further reduced by positively pressurizing the clean space.
Additionally, fabric curtain walls act as an effective physical barrier on their own, blocking transfer of particles from space to space. Curtain walls can be single-layer fabric or multi-layer insulated and can easily be fitted with clear vision panels for visual communication between spaces.
Curtain walls are flexible by nature, yet very durable. They can withstand contact from machinery or product, and simply “bend without breaking,” in contrast to a hard permanent wall. They are also relatively easy to reconfigure if a space needs to be enlarged, reduced, or the shape of the space footprint needs to change. No “deconstruction” is required. Fabric curtain walls are easily installed, can be simply trimmed around conduit, piping, ductwork, etc., and can be anchored to the floor to withstand pressure differential across them.
Depending on the application, a curtain wall can be suspended from the room ceiling or can be supplied with a standalone framework to hang from. They are available as stationary units, as well as sliding (suspended from roller track), and can be fitted with strip curtains, personnel doors, or high-speed industrial doors for full range of access to the space.
Adding Safety And Efficiency With Curtain Walls
When considering possible dangers associated with explosions, facility managers should remember the role air particulate and settled dust from processes can play. Using fabric curtain walls to enhance the efficiency of standard exhaust methods is a good step in controlling dust and preventing explosions. Curtain walls can make exhaust and separation systems more efficient, as well as partition space with minimal set-up or maintenance costs. Their flexibility, reconfigurable nature and their ease of installation saves companies time and money.
Chuck Ashelin is an engineering manager for Zoneworks. A 15-year industry veteran, he holds a bachelor’s degree in chemical engineering.