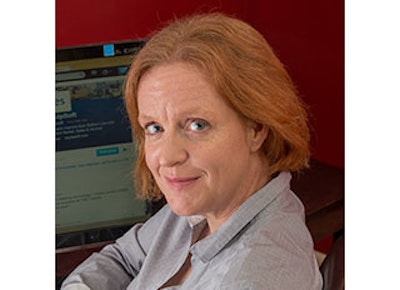
Now that the Food and Drug Administration has the power to invoke mandatory recalls, as granted by the Food Safety Modernization Act (FSMA), the speed and accuracy of your recall process has never been more important. The federal watchdog’s new teeth can be expected to leave their mark on more food companies, forcing the halt of distribution of suspect products — and that could affect your own supply chain. Fortunately, software technology can help ensure your business never makes it onto the FSMA mandatory food recall list.
Lot tracking is the place to start, but it should be noted that a recall program is not just signing off on a review of the traceability process. While that’s necessary, it doesn’t determine if your company can conduct an effective product recall. An effective recall program should include:
- Notification of an incident in real-time during production or distribution.
- A thorough investigation including tracking and tracing the potentially affected product.
- Testing conducted through mock recalls.
- Assessment of the risk to health and safety, and to your company’s reputation.
- Effective communications both internally and externally to the supply chain.
- Processes in place to monitor the effectiveness of the recall.
- Response to requirements, concerns and expectations of key stakeholders.
- Reviewing and continually improving processes and systems as new conditions arise.
Inquiry Tracking
Inquiry Tracking gives you the ability to track concerns from customers and vendors, and it lets you organize the call information electronically for quick access and historical purposes. In some Enterprise Resource Planning (ERP) software, you can initiate an Item Trace from right within the Inquiry Tracking screen in a user’s role center, and trace the item forward and backward.
Within the Trace functionality, you can see the trace from the purchase of raw materials to the production orders that consumed them, and all the way to the shipment of the finished goods. The Item Trace can then automatically create a compilation of all the contacts that received the finished goods. There should be visibility between Inquiry Tracking and Recalls within your ERP system — so that a customer complaint can be linked to a recall.
Mock Recalls
Global food safety standards, such as BRC, require that both traceability and recall are tested. In the latter case, mock recalls can be compared to fire drills — making sure everyone knows their role, and how long it takes to fulfill those roles. A good idea is to throw in some ‘curveballs’ to your mock recall to make sure you’re prepared for the unexpected by using strong internal and external communications. The only difference between a mock recall and a real one should be that external communications are not sent externally to your supply chain in the case of the mock recall.
Sahale Snacks: “Now anyone can begin a recall”
One food manufacturer, Seattle-based Sahale Snacks, which makes nut-based bars sold at more than 4,000 locations across the U.S., has been ahead of the compliance curve. Sahale had been through the 2010 nationwide pistachio recall as a result of one of their suppliers, during which they had to make do with Excel pivot tables, says Lindsay Palmer, Sahale’s supply chain coordinator. “Although we got through that recall with flying colors, the effort to do so was tremendous,” with diverse spreadsheets and a lack of a centralized data system resulting in much labor redundancy.
When Sahale Snacks began investigating Enterprise Resource Planning (ERP) software options in 2010, they were just ahead of the game-changing FSMA rules; in fact, Sahale’s CEO Eric Eddings was prescient in his observation that “as new regulations come in for food, as the industry changes, we need a system that can easily make the needed changes.” The built-in technology for automating lot traceability and recall processes within JustFoodERP was a major consideration in their selection of that ERP software for their business, says Palmer, as well as “more manufacturing friendly scheduling tools” and other food industry-specific functionality.
Allergens in Sahale products (full of nuts!) are recorded within the software, and the manufacturer’s recall process now involves, literally, the click of a button to start the minutes-long recall. “Before we got our new ERP system, only a few of us specialized in food recall — but we like to go on vacation, too!” says Palmer. “Now many employees can just type in the lot number and push the button.”
While federal legislation requires no more than 24 hours to complete the recall process, preceded by bi-directional lot traceability across the supply chain, product recall can be achieved within a few minutes. For example, at Sahale Snacks, their system uses Microsoft mail merge technology to integrate with CRM to auto-create a letter that contains all the information needed regarding the potential recall and emailed to stakeholders — all of this triggered by a single button within the ERP system.
Recall efficacy enabled by software technology results in significant reduction of associated costs and risks — now more important than ever with the advent of mandatory FDA recalls. Staying ahead of the food safety compliance curve, as Sahale Snacks has done, pays big dividends.
Heather Angus-Lee, a long-time business and trade journalist, now writes for IndustryBuilt. She can be reached at [email protected].