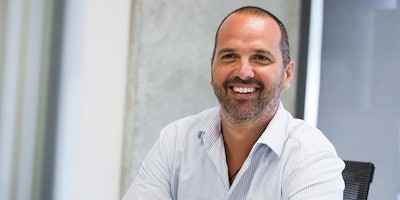
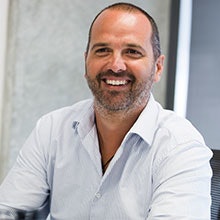
One of the biggest challenges facing the food industry today is the harmonization of food safety standards. With food imports and exports on the rise, particularly in emerging markets such as India, Indonesia and China, food manufacturers worldwide must contend with a proliferation of public and private standards as different governments increasingly enforce their own national guidelines.
Despite the obvious advantages of process standardization for food manufacturers — from the simplicity of managing fewer processes to cost savings and economies of scale — the demands of localization and customization mean there will always be exceptions to the rule. This makes process standardization challenging.
Sociologist Roland Robertson labeled the dichotomy that this presents “glocalization” — the simultaneity or co-presence of both universalizing and particularizing tendencies. And for food manufacturers under pressure to standardize processes while adhering to local regulations, it translates into a greater need to introduce and manage process variants to global standards so that they can comply with different quality and safety regulations and meet individual customer requirements, as necessary.
If not properly managed, though, introducing process variations can lead to increased costs, process inconsistencies and bottlenecks every time a new variation is introduced. This can be particularly frustrating when only slight tweaks to standard processes are necessary to meet the requirements of a specific location, product or customer.
What steps can food manufacturers take to deal with what would seem to be two diametrically opposed business models? I believe there are ways of achieving the nirvana of process standardization with the ability to control process variations as appropriate. Here are seven steps food manufacturers can take to make this happen.
1. Standardize core processes
Food manufacturers operating across multiple countries with multiple sites, products and varying customer requirements must first agree on a set of core or standard processes. These processes should then be assigned to global process owners who are responsible for their ultimate governance and control. This master platform will act as a blueprint against which all local variations will then be considered.
2. All process variations must be authorized
Local process variants can be considered and established only after this standard process base has been defined. Any changes applied by variant experts must then be highlighted and visible to all users against the core processes. There should be no modifications to process variations, unless authorized by the global process owners, enabling them to retain complete control.
3. Track changes
Food manufacturers must be able to oversee, compare and report on all the process variations that exist for each standard process. Doing so will allow the company to see and track exactly what activities have been added, removed or changed, and understand how they diverge from the original process. This will enable global process owners to be completely aware of what is happening at a macro-level, while simultaneously giving local teams the flexibility to meet regional or customer-specific demands.
4. Intuitive access to process variants
Any time a process variant has been introduced, it must be easy for employees to find and access those variations that are applicable to them. Ideally, employees should be able to select the process variant they seek electronically from a list, or be routed automatically to the exact variant relevant to them, dependent on a default location, product team or department. This will not only save huge amounts of time in sifting through documentation or manuals, but will also help to support process adherence.
5. Conversations about changes
If the global process owners want to make an alteration to the standard process, they should alert local variant owners for feedback and/or amendment and, ultimately, for approval to merge it into each of the established variant processes. Introducing this layer of consultation and dialogue provides variant owners with an opportunity to apply their on-the-ground expertise to ensure that the particular needs of the process variation are still met.
6. Shared global intelligence
There should be a global reporting function so that process champions can always view the entire inventory of process variations, and determine how they compare against the standard core process.
7. Accounting for costs and time
Process variant costing and timeframe tracking is necessary to compare the costs and time between variations and the standard process. This allows food manufacturers to decide whether they should retain or remove specific process variations. It also highlights cost savings opportunities and the impact of process changes.
Tracking and measuring the impact of process variations is critical for food manufacturers to have a clear understanding of not only the volume and effects of process variations, but also their benefits or drawbacks. Armed with this information, global process owners can work with local teams as necessary to challenge variants and improve transparency, compliance and control. Employees, in turn, have the power to be more agile because they have sufficient ownership to customize or eliminate activities as required.
Introducing a simplified approach to process management and improvement that encourages participation at both a global and local level allows food manufacturers to achieve the benefits of scale from standardization, while simultaneously having the freedom to customize processes and, importantly, comply with local regulations.
Ivan Seselj is CEO of Promapp Solutions, an industry leading provider of cloud-based process management (BPM) software for creating and managing business processes online. You can contact him at [email protected] or follow him at @Ivanseselj. You can visit Promapp at www.promapp.com.