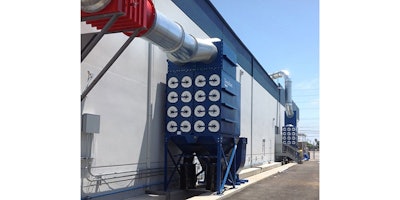
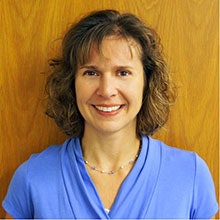
Agricultural and food processing facilities have been leaders in implementing combustible dust mitigation equipment, but it’s time to take a refreshed look at the current standards potentially affecting your facility.
The National Fire Prevention Association (NFPA) recently published the 2017 edition of NFPA 61, Standard for the Prevention of Fires and Dust Explosions in Agricultural and Food Processing Facilities. NFPA 61 has been providing guidance since 1970 on combustion risks in “facilities handling, processing, or storing bulk agricultural materials, their by-products, or other agricultural related dusts and materials.” The 2017 edition introduces updated content and some important new concepts.
NFPA standards are not federal law, but they become legally binding when local and state municipalities adopt them as regulatory code. And OSHA can reference NFPA standards when they levy fines for unsafe work environments under the General Duty clause.
NFPA 61, 2017 Edition
For the 2017 edition, the document has undergone substantial revision to better align with NFPA 652, Standard on the Fundamentals of Combustible Dust. A new chapter on hazard identification was added to clarify how to determine whether the materials present in the process are combustible or explosible. This is an important responsibility for the owner or process operator, and needs to be the first step in a risk mitigation plan.
A Dust Hazard Analysis (DHA) is another new concept in the standard. If you have a potentially combustible or explosible material in your facility, then a DHA is developed to address the risks present. NFPA 61 describes the methodology for a DHA and gives an example checklist. The standard lists a completion date of June 2021 for facilities with existing equipment, but the DHA must be completed sooner for any new process or existing processes being significantly changed. Then it must be completed as part of the project.
The standard also contains a new section on the methods and requirements for the Performance-Based Design option for risk mitigation. This option gives the process owner the flexibility to use alternative solutions based on good engineering principles and documentation in addition to the prescriptive requirements outlined in NFPA 61.
Process Review
Food processing facilities have been a leader in addressing combustible dust risks, but now some of those early systems are aging or out of date, and new technologies are available to upgrade them. At the same time, the Food Safety Modernization Act (FSMA) and increased production rates may be driving facilities to make changes in their food manufacturing processes. Because a major process change could trigger an immediate DHA review, it makes sense to combine the process equipment review with dust collection system evaluations so that combustible dust risks can be addressed at the same time.
While owners needing to complete a DHA have until 2021, reviewing your mitigation approaches sooner could highlight a strategy that integrates better with your production process and provides an optimized system.
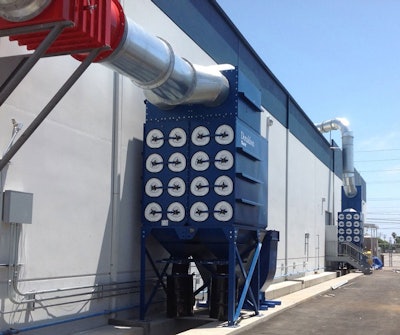
Mitigation Options
The process owner responsible for a DHA and mitigation strategy should consider some timeless fundamentals, as well as different options for effective risk mitigation.
Facility Housekeeping
The first consideration in fire and explosion prevention should be housekeeping. Some facilities with devastating events looked fastidious on the surface, but ignored dust accumulations on suspended ceilings, light fixtures or girders. If an initial explosion disturbs this dust, it becomes suspended fuel for a secondary, building-wide deflagration. Make sure you inspect and periodically clean all surfaces from floor to ceiling — including walls — avoiding accumulations.
Dust Containment
The next consideration is dust containment. Removing dust from the air prevents it from accumulating on surfaces. An effectively designed dust collection system uses hoods to capture dust and the airflow transports it via duct to a dust collector. Once the airflow requirements are known, then a dust collector can be chosen for the application and outdoor or indoor location reviewed. While an outdoor location may simplify the risk mitigation strategy, there are mitigation equipment options that do allow for indoor use.
Food manufacturers in particular may have valid reasons for preferring indoor installations — and with today’s engineering advances that is more viable. Here are a few concerns that may favor indoor location:
Cross contamination — Newer compact dust collectors bring highly efficient filtering power with a small footprint and minimal to no duct needed. Prevent cross contamination between product lines by collecting dust right at the point where fugitive dust is generated instead of filtering air from multiple product lines in one dust collector, minimizing the mixing of dusts.
Cleanliness — Dust removal at the point of fugitive dust creation is critical for preventing it from dispersing in the production facility. When dust control can be tailored as point-of-use systems, you no longer need to have long lengths of duct running through the production facility. This reduces the risk of combustion events expanding through a facility within the ducts, and may lower the initial system cost and/or ongoing maintenance requirements.
Downtime — Using several smaller dust control systems at various points in your production line versus one large centralized dust control system can help minimize downtime and may save on energy expense. The dust control system runs only when its specific production area is in use. If the production line is down, then air is not being moved and filtered when no fugitive dust is generated.
Of course, a fire or explosion in the middle of your facility may have significant impact. If you want the advantages of indoor collectors, you should review your risk mitigation plan and determine the equipment and strategy that works best for your facility.
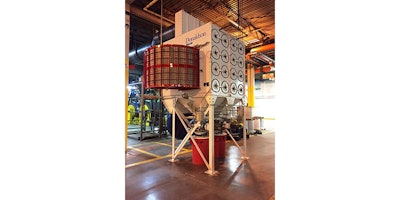
Mitigation Equipment
A combustible dust mitigation plan should consider both prevention and protection actions. The food industry has done a good job in prevention by addressing the sources of sparks or flames in a facility, minimizing the risk of a fire occurrence. But no prevention method is 100 percent effective, so a closer look at protection equipment is still warranted.
Protection equipment limits the scope of damage from a fire or explosion. There are a variety of equipment options now available, with some that may be preferred for a food processing facility.
Isolation equipment — Isolating a fire or explosion to only the dust collector can prevent damage to the process line or building. An outdoor dust collector may be easier to isolate, especially if the filtered air is not being returned to the building. But, regardless of where the collector is located, isolation is a necessary consideration for a mitigation strategy.
- Passive devices — Flow actuated isolation valves are one example of a passive isolation device that prevents an explosion from propagating through the duct. The valve activates based on a pressure wave without the need for an activating sensor.
- Active devices — Active devices (inlet or outlet) are available for either fire or explosion applications, using a sensor and signal to trigger activation. Explosion isolation valves prevent flames from flowing back through the duct in the event of an explosion; or fire abort dampers divert smoke and flames to a safe location in the event of a fire.
Venting — If the dust is explosible, one of the traditional mitigation strategies is using explosion vents. Locating the dust collector indoors can pose some additional challenges for applying this equipment.
- Explosion vents — Create a planned pathway for gases to escape by installing a weak panel — an explosion vent — on the collector. When a defined pressure is reached, the vent opens to reduce pressures in the collector. The open vent must direct the resulting fireball to a safe location. When located indoors, explosion vents must be ducted to an outside wall or roof, allowing the fireball to escape from inside the facility. The addition of a duct will adjust the performance of the explosion vent, which has to be factored into the selection and location of the collector and explosion vent.
- Flameless explosion vents — A flameless explosion vent combines an explosion vent with a stainless steel metal mesh to contain the flame front while relieving pressure. An indoor dust collector with a flameless explosion vent is not required to be vented through an outside wall or roof, allowing a wider range of potential locations. The flameless vent does not have the same performance as a traditional explosion vent and may have limits on the size of room in which it can be used.
Explosion suppression equipment — In a suppression system, sensors on the collector monitor pressure, and, in the earliest milliseconds of a deflagration, trigger the injection of a flame-suppressing chemical (Sodium Bicarbonate) into the collector. The cloud absorbs heat and interferes with flame propagation — snuffing out the fireball before it grows to a threatening size. Highly effective, suppression systems can be used indoors and retain dust within the collector, which may be an important option for some food processing facilities. It can also reduce the risk of associated fires after the deflagration and may reduce clean-up, which shortens downtime. Suppression system techniques can also be applied to inlet and outlet ducts for isolation, providing the same benefits listed above. This may be a good combination of options for your mitigation strategy.
There’s a lot to think about when you’re evaluating your combustible dust risks and mitigation strategies. NFPA 61 gives you guidance on a dust hazard analysis, and can help to develop a plan to meet your specific facilities requirements in a timely manner.
Undertaking this initiative now can potentially save you time and money as you integrate any process equipment upgrades or changes with implementation of your revised combustible dust strategy. The mitigation options available are better than ever, allowing you more flexibility in the location of your dust collection system. As you weigh your options, don’t forget an initially higher priced mitigation strategy may reduce the potential downtime you would face from a combustible dust event, causing damage to your production facility. The investment might be well worth it.