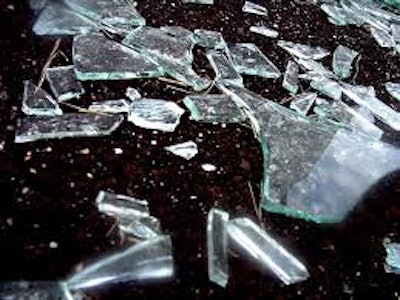
Improperly maintained sight glasses can easily become the weakest link in a processing system, becoming difficult to illuminate and providing less than optimal visibility to process observers. In the most severe cases they can actually fail endangering workers, leading to extensive destruction of property and forcing unplanned downtime. Strict adherence to the proper maintenance procedures can minimize the opportunities for problems.
Tip #1: Glass or gaskets should not be reused. Once a sight glass disc has been removed from its mounting for any reason, both the glass and gaskets must be replaced with new parts because of damaging stresses created during installation and use. However, fused glass safety windows are an exception. They provide a borosilicate glass disc permanently fused to a stainless steel ring that takes the stress of installation. Unlike glass discs, fused glass safety windows can be returned to service after maintenance without the risk of rupture due to compressive torque damage to the glass caused during installation. Such sight windows cost more initially, but they save money over the long term in replacement costs.
Tip #2: Clean the glass properly. Always use a commercial glass cleaner; never resort to wire brushes, metal scrappers or harsh abrasives. Don’t try to clean the glass while the process equipment is operating. A sight glass that appears cloudy or roughened after cleaning should be replaced. By the way, borosilicate glass resists corrosion and erosion better than soda lime glass, so if clouding is a problem (especially with caustic process media), switching to a borosilicate sight glass may help.
Tip #3: Inspect sight glasses for damage regularly. To check for scratches, shine a very bright concentrated light source at roughly a 45-degree angle. Anything that glistens should be inspected closely. Replace the glass if you detect any scratches that catch the fingernail or any star- or crescent-shaped marks that glisten. Also, inspect sight glass frames and flanges for corrosion buildup.
Tip #4: Always use first-quality replacement parts. Never install a sight glass that is scratched, chipped or otherwise damaged. Glass seating surfaces must be flat within 0.005Ëť with a smooth finish. Flanges must be rigid. Do not allow the glass disc to make contact with metal during the assembly process. Use new, clean and smooth gaskets of the same diameter and fit them concentrically.
Tip #5: Employ proper bolting procedures. Never tighten bolts on a sight glass while the process equipment is operating. Follow a regular tightening sequence to ensure even loading of the glass, allowing a maximum difference of no more than 1.5 ft/lbs between bolts during tightening. Tighten only enough to produce a positive seal against the process pressure. It may be necessary to retighten the bolts after initial cycling of the process vessel, but never tighten them when the sight glass is hot.
David G. Star is president and CEO of L.J. Star Incorporated (www.ljstar.com), a supplier of sight glass and sight-flow indicator products. He owns Tank Components Industries, a manufacturer of tank heads and related process vessel components.