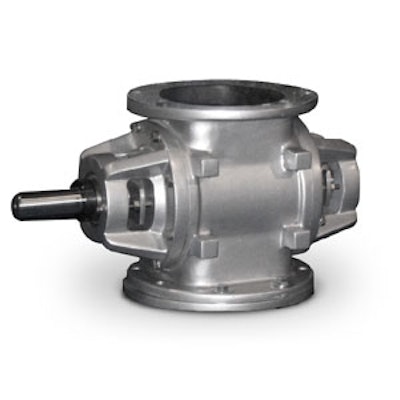
title
ACS Valves believes that its MD Series rotary feeder valves immediately contribute tangible operating efficiency advantages, and long-term production and maintenance savings. According to the company, this material-metering valve additionally boasts:
- An optimized seal that can reduce compressed air loss by up to 28 CFM a year for a savings of up to $3,600 a year based on an annual industry average cost of $1,200 per 10 CFM of compressed air.
- An 8-vane rotary valve that ensures proper pressure sealing at the inlet and outlet flange.
- An outboard bearing design that removes the bearings from the path of damaging and contaminating materials, protects the bearings in high-temperature applications to 750ºF, and easily manages pressure differentials up to 15 PSIG, thereby further extending maintenance cycles.
- Housings CNC-machined to precise tolerances with optimal strength, eliminating axial shaft movement, seal leakage and shortened bearing life.
- Construction from cast iron, or cast 304 or 316 stainless steel.
- 7 valve sizes —from 4 to 16 inches.
- Availability of a variable-frequency drive to modulate drive speed and reduce electricity consumption based on fluctuating power requirements.
- Closed-end, metering, shallow-pocket, Teflon®-coated or adjustable-tip rotor configurations.
- Adjustable rotor tips, which are available in EPDM, hardened steel, stainless steel, bronze or polyurethane.
- Hard chrome, tungsten or Teflon® interior surface coating options.