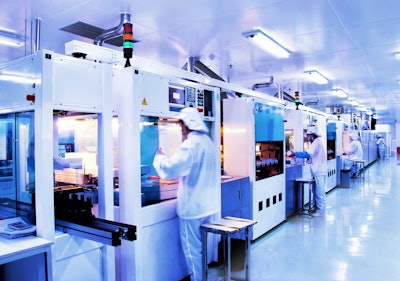
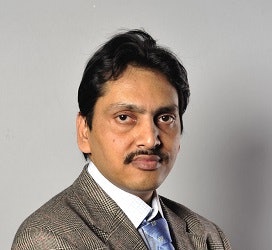
Industry 4.0 and digital transformation bring with them smart factories and smart manufacturing units, which are fully integrated, collaborative manufacturing systems capable of adapting to supplier and customer needs in real time. The latest technologies in Internet of Things (IoT), cloud computing, data analytics and artificial intelligence are forming an integral part of this digital-driven industry. But how important is digital transformation to the manufacturing industry?
According to a recent PWC survey, 72 percent of manufacturers are increasing their digitization efforts, investing $907 billion per year – roughly 5 percent of revenue – toward smart factories and connectivity.
As manufacturers grapple with organizational and ecosystem-wide changes, operations feel the pressure of having to keep up. While smart manufacturing effectively addresses operational challenges, the real challenge begins with a vision of where to prioritize investments. Despite years of automation, the smart manufacturing hasn’t seen wide adoption. According to a report by Cisco, only 26 percent of companies view their IoT initiatives and deployments as a success, and 60 percent of similar projects reportedly are stuck at the Proof of Concept (PoC) stage.
What are some of the issues that are stopping companies from leveraging the benefits of smart manufacturing? Here are five key areas manufacturers need factor in for successful digital evolution:
Data & Interconnectivity
The growth of connected devices and improved ability to record significant data from the field pose unique challenges for manufacturing companies and their data silos. Every manufacturing department works independently with lengthy data acquisition protocols. These data silos impede growth. As the industry moves from mass manufacturing to mass customization, freeing up data from disparate networks and investing in connected information systems should be a top priority for establishing interconnectivity. Manufacturers need to be ready to break down their silos, clearing the path toward better analytics and operations. Companies should also consider creating cross-functional teams and adopting new operational models, such as closed-loop manufacturing, to address their data challenges.
Evolving Technology
The manufacturing industry has come a long way with the advent of the digital era. As technology advances every passing day, companies must position themselves to benefit from it.
Advanced manufacturing technologies such as 3-D printing, sensors and intuitive machinery are quickly finding inroads to the core of today’s industries. Technologies such as augmented reality can be used in various forms to avoid unintentional errors in plants thereby improving operational and performance visibility of the plant. Workers can be trained using virtual reality to resolve various issues in a systematic manner, dramatically reducing the cost of maintenance. Factories will be able to predict failure of machines and enable proactive maintenance reducing the downtime. Manufacturing leaders should be ready to deal with rapid technological changes, modernize their legacy assets and incorporate new system designs.
Augmenting Processes
Automation of assembly lines was the first success that the automotive industry witnessed in mass production. The smart manufacturing era is now pushing beyond production lines to automate and augment processes toward operational efficiency. From sales and operations planning to shop floor activities, smart manufacturing can manage and optimize processes along the entire supply chain. However, manufacturing leaders must be willing to embrace the consequential process disruption and operational changes to capitalize on new opportunities.
Investing in People
Automation has brought with it the need to train and adapt today’s workforce to technology and new systems. To strike a balance between their workforce and machines, industries have to look at creating a centralized ecosystem that takes advantage of modernized skill sets. IoT is a major driver for smart manufacturing, but 42 percent of companies report having a limited understanding of it while 24 percent do not understand it at all. In this changing climate, manufacturers must address the challenges of an under-skilled workforce. Manufacturing leaders must not only have domain knowledge, but also technical know-how about equipment, data and automation. As a model to strive for, an appropriately agile workforce would consist of employees who are quick learners and capable of upskilling fast.
Security
With increased connectivity and new communication protocols, companies are increasing security measures to protect critical industrial systems. Compared to traditional manufacturing systems, smart manufacturing systems are vulnerable to a growing number of cybersecurity threats. Updating existing IT infrastructure is a start, but what is most essential is incorporating security measures into applications or security by design to strengthen systems.
smart manufacturing is the future and that companies need to move toward adapting to the technological landscape. The industry’s problems do not lie in awareness though – they lie in execution.
To succeed in smart manufacturing, companies need to prioritize long-term business goals over short-term returns with lower risks. Using the above five areas of critical importance as a guide, companies should explore partnering with system integrators who have comprehensive knowledge of IoT and begin to incorporate the industry’s best practices.
Ashish Saxena is vice president and business head of North American Manufacturing for Wipro Ltd.