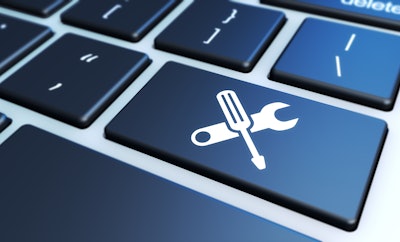
The accumulation of equipment failure data is a critical aspect of effective asset management and life-cycle analysis. By analyzing historical equipment failure data, one can assess the reliability of a facility and gain insights into the likelihood of asset failures. Key indicators such as failure rate, mean time to failure (MTTF), and availability play a vital role in shaping maintenance strategies and optimizing operations.
Equipment failure occurs when a piece of machinery or system cannot perform its intended function. This failure could be partial, complete, or even a potential risk. Reliability, expressed as a percentage, gauges the likelihood of equipment performing without failure over a specific period, represented mathematically as (1 - The Probability of Failure).
To harness the power of Reliability Analytics, GE Digital APM offers a robust module that analyzes failure data to draw conclusions and make predictions about equipment reliability. The process involves collecting failure data and storing it in GE Digital APM, including information about equipment type, location, failure modes, repair actions, costs, and various other critical data points. With the data in place, it can be formatted and fed into the Reliability Analytics tools to conduct thorough analyses.
Failure data collection and analysis are interconnected with all aspects of reliability management. It is crucial to initiate failure data collection during the early stages of systems design and continue throughout the product's life cycle. Both suppliers and users should meticulously track and analyze equipment malfunctions and failures. The ALD FRACAS (Failure Reporting, Analysis, and Corrective Action System) specialists play a vital role in defining the failure data collection procedure, ensuring comprehensive processing, and implementing corrective actions and preventive maintenance.
Timely and efficient failure data collection, aided by ALD software, not only prevents recurring failures but also simplifies and reduces maintenance tasks. The FRACAS system facilitates a closed-loop feedback process, wherein users and suppliers collaborate to collect, record, and analyze hardware and software-related failures. A Failure Review Board (FRB) assesses the failures, considering factors like time, resources, and costs, and suggests corrective actions to prevent future occurrences. The important data associated with this process includes:
- Failure Rate: Failure rate quantifies the number of failures occurring within a specific time frame. It can also be calculated as the inverse of the
- Mean Time Between Failures (MTBF), which represents the duration between successive failures. MTBF is relevant for repairable assets, whereas non-repairable assets, like consumables, are better measured using the mean time to failure (MTTF).
- Mean Time to Failure (MTTF): The mean time to failure (MTTF) indicates the total lifespan of a non-repairable asset, such as consumables or disposable instruments, before it completely breaks down.
- Availability: Availability measures the time an asset can perform its intended function. Unlike reliability, it does not focus on continuous operation but evaluates the overall ability of the asset to function.
- Defining the Reliability Index: The reliability index signifies the likelihood of equipment failure within a specified time frame. Organizations and industries might employ different criteria and weights for performance indicators to calculate this index effectively. By determining assets that require special attention, the reliability index guides strategies to enhance overall reliability.
Collecting equipment failure data is of utmost importance in various industries. By analyzing this data, businesses can identify patterns and trends, allowing them to make informed decisions about maintenance schedules and equipment replacements. This proactive approach not only reduces downtime and costs but also increases productivity and customer satisfaction. Furthermore, the data collected can be used for research and development purposes to improve the design and quality of future equipment.
So, if you want to ensure the smooth operations of your business and stay ahead of the competition, start collecting equipment failure data today!
Lindsey Walker is the marketing manager for NEXGEN, a Sacramento-based industry leader in designing advanced computerized maintenance management systems and asset management software tools.