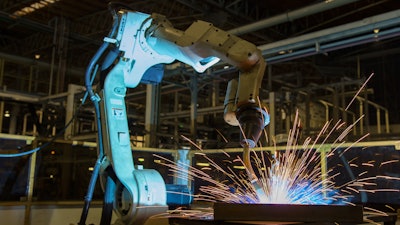
Once upon a time, humans used to melt bronze in clay furnaces. Over the years, metal fabrication companies have come a long way and have become exceedingly advanced in the way they get their job done. The art of metal fabrication is a collaboration between skills and intellect, requiring it to be adequately understood.
However, it is unfortunate that metal fabrication is perhaps one of the most underrated industries. Most people are unaware of the updates and latest trends in the arena of metal fabrication industries despite various related sectors being affected and impacted by them. This blog reveals five interesting trends and technologies that have been incorporated into the metal fabrication industries over the years.
1. Automation and CNC Machines
Previously, most of the work in metal fabrication industries required a high level of human intervention to function. However, things have changed, and the work has become more efficient. This has been possible due to implementing automation techniques. Unlike manual lathe machines, CNC or computer numerical control machines do not require manual controlling of the machines.
CNC machines also require fewer operators as compared to manual machines. For this reason, CNC machines have become an integral part of metal fabrication companies. CNC machines are also beneficial when it comes to performing tasks that are repetitive and tedious. In other cases, they are equally helpful in performing tasks that are too dangerous to be completed by human laborers and may result in accidents.
Integrating CNC machines have resulted in increased productivity and efficiency in the long run. Automation also allows opportunities to reduce waste and improve operations.
2. Reshoring
Reshoring, technically, means the trend of outsourced industries and jobs relocating to their original native location. While other industries (e.g., IT sectors) have boomed overseas, metal fabrication industries have witnessed an opposite trend, where various metal fabrication companies have returned to the place from where they are originally from.
This trend has risen due to rising labor costs in many countries, particularly India and China. In other words, reshoring allowed metal fabricating companies to be more cost-effective, indigenous, creative, and innovative. Reshoring has helped generate more employment opportunities in the native country, which may have been otherwise not generated.
3. Cybersecurity
Upgrading technology has been a need in recent times. Similar to other industries, new technology is also slowly taking strides in metal fabrication. With these upgrades on the technological front, it is essential to ensure that the networks remain safe and sound. This is where cybersecurity chips in.
As per the 2022 reports of IBM's X force Threat Intelligence Index, the most affected industry from the Cybersecurity attacks as of 2021 was the manufacturing industry. The manufacturing sector received around 23.2 percent of the cyberattacks, resulting in millions of data breach costs. These increasing cyber-attack incidences may put potential risks to the metal fabrication industries. One of the most common threats includes the breaching of sensitive information.
For example, productivity metrics, financial metrics, etc. This is why the need for cybersecurity has increased more than ever. Even some companies educate their employees about fundamental hacking tactics, such as phishing, so that both industries and employees can be protected from any random ransomware attacks.
4. Collaborative Robotics
It is a fact that jobs in metal fabrication industries can be potentially risky for human workers. Thus, it is only natural for many metal fabricating companies to integrate collaborative robotics into their work. Some years back, when robots used to be fairly large and took up a lot of working space, integrating them into the workspace was not cost-effective.
However, with recent advances in robotic sectors, robots have emerged as collaborative robots or cobots that allow them to work alongside team members to complete dangerous or monotonous tasks. Another reason for using cobots in metal jobs is that such robots have helped meet the shortage of laborers during the covid-19 pandemic.
5. 3-D Printing and Additive Manufacturing
3D printing has emerged as one of the most promising tools in every industrial sector. And metal fabrication is equally impacted by this technological upgrade. Unlike subtractive manufacturing, additive manufacturing has helped many sectors create objects by building one layer at a time.
3D printing and additive manufacturing has thus allowed workers in the field of metal fabrication to provide a rich level of customization and create nearly anything metal-related with almost no wastage.
Metal fabricating industries have been under-appreciated despite serving various background roles in different industries. Many specific industries require high-demand services from metal fabrication sectors, which has been instrumental in improving the trends and technologies used in metal fabrication.
Many changes in trends and technologies have highly helped metal fabricating companies increase their productivity and work efficiency by a large margin. Recent technologies, such as automation, 3D printing, and collaborative robots, have expanded the metal fabrication industries. As more advances are introduced in this sector, more positive changes should be seen in metal fabrication.
Vincent Hua is the Marketing Manager at TSINFA.