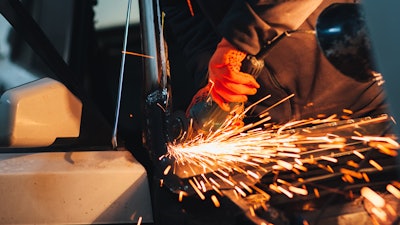
A manufacturing plant needs to have reliable operations in order to improve efficiency and profitability, and there are multiple metrics that can be used to determine this via the level of machine reliability.
Machine uptime represents the percentage of time a machine was available and working. The higher the uptime, the higher the reliability of the machine. It is the complement of machine downtime. If machine downtime can be calculated, finding out machine uptime is just one subtraction away.
Machine Downtime = Number of seconds machine was down / Total number of seconds observed
The product of this division problem is then multiplied by 100 to provide the rate of machine downtime.
Machine Uptime =100 - Machine Downtime
For example: If a machine was down for 20 minutes in a window of 24 hours, the machine downtime is:
Machine Downtime = 20 x 60 / 24 x 60 x 60
x 100 = 1.38%
Machine Uptime = 100 - 1.38 = 98.62%
Increasing machine uptime comes with many benefits, including increased productivity, less unscheduled downtime, less use of maintenance resources, more reliable and predictable operations, and a more robust supply chain. Some of the most prudent ways to improve uptime can include:
- Condition monitoring technology and predictive analytics. A machine in operation has a plethora of metrics that can be tracked, the least of which are speed, torque, current, power, temperature and shear. It used to be difficult to monitor all of the various parameters, but with today's advanced technology and sensors, we are able to monitor all the different metrics of a machine with very high accuracy. It is much easier to optimize maintenance resources when you are able to track common failure modes, spot early deterioration signs, and sometimes even predict potential failures. Instead of having four hours of unplanned downtime to address an equipment breakdown, you can have 20 minutes of planned downtime to perform corrective actions. All the advanced monitoring systems also enable the implementation of the Manufacturing Execution System (MES). MES systems in turn can be used to reduce machine downtime. Tracking the material flow, hours a machine is in operation, and other ancillary data from the MES can be used to schedule maintenance with minimal disruption. Timely maintenance activities that are performed around production schedules help to increase machine uptime.
- Training programs. Adequate training has to be provided to everyone that interacts with the machines. One of the prominent reasons for machine failure is the mistakes by employees, especially machine operators. This can be attributed to improper training and lack of experience. A great way to fix this problem is to invest into implementing autonomous maintenance. Similarly, you might have maintenance techs with different levels of skill working on the same machine at different times. All of these factors introduce great variability in operations and might negatively affect equipment reliability in the long term. Regular refresher courses and programs to upskill technicians should be given priority. Setting up standard operating procedures (SOP) and building maintenance checklists can help reduce the variability brought about by different technicians. They will not only improve the quality of performed maintenance work, they will make them faster and more efficient. In practice, you should have less planned downtime and that those planned downtimes will be shorter. Both of which will have a positive impact on machine uptime.
- Maintenance software. CMMS is a comprehensive software to manage, track, and execute all maintenance-related activities of a manufacturing facility. It can track and store all information on plant operations from the monitoring systems used. This large amount of data can be automated to improve the planning and scheduling of all maintenance activities - from allocating resources to coordinating complex maintenance projects. In the context of increasing machine uptime, a CMMS can:
- Integrate with condition monitoring technology to track equipment health.
- Set up the foundation for implementing proactive maintenance strategies and improving equipment reliability.
- Help maintenance planners allocate resources in time for both preventive and corrective work.
- Speed up maintenance work by providing instant access to maintenance logs, SOPs, and checklists, as well as by facilitating the sharing of knowledge among maintenance staff.
- Improve the Procurement Process. Choice of machines and vendors play an important role in plant efficiency and machine uptime. For example, a food processing plant can choose between magnetic direct drives and drum motors to drive conveyors. Drum motors require frequent maintenance due to their use of oil. Magnetic drives do not have such a problem. Though magnetic drives cost more, they are a more hygienic and economic choice for a food processing plant. For plant managers that are looking to maximize equipment uptime, selecting the right equipment type and vendor is the most proactive approach they can take. Of course, factors such as efficiency, cost of operation, manpower required, maintenance required, specific use cases, etc. should all be considered before making the final choice.
Increasing machine uptime is a goal that manufacturers have to actively invest in, as it improves the efficiency and profitability of plant operations. A perfect 100 percent uptime is rarely possible - but should be the goal nonetheless. Constant effort must be taken to reach closer to the ideal scenario. Besides the investments we outlined above, manufacturers have to set up a proactive culture and focus on continuous improvement in order to keep moving forward.
Bryan Christiansen is the founder and CEO of Limble CMMS. - a mobile CMMS software platform.