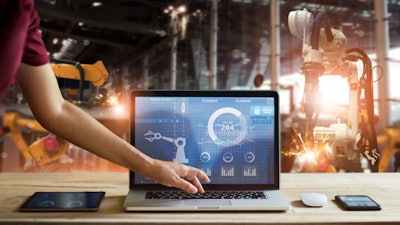
The benefits of an effective maintenance program are well established. With unplanned downtime costing industrial manufacturers an estimated $50 billion each year, finding a way to optimize the process is business critical. Predictive maintenance, where you optimize maintenance tasks in real-time, maximizing the useful life of equipment and avoiding disruption to operations, is viewed as the solution.
But how does an organization overcome the challenges and successfully transform its maintenance philosophy?
The goal of predictive maintenance is first and foremost to predict when asset failure is most likely to occur. Monitoring for future failure allows repairs to happen at the precise time required, rather than too early, while the part still has life, or too late, when the part is already offline.
By adopting this approach to maintenance, manufacturers can realize multiple benefits, including reducing unplanned downtime, maximizing device or equipment uptime, optimizing utilization of maintenance teams, avoiding warranty costs for failure recovery, and reducing the cost of spare parts and supplies.
However, making the transition from a preventive or reactive maintenance strategy to a predictive approach is no small undertaking. Predictive maintenance requires software to continuously gather sensor data from a physical asset and use advanced analytics for additional insight. A successful transformation is only possible when an organization prepares for it properly. Before making the shift to predictive, five operational areas need attention:
1. Understanding Asset Criticality
Before your organization can implement a predictive maintenance strategy, you need to map out your asset criticality to understand:
- Which assets are your most important for production?
- Which assets break down the most frequently?
- Which assets are the most costly to repair?
- Which assets cost you the most in lost production time?
The answers enable you to assign a criticality rating to each piece of equipment and focus maintenance processes on these vital assets. This helps inform key decisions related to your predictive maintenance strategy.
2. Infrastructure Requirements
Predictive maintenance utilizes sensor data and connected software systems to predict when a failure is likely to occur. This requires modern infrastructure to track a wide variety of data in real-time. Therefore, sensors need to be added to legacy machines to capture asset information. In addition, software needs to support data collection and management. Without an integrated hardware and software platform, a predictive maintenance program will remain out of reach.
3. Time Savings
Efficiency gains are a core benefit of adopting a predictive maintenance philosophy. However, organizations need a plan to direct the time savings gained from optimizing repairs and maintenance into other activities that drive the business forward. If not, manufacturers will not be able to take advantage of one of the key benefits.
4. User Adoption
With any new software or process, user adoption is a crucial hurdle to overcome. Unless there is buy-in from employees, the new system will fail. Predictive maintenance disrupts established processes, so you must train workers to help smooth the transition and make sure they can follow the new systems, software, and procedures.
5. Data Management
Data is a perennial issue, and in the case of predictive maintenance, the volume can quickly become overwhelming. Data accuracy and management are the foundations for delivering an effective program. Therefore, putting in place systems and processes to capture, track, and analyze the correct data to predict failures and malfunctions is vital. The timely monitoring and repair of potential problems enables manufacturers to reduce the risk of safety incidents, which can be both costly and potentially catastrophic.
Derek Shickel is the Engineering Operations Manager at Prometheus Group.