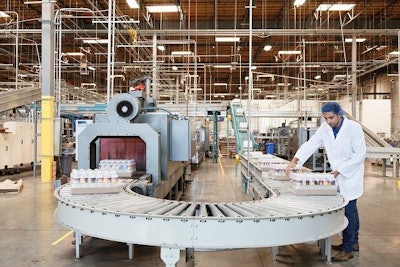
Conveyor belts systems help manufacturing facilities save tremendous time, effort, and resources by automating manual production operations. Easy to install, operate, and maintain, conveyor belts come with a host of benefits for production operations but in order to maximize conveyor productivity, cut labor costs, and reduce the risk of injury, companies need to consider several factors while keeping safety forward.
Here are eight ways to optimize conveyor belt operations and boost productivity:
Maintenance Is The Key To Maximizing ROI
The best way to avoid unexpected failures while optimizing performance is to perform preventive maintenance periodically, check lubrication regularly, and replace depreciated parts on time.
Find Fixes To Common Problems
Unexpected failures and replacements are very expensive but they can be easily avoided if you know how to fix common conveyor belt issues like:
- A sudden shut down for no apparent reason
- Accumulation of packages in only one area
- The drive keeps running but the belt is stagnated in one position
- The load does not accumulate on 1 or more areas
If you can fix all of these issues yourself, you will end up saving a lot of time and money. Most of the times, these issues occur due to overloading and can be easily eliminated with training and intelligent load distribution. So check things at your end before you call for service.
Calculate The Load
Specification error is the most common conveyor belt problem because in the absence of detailed information of load, the performance gets adversely affected. So examine the load by making a list of all the units that will be placed on the conveyor belt system and consider their shape and form, their dimensions, the orientation, and the position of the load on the conveyor. All of these things should be considered in advance to ensure smooth, uninterrupted operations.
Check Your Conveyor Belt’s Performance
Once the new conveyor belt system has been installed and your facility is all set for production, you need to fine-tune all the controls and ensure that you are not missing out on any mechanical issues. Visually inspect the entire conveyor belt system to make sure that every pull-stop is accessible, safety stickers are visible and junction boxes are closed. Test the functioning of the conveyor belt system by placing few items on the belt and look for apparent flaws to ensure that cartons don’t hang up midway and all diverters and merges are working properly. When it is time to fully load the conveyor belt examine how the system handles a huge throughput and see if you can detect any bottlenecks in the conveyor belt system early on.
Choose The Right Horizontal And Vertical Conveyors
If the nature of your business operations, throughput, product characteristics, or plant layout requires a change in elevation, make sure you choose the right type of conveyor belt system. A change in elevation can make or break the performance of your conveyor belt system and there are several factors that you need to consider if you want an optimum solution. The number of infeeds, proximity to workers, future system needs, discharge points, manual or automated operations, safety devices, chutes, scissor lifts – all of these need to be analyzed to arrive at a sound decision.
Train For Conveyor Belt Safety
Conveyor safety and ergonomic material handling are essential to preventing unnecessary injuries and conveyor hazards. Training is needed to ensure worker safety so coach all new employees on how to use switches, emergency stops, and how to perform maintenance and other mechanical processes.
Design Workstations Ergonomically
When conveyor belts are used in combination with workstations, workers can develop musculoskeletal disorders. An ergonomically designed conveyor belt workstation will not only eliminate the risk of injury but also boost worker productivity. So make sure both the reach distance is convenient and the work surface height is adjustable. For standing jobs where the load is light in nature, 42 inches would work well and 30 inches is a convenient height for seated workers.
Choose The Right Belting
The right conveyor belt can greatly boost the performance of the conveyor belt system because it is the only part that comes in contact with the pulley and the product. The belt style, the thickness of the surface, the material of the conveyor belt, the installation, and the load requirements will determine your purchase decision. If you are in the food handling industry, then you would need to know the application and the load requirements in detail in order to select the right type of conveyor belt system.
Finally, an additional feature that is available with newer, advanced technology is the “loading zone” which efficiently meets the evolving needs of modern distribution centers by telling the difference between a load in transit and an inserted load.
Erich Lawson is passionate about saving environment by effective recycling. He has written a wide array of articles on how modern recycling equipments can be used by industries to reduce monthly garbage bills and increase recycling revenue. You can learn more about environment savings techniques by visiting Northern California Compactors, Inc blog.