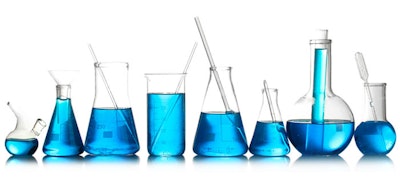
Isocyanates are critical building blocks for high performance polyurethane based polymers that make up coatings, foams, adhesives, elastomers, and insulation. With demand expanding globally, the market for isocyanates is expected to grow to $39 billion by 2019. As manufacturing volume rises, worries have increased over both product quality and the toxic health impact of residual isocyanates. In 2015, concerns over exposure to residual isocyanates led the Environmental Protection Agency to issue new actions extending the Toxic Substances Control Act in order to limit residual isocyanates in new products.
Controlling isocyanate reactions begins with process understanding. Yet, traditional analytical methods for measuring the residual isocyanate (NCO) concentration using offline sampling and analysis introduces concerns such as:
- Long wait times for offline analytical results making it impossible to make real-time decisions, leading to inconsistent product quality and reduction in production capacity
- Sufficient process knowledge lacking at any given time point
- Exposure to NCO samples increasing the risk of sensitization and human health risks
In situ monitoring with process analytical technology addresses these challenges. Specifically, in situ mid-IR spectroscopy with an attenuated total reflectance (ATR) sensor is an ideal choice due to its selectivity and sensitivity. Inline spectroscopy offers a very straight forward way to monitor reaction initiation, progression, conversion, intermediate (transient and/or highly reactive) formation, and end-point in real time. It can quantify NCO, polyol, by-products, and pre-polymer concentrations under reaction conditions without taking samples for offline analysis. This enables manufacturers and formulators to ensure that product quality specifications, personnel safety, and environmental regulations are met.
In the following example a diisocyanate reacts with a polyol (Scheme 1). Several critical process parameters may affect the residual diisocyanate in the product including temperature of the reaction, quality of the incoming starting material, feed rates, reaction kinetics, and reaction time.

To track reaction progression, a probe based FTIR instrument (ReactIR) was inserted directly into the vessel for the duration of the batch. Mid-infrared spectra were recorded every 60 seconds and plotted over time creating the three dimensional waterfall graph as shown in Figure 1. This plot depicts how a decrease in reactants is concurrent with an increase in the product as time progresses.
Figure 1. Waterfall plot tracking the reaction from Scheme 1 over time. X axis is Energy (wavenumber cm-1), Y axis is Absorbance Unit, and Z axis is Time (hours)The reaction components are easily detected by the distinct peaks as shown in Figure 1 (using conclusive functional group peak assignment, peak at 2270 cm-1 is the NCO functional group of the reactant while peak at 1740 cm-1 is the C=O functional group of the prepolymer). Reaction progression, a plot of the relative concentration of each reaction component as a function of reaction time is depicted in Figure 2. The mechanism can be explained and kinetics of product formation can be calculated from the information. The reaction endpoint is precisely detected three hours after initiation.
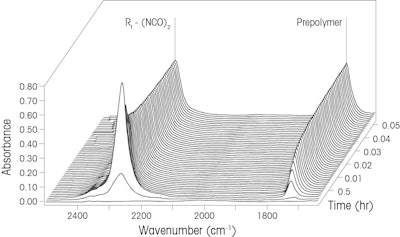
Figure 2. Two dimensional peak profiles trending reaction components over time
To confirm that the NCO concentration meets specification, samples were extracted and the residual NCO concentration was measured via the titration method [ASTM D2572-97(2010)]. These results are then correlated to the mid-infrared absorbance values of the diisocyanate component trend as shown in Figure 3. The diisocyanate concentration does not reach zero because the prepolymer product contains unreacted NCO functional groups.
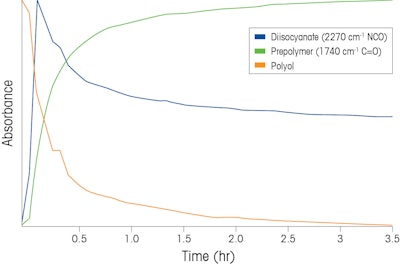
Figure 3. Diisocyanate trend overlaid with offline titration measurements confirming the remaining NCO concentration
After validating the measurement and confirming that yield and purity meet specifications, it is possible to use the real-time trends depicted in Figure 2 to set process control limits on the reaction progression for each reaction component. If a trend deviates from expected values, the in situ measurement can immediately detect the change from optimum or expected and provide engineers and plant operators with the opportunity to make the necessary corrections during manufacture of the prepolymer. Such actionable information available in real time reduces or eliminates the potential for out-of-spec batches; reducing or eliminating the need to re-work batches that don’t meet quality standards.
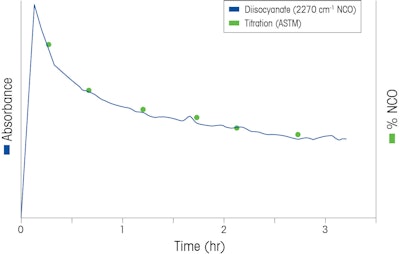
Process Understanding: Seeing is Believing
Monitoring isocyanate reactions using in situ mid-infrared spectroscopy (ReactIR) allows manufacturers and formulators to “see” what is happening with their chemistry as it occurs. It enables on the spot and fast decisions about dynamic process parameters or conditions. Armed with increased reaction understanding, research scientists, engineers, and plant operators are able to quickly optimize and scale up processes with increased robustness and quality. This enables a safer work environment and ensures residual NCO concentration meets specifications, while optimizing production capacity and lowering operating costs.
Brian L. Wittkamp, PhD, is the Market Development Manager at Mettler Toledo AutoChem