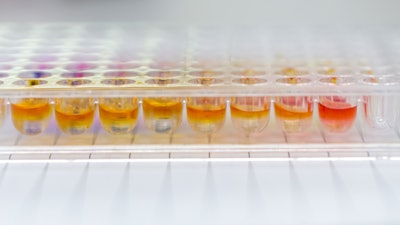
Each year, billions of well plates are manufactured for research, drug discovery and diagnostic testing. Although many are inexpensive consumables, an increasing percentage require more sophisticated surface modification and functional coatings from labware manufacturers.
This surface modification aims to improve the adhesion or proliferation of antibodies, proteins, cells and tissue and improve the signal-to-noise ratio for high-resolution testing with less target material or markers required.
Unfortunately, there are limitations to this approach. Pre-coated well plates are expensive and the functional coatings may only suffice for more straightforward research or testing requirements. A more customized solution is often required for cutting-edge R&D and diagnostic test development.
When this is the case, an increasingly popular alternative is contract services that can apply functional coatings optimized explicitly for the application. In this arrangement, inexpensive, uncoated labware is purchased and delivered to the contract service provider for plasma treatment.
Surprisingly, this approach often lowers coated labware costs while providing high-quality standards. The savings can increase at higher production volumes, given the contract service providers' ability to scale up and move to higher-capacity plasma treatment tools.
The savings can increase at higher production volumes, given the contract service providers' ability to scale up and move to higher-capacity plasma treatment tools.PVA TePla
Plasma Treating Well Plates
Well plates are a standard tool in analytical research and clinical diagnostic testing laboratories. The "wells" that function as small test tubes are used to perform many tests at a time while keeping the test environment the same.
Well plates are manufactured using polystyrene primarily because the material is stable and allows for the long-term containment of chemical compounds. It is biologically inert and provides good optical clarity.
Other polymers like polypropylene, polycarbonate and sometimes glass are used for applications that must withstand a broad range of temperatures, such as polymerase chain reaction (PCR) for DNA amplification.
However, untreated synthetic polymers are extremely hydrophobic, providing inadequate binding sites for cells to anchor effectively to their surfaces.
As a result, plasma treatments are used to solve problems with well plates that are difficult to be resolved in other ways. Plasma is a state of matter, like a solid, liquid or gas consisting of energetic species such as electrons, ions, radicals, neutrals and radiations.
When enough energy is added to a gas/monomer, it becomes ionized into a plasma state in which the collective properties of active ingredients can be controlled to clean, activate, chemically graft and deposit a wide range of chemistries into well plate coatings.
For vitro diagnostic substrates, treating the well plate with plasma can improve adhesion promotion and conjugation of bioactive molecules; this is done by providing a particular chemical functionality at the surface, allowing covalent coupling of biochemical species to occur. Amino, carboxylic, hydroxyl and epoxy functionalities are readily obtainable chemistries using gas plasma surface treatment.
Biomolecule attachment, survivability and proliferation can be improved on well plate surfaces using plasma to create a hydrophilic surface using hydroxyl, carboxyl or amine groups. The surface treatment can also enhance the analyte wetting of wells, facilitate cell proliferation without clumping, reduce the serum, urine or reagent required for testing and lower the risk of overflow or cross-well contamination.
With a background in plasma equipment manufacturing, a provider like PVA TePla can provide critical insight on validation, production methods, fixturing, hardware and software modifications.PVA TePla
Creating Custom Coatings
When problems occur with uncoated or off-the-shelf well plates that inhibit research or production, researchers or manufacturers often utilize contract services from a provider like PVA TePla; they are skilled in applying these types of functional coatings which can speed the time to market and eliminate the need to invest in equipment and expertise in-house.
Working with an experienced contract services provider also has tremendous advantages when tapping into years of technical expertise. In many cases, PVA TePla has already developed solutions to similar challenges. This experience can speed development efforts significantly. Companies like PVA TePla are also accustomed to working under strict NDAs since customers often do not want to disclose more information about their specific research than necessary.
Some contract services providers provide access to on-site research and development equipment and engineering expertise. PVA TePla, for example, often invites labware manufacturers to visit its lab in Corona, CA, to run parts and conduct experiments on in-house equipment, with complete customer involvement. The customer can access Ph.D. scientists and surface, polymer, physical, bio, organic chemists, engineers, plasma physicists and metallurgists there.
In addition to providing many options for functional coatings, a skilled contract services provider can develop and document an optimized range of processing parameters to ensure the optimum quality of the treated well plates.
When it is time to transition from R&D to production, working with an experienced contract services provider also has advantages. With a background in plasma equipment manufacturing, a provider like PVA TePla can provide critical insight on validation, production methods, fixturing, hardware and software modifications. Examples include special hardware for batch processing, such as a mass flow controller, a different pump configuration or unique chamber sizes.
A proficient contract services provider also has the equipment and expertise to seamlessly scale up from R&D to production. PVA TePla has multiple systems and can scale rapidly, allowing for rapid increases in production volumes.
This includes an R&D tool for lab work and a production tool with a larger volume chamber designed to run at higher capacities. Frequently, moving from R&D to production will substantially lower the price for coated well plates since the entire process from receiving, handling, processing, testing and repackaging is pre-determined using the largest chamber sizes to facilitate higher volumes.
For researchers and manufacturers interested in reducing the costs of coated well plates while improving research quality and diagnostic test resolution, outsourcing to a qualified contract services provider could be the solution they seek.