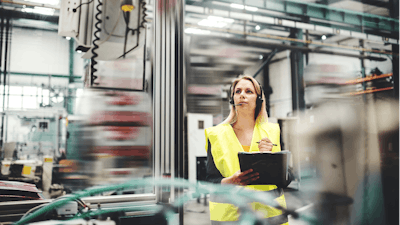
Key performance indicators, or KPIs, are put in place to expose the problems that are plaguing processes in our manufacturing plants so we can improve them. The reality is that all too often, those KPIs actually lag behind the point of occurrence of problems as they happen. They can also require study and interpretation before the problem that the KPI is pointing to can be identified. There is no chance to "stop to fix" and the data becomes disengaged from the process that the KPI is designed to monitor. The KPIs lack real-time problem identification.
Would some means of better alignment between a KPI and the actual process improve the situation? AND what about a meaningful visual control and a less top-heavy method of application? An answer can be found in the application of some basic LEAN tools and a fairly simple continuous improvement approach to monitoring the process you are wishing to support.
Defining the Process
To get started, the process in question must be committed to standard work (the verb). That involves a legitimate time observation and documentation (in granular, non-engineering speak detail) on a standard work combination sheet. This gives you a realistic "least waste way" (as we currently know it) view of the process in question. Using this, a time-based appreciation of the process (when it runs as intended) can be compared to the realistic time we intend to man/run the process. And now, we have an actual idea of what output from the process we can expect over that time. It is important to remember that time is (strictly speaking) a function of the things we do within that time. If those things we do are repetitive and accurately predicted, the time it takes to produce the output of the process will be equally predictable. It is when unexpected elements/abnormal process conditions occur that the time it takes to perform that process output will change. That is one key.
iStock
Identification
Now comes the task of identifying exactly when such abnormal conditions occur, or as close to when they actually occur as possible (in "real-time"). This can be done by creating a visual control that reflects the output expectations calculated through the standard work over the realistic time(s) we intend to run the process. One such visual control can consist of a simple hour-by-hour chart and an equally simple way of raising a red flag when output does not match the expectation as soon as it occurs, so somebody can come over and ask "Why, Why, Why" (optimally five times). Of course, this does require that someone is available to do so, but underestimating the importance of this task is to give away golden opportunities to catch opportunities to improve the process, which can be thought of as "Red Dots" (which are good, not bad) ... but more on that in the next paragraph. It is important the be realistic and thorough with the assessment of time available on an hour-by-hour chart. It is not enough to divide the workday by eight even hours. The consideration of time available must be very deliberate. For instance, in an individual hour where we expect the operators to take a 15-minute break, there are only 45 minutes remaining in which to perform the process. That particular hour on the chart must represent that. This is the only way the hour-by-hour chart will have credibility. This is another key. By the way; a desirable by-product of attention to that detail is that the credibility of the document will extend to the process operators, an integral necessity of the system.
iStock
Real Data over Gut
As I mentioned in the preceding paragraph, it takes a human support system to attend to all this information that the standard work and the visual control will provide. Do not underestimate the volume of information — Red Dots — which will come out almost immediately, once such a system is set in place. It is not enough to simply roll out the tools. They won't take care of themselves and goodness only comes from showing up (and, by the way, your workforce will immediately know the difference). The time required to attend to the new information delivery system may have to come out of time that is already being spent by support people assembling information to feed the conventional KPIs that management is accustomed to seeing. This is the part where the organization may have to learn a new LEAN language with which to convey the status of the process. Instead of OEE values or some other quotient-based score, officers of the company may have to learn to count Red Dots. A confidence that greater amounts of goodness come with improving processes in real-time that support the business as coming out of those old John Allwood
What system could be stronger?
John Allwood is the author of "Standard Work is a Verb: A Playbook for LEAN Mfg".