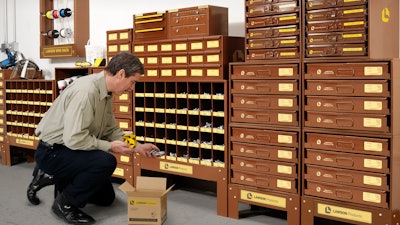
As a factory maintenance and parts supplier, Advanced Technology Services, Inc. provides custom solutions for businesses around the world. So when they decided to improve their approach to servicing and repairing their clients’ equipment, they chose a custom solution with Lawson Products. ATS helps growing industrial companies in the U.S., U.K. and Mexico by deploying its own employees full time to repair machinery and perform routine maintenance.
No two sites are alike due to each client’s unique operational needs, so having the right parts on-hand at the right time is critical. ATS saw an opportunity to seek a formal inventory management solution to organize and stock the many parts necessary to service and repair their clients’ equipment. Some locations managed their own inventory, while others outsourced the task to several suppliers—in some cases up to six suppliers—with different storage set-ups, schedules and inconsistent service. To complicate matters, mechanics wasted valuable time going off-site to pick up parts – sometimes as often as four times a week. “Our biggest challenge was not having the right items or being overstocked,” said an ATS spokesperson. “We worked closely with Lawson to capture the unique needs of each location and identify the right mix and right levels of product for each location.”
Customized Solutions, Standardized Reporting
Lawson provided a customized product assessment for 30 ATS locations nationwide. In addition, Lawson established consistent reporting and service across these sites. Lawson and ATS apply a stringent and methodical approach to measuring success using 5S, a standards-based approach to creating and sustaining workplace efficiency and effectiveness. After each site completed a 5S audit, an on-site Lawson representative developed a custom shop set-up unique to the tasks, behaviors and product needs of that site. All set-ups can be adjusted according to planned shutdowns or start-ups, market conditions or regular business cycles.
One facility, for example, required hoses made off-site simply because ATS didn’t have the product or equipment to make its own. Lawson, however, worked to understand the site’s needs and created a stocking program, including hoses, fittings and the hose-making equipment. The site’s dedicated Lawson representative also provided in-shop training to ensure safe operations. This solution resulted in annual savings of $46,500 at this ATS facility. After Lawson completed the custom shop set-ups, the representative applied a results-driven approach to ensure continuous improvement at every ATS site. Lawson conducts a 90-day 5S audit to track initial results with quarterly audits thereafter. Important audit criteria includes measuring the impact of having properly organized parts, efficiently placed set-ups, lean inventory levels and consistent service. To date, all the ATS locations serviced by Lawson have experienced an average of 200 percent improvement in efficiency and productivity.
Bottom Line Results
Lawson Products’ managed inventory solution gives ATS the ability to track part usage at each location. This helps the company compare stocked items across locations and share inventory as needed, reducing overall costs. Lawson’s scanning solutions and online ordering tools also provide ATS with a quick and easy way to reorder parts without having to leave the job site. Today, ATS operates more efficiently with Lawson’s managed inventory solutions. Instead of facing unreliable site visits from several suppliers, ATS has the right parts at the right time and a knowledgeable Lawson rep serving as a single-point of contact for its small-parts inventory. “Lawson takes full ownership of the vendor managed area and provides reliable management of our free access items that are critical to our operations,” an ATS representative said. “We have open lines of communications through all levels of the organization. Plus, knowing that Lawson is managing these products, we can focus on our maintenance services and other critical inventory items.”
For more information on Lawson Managed Inventory, visit www.lawsonproducts.com.