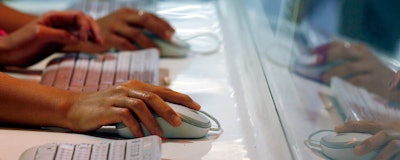
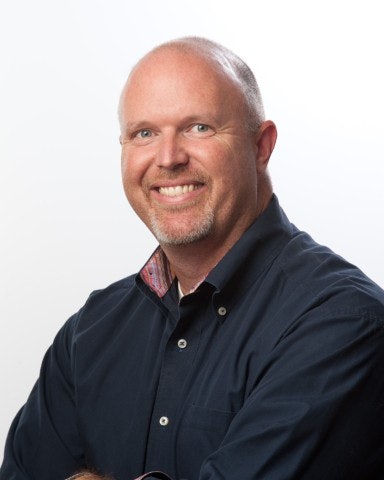
Smart Manufacturing is the moniker often used for factories with connected devices, integrated systems, and visibility across the full value chain. But, level of adoption varies greatly, with no standardization of what criteria must be present in order for a plant to be considered truly a Smart Manufacturer. A few sensors embedded in the assembly line machinery cannot realistically indicate a factory is “Smart” and meeting its full Business Intelligence potential. It may be more appropriate to evaluate achievement based on a sliding scale and level of growth. Some basic milestones, though, can help plant managers identify how their organization measures up to the competition.
Why Evaluation Matters
It’s generally well-known that parents like to brag about their little geniuses, whether they are toddlers reciting ABCs or college-bound students with near-perfect SAT scores. Officers and plant managers aren’t so different. They, too, have an innate desire to classify, label and extoll the achievements of their organization. From incentivizing employees to sharing bottom-line statements with stakeholders, manufacturers thrive on competition and achievement.
Smart Manufacturing vs. Business Intelligence
While some industry experts might quibble about the fine-line distinctions between Smart Manufacturing and Business Intelligence, most would agree that semantics shouldn’t interfere with practical day-to-day applications. No matter the labels, the facts are clear: Connected devices and integrated systems lead to improved insights, refined decision making and heightened Business Intelligence. Data, collected through smart devices and aggregated and analyzed through BI tools, can help draw conclusions about the past and predict the future.
Measuring How “Smart” the Organization is
Manufacturers must rely on survey results, benchmark data, and published case studies to determine if their organization is leading the pack or trailing in the competitive race to win market share. Here are some guidelines to help perform a self-evaluation.
Elementary: Mastering the basics
Connected systems. Smart Manufacturing has at its core a fully integrated software solution, including the ERP foundation, plus any specialized point-solutions which address specialized needs. All of the business solutions must integrate data to one view. The various divisions and locations should also be visible and easily accessible for one comprehensive picture of the enterprise’s health.
Connected people. The workforce needs to be connected, well-informed, and have access to role-related data, reporting and tools to help speed tasks and make insightful decisions. Personnel need access where they work and when, even if that means on the plant floor or outside of the plant.
Connected machines. Machine-to-machine (M2M) connectivity is not new to manufacturing, but the lower cost of smart sensors and the wider array of capabilities are changing the scale of applications and expanding use-cases. Machinery on the shop floor, material handling equipment, vehicle fleets, service vans and shipping containers can all be equipped with smart sensors to measure location and physical characteristics, like temperature, speed and moisture. This data can be used to predict arrival, measure performance, spot anomalies and predict maintenance requirements.
Connected supply chain. To be competitive today, connectivity should expand beyond the organization’s four walls and encompass visibility and communication with contractors, partners and suppliers. This can take the form of online portals, collaboration tools, Internet of Things (IoT) connected devices and product configurators which help plan product customization. The underlying purpose is to speed transactions, automate responses and improve relationships.
Connected products. Manufacturers do not need to lose awareness of their products just because they leave the plant. Smart sensors and IoT technology allow manufacturers to gather and aggregate contextual data about the product’s performance. This type of insight about product performance or consumer habits can help designers improve the value of the product.
Intermediate: Applying Concepts
Speed processes. Once the basic systems, sensors and personnel are in place, the enterprise can work on reaping tangible results. One of the first applications of connected Smart Systems is to speed response time. The enterprise-wide visibility will eliminate silos and gaps in communications, increasing agility, reducing cycle times and improving on-time delivery to customers.
Prevent downtime. Collecting and analyzing sensor-generated data from shop floor machinery can be used to predict machine failure and to intervene early — before there is a breakdown.
Improve profitability. Data collected throughout the manufacturing process can point to gaps or roadblocks where quality, productivity or efficiency errors tend to occur. Data can also be used to automate activities, reduce waste, eliminate redundancies and minimize “just in case” back up inventory.
Advanced: Formulating Strategies
Understanding history. Data collected from machines, systems, and processes can be used to delve into reasons behind occurrences, as well as find influencing factors and related trends. This look backwards helps the enterprise fully understand the cause and effect of policies and related outcomes, plus create strategies based on proven results.
Projecting the future. Business Intelligence truly takes on advanced capabilities when it not only looks backward but projects the future, helping the enterprise anticipate product trends, customer preferences and pricing variables. This allows the company to prepare with the right materials, personnel and inventory necessary to meet changing needs.
Creating value. Data and insights from data can be turned into revenue streams and value-add offerings for customers (B2B as well as B2C). Insights about product performance can be transformed into educational materials and be used to help build relationships with customers. Data can be packaged and marketed to other target markets as well, creating new business models and opportunities for growth.
Concluding Insights
How does your organization measure up? No matter whether your plant is deploying basic Smart Manufacturing concepts, or has graduated to more advanced strategies, remember there’s no limit to learning and insights. Business Intelligence is a continuous process, with expanding results. The key is to start with an open mind, a desire to discover, and a commitment to improve.
Mark Humphlett is Senior Director of Industry and Solution Strategy at Infor.