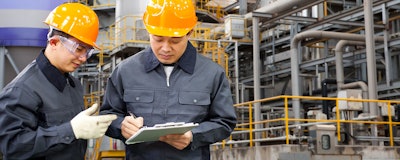
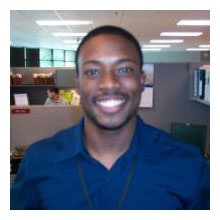
Balancing short-term operational requirements with strategic planning and goals can be a juggling act for facility managers — especially when you consider that a commercial or industrial facility is made up of a complex network of electrical, electronic, process and control, automation and building management systems. When day-in/day-out facility issues arise, the facility manager is the go-to person.
From a strategic viewpoint, a facility manager should be aware of external trends that may impact decisions about future operations, which include:
- Aging facilities and budget gaps are forcing organizations to operate and maintain with fewer resources.
- The number of retirement-eligible skilled workers is growing, making it increasingly difficult to hire, develop and retain qualified staff.
- Businesses are choosing to outsource services and engage in strategic partnerships.
- Risk management must be addressed for issues related to worker safety. According to OSHA/NFPA 70, electrical equipment must be maintained to avoid unplanned outages, which may have a negative impact on worker safety.
- Technology continues to impact how facility managers do their jobs and buildings operate. Smart technology can be incorporated into a building’s infrastructure for enhanced communications and monitoring.
- There is an escalating demand for sustainable solutions. Upgrading to modern technology enables facility management to ultimately reduce operating costs.
When decisions are made — whether it affects daily operations or strategic goals — safety and electrical reliability should never be compromised.
Reliable Power: The Heart of Facility Operations
Electricity is an often ignored commodity — unless we’re forced to pay attention. Maintenance is a vital component in supporting electrical workplace safety, business continuity and optimized total cost of ownership. Section 4.2.1 of NFPA 70B-2016 best sums up the case for having a maintenance strategy in place:
“A well-administered electrical preventive maintenance (EPM) program reduces accidents, saves lives, and minimizes costly breakdowns and unplanned shutdowns of production equipment. Impending troubles can be identified — and solutions applied — before they become major problems requiring more expensive, time-consuming solutions.”
Planned vs. Unplanned Maintenance
Plant managers should proactively schedule and employ a variety of approaches to maintain electrical distribution equipment. Even though reactive maintenance activities typically cost three to four times more, planned maintenance activities are often deferred due to high productivity objectives and tight maintenance budgets.
Regularly scheduled preventive maintenance, based upon manufacturers’ recommended guidelines, is the traditional planned maintenance strategy. These activities are often conducted during end of year shutdowns to minimize the impact on business operations. Less complex tasks, including routine monitoring and inspections, are recommended between planned shutdowns to ensure the electrical equipment is kept clean, cool, dry and tight.
1. Keep It Clean: The accumulation of dirt in an electrical enclosure can result in electrical tracking, which can cause arcing, especially during high humidity conditions. Another issue is most electrical equipment relies on unobstructed air circulation to cool the equipment. Dirt and dust accumulations can restrict airflow and affect the equipment’s ability to remain cool. Enclosures and equipment rooms should be properly sealed to keep rodents and vermin out. Finally, traffic in/out of electrical room should be kept to a minimum to help keep out additional dirt and dust.
2. Keep It Cool: Heat build-up in electrical equipment can shorten its life span. Electrical equipment generates heat due to current flow. Normal room ventilation typically removes the heat. Ensure adequate ventilation is provided for electrical equipment and the ventilation equipment is properly maintained. Additional causes of excessive heat build-up that could shorten the lifespan include:
- Overloaded circuits or poor quality connections
- Operating electrical equipment for extended periods at elevated temperatures.
3. Keep It Dry: Water and electricity don’t mix. Any moisture in or around electrical equipment is a safety hazard and should be corrected immediately. If moist surfaces are noted, identify and eliminate the source. If it cannot be completely eliminated, take steps to protect equipment from the harmful effects of moisture.
Any prolonged exposure to moisture should be examined by a qualified electrician. Damage should be properly repaired immediately. Moisture can damage equipment — even if an electrical failure does not occur — leaving the equipment unreliable and unsafe. It should be closely examined and tested by a qualified electrician to determine if parts can be repaired or replaced.
4. Keep It Tight: Loose connections are a major cause of electrical failures. A proper electrical connection is mechanically and electrically secure. Qualified electrical contractors may be called in to ensure the integrity of electrical connections. As loads vary, the metal portions of the connections will expand and contract, which is normal. They may require re-torquing, as a loose connection presents a high resistance to current flow and generates heat.
Hot spots are a major source of electrical failures, including fires. Thermographic (infrared) tests may be employed to detect bad connections and hot spots. These inspections should only be performed by a certified thermographer.
Conclusion
Like any engineered system, electrical power distribution systems cannot be designed and constructed to operate 100 percent of the time indefinitely. To help ensure electrical reliability, facility management should:
- Make room in the OpEx budget for planned maintenance activities.
- Put a strategy in place to optimize the budget and reduce unplanned downtime.
- Inspect equipment on a routine basis to ensure the equipment/electrical room is tight, clean, cool and dry.
- Monitor equipment periodically to ensure there are no loose connections or hot spots.
The failure of electrical system components is three times higher without maintenance activities and in some cases, more (source: IEEE). The best way to avoid this financial impact is to reduce the risk, which requires time, effort, planning and money. A comprehensive maintenance strategy should incorporate all electrical power distribution equipment, regardless of the manufacturer, to ensure that electrical equipment and components operate safely and reliably.
Jeramy Freeman works in sales, marketing strategy, offer development and product marketing with Schneider Electric.