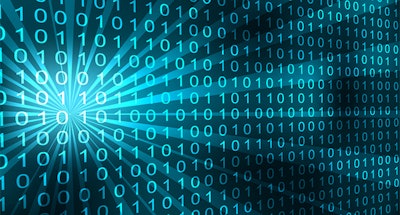
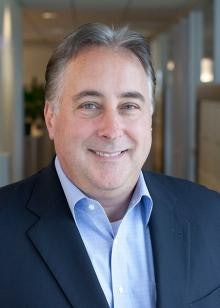
Now that the age of big data is really here, manufacturing companies have truly game-changing opportunities to increase operating efficiency and productivity — and even explore new “digital” business models taking advantage of the Internet of Things. However, a big obstacle stands in their way: manufacturers’ extraordinarily data-rich and complex global supply chains are generating digital data at an unprecedented — and frightening — pace. And to a large extent that data is not standardized, not necessarily secure and inherently complex when integrated with existing data. Most manufacturers simply can’t make sense of it all, so important business insights are obscured or, in some cases, simply wrong.
Yet the opportunities are large enough to make clear that “winners” in the big data age will be those manufacturers that can master currently out-of-control data proliferation and then analyze their data for important business insights. This is part of the impetus for EY to create an alliance with GE Digital to help manufacturers put to good use the data generated by the emerging industrial internet of things (IIoT) networks.
Manufacturers’ Big Data-Age Opportunities
Here are manufacturers’ big-data-age opportunities as EY sees them:
• First, the latest and most advanced sensors, networks and big data analytics make it possible for manufacturing companies to know when their equipment is running well and can even predict when it is likely to break down. Preventive maintenance can be directed precisely where and as it’s needed, enabling new streamlined and lower-cost operating models.
• Second, the same sensor networks and predictive analytics make it possible to enhance the efficiency of industrial capital assets in action. Case in point: adjusting the angle of turbine generators blades and the structure’s orientation in real time can significantly increase electrical generation over simply “pointing the machine into the wind.”
• Perhaps most valuable will be the entirely new kinds of business opportunities that deep analysis of large data sets makes possible. Think about the impact of spreadsheets, which at first simply made financial record-keeping more efficient by replacing pen and paper. But once we had these spreadsheets, we could create formulas and run what-if analyses; that spawned modeling, which led to major change in many industries. The IIoT is about to sweep in at a similar magnitude and offers the chance for true business innovation for manufacturers.
The Huge Data Proliferation Challenge
And yet … nearly every company I talk to tells me they are being held back because of their inability to manage the rising mountains of data. Low-cost cloud storage solutions are encouraging them to save all the data they can find, regardless of whether its business utility is established. Consequently, data is driving complexity, cost and risk, and actually inhibiting a manufacturer’s ability to engineer the connected and insightful digital supply chain ecosystem they need to realize value.
According to IDC, as of 2014, we were creating data at the rate of 1.7 megabytes of new information, every minute, for every person on earth. In the same report, IDC says the cumulative total of the world’s digital data reached 4.4 zettabytes by the end of 2013 and, by 2020, we will be creating 44 zettabytes of new data every year (one zettabyte equals a trillion gigabytes).
Data Volume and Complexity Obscures Manufacturing Insights
Manufacturing executives reading those numbers may well find them frightening. The report, Digital supply chain: it’s all about that data, finds that rising data complexity may well present an existential challenge to manufacturers and their supply chains. The sheer volume of data they produce, and its growing complexity, actually inhibits executives’ ability to access the right business insights at the right time to empower better decision-making. Thus, proliferating data creates a chaotic and counterproductive level of complexity that has the potential to actually harm businesses.
Cost and Compliance Rsk Also Rise as Data Proliferates
Manufacturers’ big-data-era challenges don’t end with hidden insights and growing complexity. Storage solutions may seem inexpensive at first, but costs rise quickly when you’re capturing all the data produced by manufacturers’ digital supply chains. A survey of nearly 1,500 Europe, Middle East and Africa (EMEA) companies reported that a midsize company with 500 terabytes of data is likely spending roughly $1.5 million per year in storage and management costs to support nonessential data.
That doesn’t even count the related compliance risk. Manufacturers storing everything for later analysis may put themselves at risk of accumulating sensitive data not in compliance with new regulations. The EMEA survey found that, on average, 54 percent of the data collected by respondent companies was “dark data,” the contents of which was unknown — and companies could only identify 14 percent of their data, on average, as business critical.
But take heart. Our experience tells us there is a solution. It requires three key steps, and simply betting on better technology is not an option.
First: Enterprise Data Strategy
We believe the first step is for manufacturers to make enterprise data management strategy a core foundational element of their digital supply chains. This is not conceptually hard. Take your organization’s long-term business goals and develop related key hypotheses — i.e., the questions that matter most to achieving those goals. Then identify the data you must capture to answer those questions, today and tomorrow. Optimization of manufacturing operations happens only when data is analyzed in the context of key hypotheses.
Second: Integrate That Data
Enterprise data management strategy requires a unified enterprise view of data. Manufacturers with many incompatible data analysis tools in different business units must find a way to integrate that disparate data into a unified enterprise view. One approach is to choose one data analytics platform in which to aggregate data from the others. But recent technology advances make possible another approach using advanced machine learning tools that automate data processing, alignment and visualization, enabling you to automate the process of aggregating and classifying data from all your disparate systems.
Third: Focus, Simplification, Standardization
This is where your enterprise data management strategy proves its mettle. Use it to instruct the development of data classification taxonomies that focus and simplify the rest of the data management and analytical process. This helps standardize data taxonomies across the organization and enable more focused data acquisition and analysis. In my experience, the highest-value business insights are being achieved by organizations that thoughtfully classify and analyze their data in the context of key questions that matter most about their business.
Ask the Right Questions to Gain Insight — and Avoid Extinction
Big data age manufacturing companies must be prepared to continuously evolve their supply chains, business models and operational processes concurrently with their customers and markets, in real time. Doing so demands that you ask the right questions — questions that provide real value and help to achieve your business goals. Those questions and related hypotheses drive successful enterprise data strategy, which then instructs classification taxonomies and more focused data acquisition and analysis.
Asking the right questions can put manufacturers on the path from strategy, to simplification, to the business insights needed to overcome big-data-age challenges and achieve the three IIoT opportunities described at the outset of this article. The alternative is a dangerous path down which chaotic data proliferation is pointing many manufacturers: from threat, to disruption and then extinction.
Dave Padmos is Global Technology Industry Leader of Advisory Services at EY.