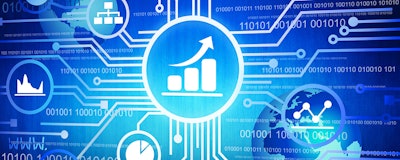

Outsourcing and offshoring continue to be major manufacturing trends today. And, as the amount of external manufacturing grows relative to in-house manufacturing, so do the number of quality events. From 2004 to 2013, FDA drug recalls increased by an unprecedented 600 percent. This surge is especially troubling as global supply chains become more and more complex.
One option for reducing these quality issues throughout the supply chain is for manufacturers to better leverage data analytics.
With the high levels of merger and acquisition activity, it has become increasingly difficult for manufacturing companies to sift through all of the relevant data due to integration issues, legacy systems and just the sheer amount of information that each company maintains in multiple formats.
In order to collect the necessary information for reports or trend analysis, companies need to pull data from different files, across various systems, and then manually combine those results for reporting. As you would expect, there is plenty of room for error in that scenario, so the most efficient solution is one system to house, consolidate and organize the multitude of data previously stored in various locations.
Analytics professionals are a critical component in making sense of quality data. By identifying and analyzing opportunities to improve the company’s profitability, analysts turn data into information and then translate that information into actionable insight to influence business decisions.
It is in a company’s best interest to hire people who understand the health of the organization by reviewing and analyzing data. Manufacturing data analysts, in particular, need to have a firm grasp of compliance and regulatory issues by continuously monitoring performance and quality controls to prevent issues from arising in the first place. Having someone in-house that can determine or predict where the company’s strengths and weakness are by tracking data trends, is critical for the success of the company.
Think of it as having your own personal doctor monitoring the health and financial wellness of a company on a regular basis. This “doctor” provides enterprise-wide visibility and equips manufacturing executives with the insights needed to make proactive changes. Rather than waiting for a quality-related failure, the executives can identify leading indicators and intervene before a minor issue becomes a critical and costly impediment in the manufacturing process.
The inability to obtain data when needed and a lack of an appropriate methodology to interpret said data significantly reduces visibility — preventing the true root cause of an issue to be identified in core quality systems.
Companies then waste considerable time and effort on the wrong problems and corresponding corrective actions. As this negative cycle continues, companies often find themselves in a perpetual state of being reactive, and leading to citations by regulators for quality deficiencies.
Additionally, manufacturing companies risk having faulty products distributed to consumers, forcing a recall of products from store shelves, hospitals, homes and more. Depending on the severity of the defect and the safety impact to consumers, this could cost the company considerable resources, budget and time invested in product investigations, repairs or other product dispositions. Recalls also stem from quality issues that are neglected or unaddressed before the product is distributed out to consumers.
By creating a process to trend and leverage data insights from the very beginning of a product’s lifecycle, a company is positioned to have successful inspections at any given time, without massive efforts invested in inspection-readiness preparations. Active and effective use of analytics provide the necessary foresight for manufacturers to focus on maintaining the quality of their products and maintaining trust with consumers, while being more predictive in preventing the “snowball” momentum that leads to systemic quality issues.
Joe Goodman is Director of Solutions Consulting at Sparta Systems.