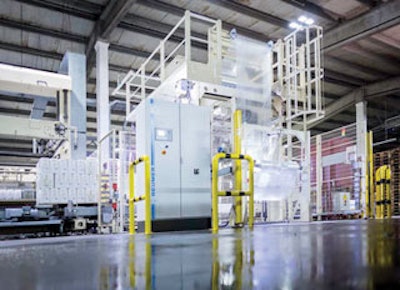
In order to transport palletized beverage cartons to the central warehouses and distribution centers of the customers, the German market leader for sparkling wine, Rotkäppchen-Mumm Sektkellereien GmbH, Freyburg (Unstrut), decided to equip two of its production locations with the BEUMER stretch hood M high-capacity packaging systems. These systems package the palletized beverage cartons quickly, flexibly and sustainably with a stretch hood film. In Eltville on the Rhine (Hesse), BEUMER has adapted the packaging system so that the film size is changed with respect to the pallet size. These systems enable the Sektkellerei company to reduce shipping and complaint costs considerably in the medium term.
The Rotkäppchen-Mumm Sektkellereien GmbH headquartered in Freyburg at the Unstrut in Saxony-Anhalt is leading producer of sparkling wine in Germany. They are also one of the top producers of various spirits and wines. Owing to their production of exclusive wines, the Rotkäppchen-Mumm Sektkellereien hold a "Sparkling wine" market share of approx. 50 percent in the food trade.
The company group currently has around 550 employees and produces at five different locations in Saxona-Anhalt, Thuringia, Hesse and Baden-Württemberg. Production Manager Karl-Josef Lauzi describes the Hesse Sektkellerei: "In Eltville on the Rhine near Mainz, we have a very traditional location". Lauzi has been working for the Sektkellereien for over 30 years and is responsible for the entire Rotkäppchen-Mumm production operation. Lauzi explains, "the company was founded in 1811. The well-known sparkling wine brands are Mumm, MM Extra and Jules Mumm; all of which are produced at this location."
The various beverages are filled and bottled automatically, closed with cork, agraffe and capsule and provided with a corresponding label. Next, they are packed into different cardboard boxes. The packaged bottles are picked up by a palletizer, which stacks them onto pallets. Prior to implementing BEUMER technology, the upper surfaces of the cardboard boxes were glued and transported to a binding machine where the palletized beverage cartons were tied up. Beverage cartons would then be carried through the pallet transport system to the goods issue - where they can be prepared for the shuttle truck of the logistics service provider.
Every year approximately 300,000 pallets leave this location. However, in the past, due to frequent hard braking, sudden steering moves and sharp curves, during transport, cartons loosened themselves from the compound, falling onto the loading space. The result was broken bottles and lost product. "For a faster material flow in their central warehouses many customers rely on automatic loading and unloading systems," says Lauzi. This requires product to be sufficiently secured and protected.
Safer, More Stable and Especially Sustainable
In order to reduce damage during transport and to meet the increased logistics requirements, Sektkellerei searched for a packaging solution to ensure safer and more stable beverage stacks. "At the beginning of 2012, the Engineering and Logistics departments contacted us with a concrete request", recalls Klaus-Dieter Enzenbach, Sales Manager at BEUMER Maschinenfabrik GmbH in Beckum. In order to demonstrate their innovative engineering, BEUMER invited the Sektkellereien team to Beckum to carry out packaging testing of their products. "In the testing hall, the impressive BEUMER stretch hood M, high-capacity packaging system, was presented", proclaims Joachim Engler.
After testing, the benefits of the stretch hood became clear and both the shrink wrapping and the stretch wrapping techniques were eliminated as packaging options, as they did not meet Sektkellereien's requirements due to high film consumption. "The BEUMER high-capacity packaging system pulls a 40 micrometers thin film hood over the palletized beverage cartons. Optimally packaged, the cartons are protected against damage during transport and reach the customer in perfect order," says Engler. "Moreover, two different pallet sizes can be packaged with this multi-format system. The change is semiautomatic and it is not necessary to retrofit the system. Thus, we are well prepared for future requirements".
In order to demonstrate the conformity of the product and the increased stability of loads packed with the BEUMER stretch hood M, BEUMER and Rotkäppchen together with DEKRA, the world's leading expert organization for safety, quality and environmental protection, performed different driving tests under extreme conditions. The results were favorable and in March 2013, BEUMER was awarded with a contract including supply, installation and commissioning of the high-capacity packaging systems.
Sustainability Black and White
Both loading stability and sustainability were critical decision making factors for Sektkellereien. In support of our commitment to deliver sustainable material handling solutions, BEUMER Group has developed the BEUMER Sustainability Index (BSI). This validation system is used to evaluate the sustainability of new machines in a continuous, systematic and verifiable way on three comprehensive levels: economics, ecology and social responsibility. Economic performance, market presence, financial opportunities and risks are well-known parameters. BEUMER products will only become economically sustainable, when they and the corresponding production processes are tailored to long-term customer use. The BEUMER specialists evaluate the value of each product, not just their cost. If we consider the BEUMER stretch hood series for example, an intuitive human-machine interface simplifies operation and makes quick work of film roll changes. Operating parameters can be changed as well. Furthermore, this system is highly energy efficient.
BEUMER technical experts, in cooperation with film manufacturers developed a solution to meet specific needs and requirements. "If the filled bottles on the pallets are exposed to extreme heat and sunlight during transport, this may result in the formation of condensation," explains Enzenbach. "In such cases a perforated film is used, which enables the water steam to escape". Another special feature of this thin film is: after utilization, the film can be returned into the multi-cycle system and recycled - thus considerably reducing packaging waste.
Accurate Insertion into the Packaging Line
The BEUMER stretch hood construction series is a modular system, which can be adapted flexibly to the individual requirements of the user. "To allow better handling of the perforated films, we have designed a special device", explains Enzenbach. Conveyor transports the stacks to the packaging system. Here, a film hood is pulled over the palletized beverage cartons.This device makes sure that the film is picked up without any problems either by the gripping system or the suction unit. Particularly with perforated, thin film, there runs a risk of the holes interlocking at the cut edges due to the punching process. The conveying technology was also adapted and is now able to transport different pallet sizes to the BEUMER stretch hood M.
A challenge for the BEUMER specialists was the time frame during which the system had to be installed and commissioned. "We had exactly three weeks", recalls Enzenbach. The location stops operation only once a year in summer. During this period machines and systems are subject to extensive service measures. "It was this time, we were expected to insert the BEUMER stretch hood accurately into the line", explains Enzenbach. This phase of the project was concluded without issues. The new packaging system has been successfully running since August 2013.
A conveyor is used to feed the palletized beverage cartons into the packaging system. The innovative control technology automatically recognises different stacking heights and adapts itself accordingly. An ultrasonic sensor determines the required film length. The film is then cut and sealed along the cut edge. This forms a hood, which is stretched, pulled over the stack and down underneath the pallet base ensuring more retention force by a special base reinforcement. The BEUMER stretch hood system acts on the high contracting forces of the film. This fits the entire stack snugly "as a second skin" and provides the required stability. This quick and efficient packaging process protects goods from the environment. The palletized goods are clearly visible due to the smooth surface of the transparent, highly flexible film. This enables packaging of up to 100 pallet loads per hour. The hooded pallet is then guided to the shipping area by a conveying system.
Optimal Service
To ensure a trouble-free course of the intralogistics processes, BEUMER Group offers optimal service and maintenance after commissioning with their Customer Support Team. "The service concept is individually designed for and in cooperation with the customer", explains the BEUMER specialist Enzenbach. This includes inspections at regular intervals as well as planning and availability of spare or replacement parts. In case of system failure or disruptions, teleservice is available around-the-clock with the BEUMER Hotline. Furthermore Joachim Engler, head of the Engineering Department and his team are aware that the system and all components can be easily accessed by maintenance personnel.
"Since its installation the BEUMER stretch hood M has been running very stable", says Ulrich Wiegel, Managing Director of Rotkäppchen-Mumm Sektkellereien GmbH. The support offered by the BEUMER employees is exemplary. "The experiences gained in Eltville on the Rhine could be incorporated several weeks later during another installation and commissioning of the packaging system at the location in Freyburg, Saxony. The system was ready for use after only 2 days".