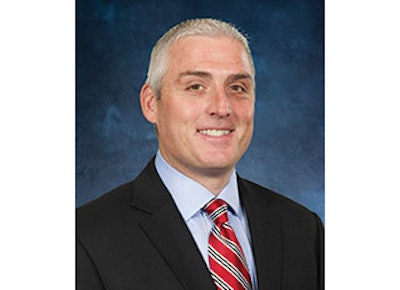
This article originally appeared in the January/February 2014 print issue of Food Manufacturing.
The Food Manufacturing Brainstorm features industry experts sharing their perspectives on issues critical to the overall food industry marketplace. In this issue, we ask: From dust explosions to gas leaks, food companies must mitigate various safety risks every day. What solutions can food manufacturers put in place to prevent potential disasters and increase employee safety?
Multi-layered communications has become a critical component of disaster preparedness for today’s food processing facilities.
Not long ago, emergency communications for manufacturing facilities, including food processing, were limited to outdoor sirens, indoor visual and audible alarms and public address systems. Times have definitely changed. Technological developments now enable plant safety officials to substantially expand the effectiveness of their alerting and mass notification capabilities. These added ‘layers’ of communications extend the reach of emergency warning and notification well beyond the scope of traditional plant alerting systems.
The modes of communication available to today’s emergency managers encompass everything from landline, cell and satellite phones to texting, message boards, PC-based instant messaging, email, other SMS technology and social media such as Twitter and Facebook. Since each layer of communications offers distinct advantages along with potential limitations, a centralized emergency notification strategy that offers redundant backup, and that reaches everyone who needs to be reached in the event of a crisis, is now essential.
This layered approach makes it possible to address cultural and environmental barriers to effective plant emergency communications. Among the most common cultural barriers are the language differences among employees. There are also the needs of the physically impaired, including people with mobility or hearing challenges. Environmental barriers include the unique and possibly hazardous characteristics of materials being used in production, and excessive noise levels in the plant.
It is worth noting that technology is also allowing plant safety officials to automate an expanding range of emergency response processes. This includes everything from controlling outdoor alerting devices, such as sirens, indoor alarms and emergency lights, to monitoring remote fire and gas-leak detectors. By the same token, sophisticated scenario management software is now being employed to automate the full range of disaster response functions, including expediting communications with local first responders and community safety officials. The ultimate goal is to eliminate the potential for a single point of failure that could adversely impact the effectiveness of the entire system in the event of an explosion, fire, toxic gas leak, natural disaster or other emergency crisis.