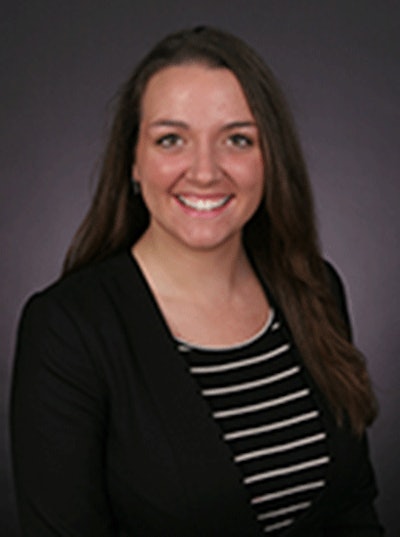
As the cost of labor and real estate squeeze manfucaturers' budgets, many are turning to plant automation to increase the usable space in their facility while saving workers' time. For many, this means more widespread adoption of automated storage soultions and traceability technologies. Companies are looking for high-speed conveyance and sortation soultions, light out mini-load systems, and more in an industry that necessitates an ever increasing pace of business.
This level of automation has been around for many years in Europe, but recently has made a big jump in American facilities. Where historically manufacturers could expand their labor force or facility, they now must look at long term investments into material handling automation and technology.
“Instead of expanding a building outward, automation allows you to expand upward and make the most of your entire facility, and not just the 10-15 feet closest to the floor,” says John Clark, New Business Development Manager at Viastore Systems, Inc.
And behind these conveyor and sorting systems is ever-advancing software and controls. “Company A’s conveyor is mechanically pretty much the same as Company B’s conveyor. The difference is in the software and controls that make the solution the most efficient and effective as possible,” says Clark. These advancements have helped with energy efficiency, power usage, and increased functionality of systems—meaning faster ROI and lower total cost of ownership for users.
Not only is automation helpful for increasing the efficiency of a plant, but it can also help prevent costly mistakes, leading to product waste and recalls. In traditional distribution, many workers touch a product to get it from shipment, to replenishment, to order. All of these product “touches” are places where damage and mistakes can occur. Automation removes this from the equation and creates an “electronic chain of custody” for the product—allowing for more accurate tracking that cannot only help prevent waste and mistakes, but can help deal with recalls when they occur.
Barcodes & RFID
In such a fast-paced industry, it can be difficult to maintain accuracy. “In some segments, manufacturers are increasingly employing end-to-end lot traceability from receiving through shipping,” says Mark Wheeler, Director of Warehouse Solutions for Motorola Solutions. “The material handling requirement is to make materials handling visible to the enterprise systems, and error-proofed on the warehouse and manufacturing floor whenever they are moved or processed.”
One strategy for this level of visibility and traceability is radio-frequency identification, or RFID. Simply put, RFID is the wireless, non-contact use of radio frequency to transfer data for the purpose of automatically identifying and tracking tags attached to objects. There is variation in tag design – some are powered by and read at short ranges via magnetic fields, others use a local power source like a battery – but they all contain electronically stored information.
Unlike a barcode, these tags do not need to be within line of sight of the reader and can even be embedded in the tracked object. The information they contain may be read, recorded, or rewritten. 1D barcodes can meet most of the data needs for product marking while 2D barcodes can do so in a smaller physical label that can hold extended amounts of data if needed. RFID is more often deployed in tracking assets in the plant or in a closed loop supply chain application.
Standard product markings that can be efficiently read at any step in the supply chain ensure case-level traceability, accuracy, and visibility. “Global Trade Item Number (GTIN) standards make it easy for any supplier to encode product information with extended data attributes at a case or pallet level as needed, without having to maintain elaborate routing guides for each customer-supplier relationship,” says Wheeler.
He also predicts that RFID will be more widely deployed to passively track assets and materials and there will be increased cold chain compliance monitoring through connected sensors. The biggest advancement that Wheeler anticipates, however, is the greater adoption of wearable computing and voice-activated technologies.
Wearables
“Motorola Solutions expects increased use of multi-modal speech in worker direction and interactions and incorporating voice direction with data capture for traceability and accuracy,” says Wheeler. Wearable computing and scanning systems enable pickers to handle product productivity while delivering near 100 percent accuracy, visibility, and traceability at the unit level.
The use of wearables can also help improve the ergonomics of material handling tasks that have not been mechanized. Leveraging the right wearable, voice, and hands-free technology can ensure a productive and accurate process that is more safe and efficient. Many of these devices also allow workers to keep their eyes on the machine and off of their phone or laptop, an obvious improvement over previous technologies and modus operandi.
Wearable technology can also facilitate more informed decision-making, as workers can have all of the necessary information and KPIs at their fingertips, literally. It’s a technology designed to merge relevant, real-time data and information seamlessly into our lives, on the job and off.
Automated Picking Solutions
Removing the number of “touches” is key to improving material handling systems. Quite frankly, machines make fewer mistakes than humans. A great way to do this is to automate picking systems. Clark is confident that there will be a continued focus on goods-to-person picking, as bringing the work to the worker is much more effective than having the worker looking for the work.
“Automation technology enables this as it brings the right product to the right place at the right time in the right sequence to create the right order for the customer,” says Clark. “This is the logical continuation of the ‘perfect order’ trend that started a decade or so ago.”
Packaging Implications
But as picking solutions are updated, packaging must also keep up. One company that’s been working to facilitate this packaging revolution is ORBIS Corporation.
“We are seeing significant advancements in automated systems, from high-speed conveyance to lights out mini-load systems,” says Andrea Nottestad, Marketing Manager – Retail Supply Chain, ORBIS Corp. “As a result, companies have a need for consistent packaging that provides repeatable performance within their system.”
In the food industry, that means using plastic pallets that are detectable through existing x-ray equipment, and that can meet sanitation standards to avoid costly and dangerous contamination.
“The idea that clean packaging can be reused within the supply chain is getting a lot more attention. Smooth surfaces, contoured corners, and flow-through designs of plastic packaging help in these efforts,” explains Nottestad. By design, reusable packaging is dimensionally consistent so it offers highly repeatable performance in automated systems and minimizes downtime associated with inconsistent packaging.
Nottestad says that while some companies may be hesitant about introducing reusable packaging into their system, companies like ORBIS provide test runs to help visualize how such packaging will impact their supply chain. She recommends companies look at cost-per-trip/use improvements and reduced payback time. “Many times, the cost-per-trip, over the life of the pallet or tote, is lower than single-use packaging and companies see a very rapid payback.”
There is also an important sustainability aspect to reusable packaging. Today, many companies are measuring their overall sustainability performance and are looking for ways to reduce waste from their supply chain. ORBIS uses life cycle data to help companies evaluate different packaging alternatives and calculate the environmental impacts – calculating greenhouse gas emission reduction, energy conservation, and solid waste reduction.
Where Should You Start?
While some automation solutions can be big ticket items, if your company hasn’t invested in automation yet, there are solutions that can help you walk before you run. “Working with a good partner will allow you to start slowly, identify the areas of low hanging fruit where you can introduce automation to make improvements and see the ROI, but also have a plan in place for additional automation to help your facility in the long term,” says Clark.
Start by looking not at the technology, but at what your material handling “pain points” are, advises Clark. What are the things keeping you up at night? Is it throughput, or space utilization? “Describe the symptoms and then look at what solutions fit best. If you assume you need a conveyor solution, what you end up with might not be the best for your pain points,” he says.
Wheeler also recommends anticipating customer demands for traceability and compliance labeling. Look back to suppliers to assess how they can improve compliance labeling and assist your internal processes for improving accuracy, speed, productivity, and visibility.
“Also, review the ergonomics of material handling tasks that have not been mechanized to ensure that the technology is aligned with the physical demands of the worker,” says Wheeler.
Remember that automation solutions are becoming more affordable, with an ROI that makes a more effective business case than ever before. What you thought you couldn’t afford might have an ROI that could surprise you.
Read Next