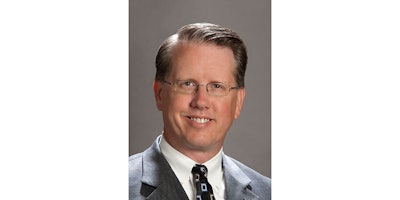
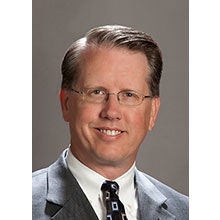
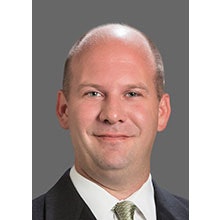
An ongoing challenge in the food industry is maintaining adequate inventory while avoiding stock outs and out of code products. Throughout the supply chain, from the manufacturers to the grocer, profits shrink when excess inventory is carried or physical inventories are inefficiently managed.
Three competing objectives govern almost all organizations:
1. Sales — preserve sufficient on-hand inventory to satisfy every possible (or impossible) customer request
2. Production — achieve the lowest cost-per-unit through long production runs which are often independent of sales forecasts
3. Inventory Management — maintain the appropriate level of on-hand inventory to satisfy customer demand while minimizing cost
However, the most profitable objective common to all stakeholders should be to create an efficient supply chain which meets customer expectations while maximizing sales and minimizing inventory costs.
Warehousing and rent, labor costs (moving, counting and maintaining, etc.) and diminished product quality represent the “hidden” costs of high inventory levels. Those costs also put added pressure on cash flow. A successful inventory management program requires close collaboration among sales, purchasing, suppliers, customers, production, warehouse and shipping, combined with a well-conceived and implemented sustainable methodology like cycle counting.
Achieving inventory accuracy is critical to the bottom line. Inventory is often the largest consumer of capital for an enterprise. It is imperative that a business have accurate inventory records to be effective and efficient. Poor inventory accuracy may result in stock-outs of inventory and require a business to carry higher inventory levels than necessary, which requires more capital.
Common causes for inventory inaccuracy are:
1. Imprecise material requirement planning
2. Inaccurate bill of materials (BOMs)
3. Lack of shop floor discipline (BOM’s not followed, non-recorded transfers, etc.)
4. Ineffective root cause analysis of inventory issues
5. Accounting system not configured correctly
Inventory accuracy is a measure of how closely official inventory records match the actual on-hand inventory levels. Accounting prefers dollar-based measurements while operations and material management personnel have a stronger interest in the unit accuracy on an individual product or SKU. For both, maintaining an accurate count is imperative.
Although they provide a high degree of accuracy, annual physical inventories can be expensive, require a large investment of physical resources and have a significant impact on operations. The accuracy achieved by a physical inventory count often is not sustainable and, in almost every case, fails to provide a root cause analysis of inventory inaccuracies — a major advantage realized through cycle counting.
Cycle counting has proven to be an effective method to ensure inventory accuracy resulting in the confidence of the manufacturer to produce to customer demand and the broker and grocer to carry less inventory. Cycle counting provides a significant advantage over an annual physical inventory count because it achieves and sustains very high accuracies, spreads out the counting workload and continuously measures accuracy. An effective cycle count program does not interrupt operations but does facilitate process improvement and ultimately eliminates the need for an annual inventory.
Above all, cycle counting continually finds and corrects inventory record errors. Counters inspect a small sample of inventory items at a defined frequency (e.g., daily or weekly), thereby spreading out the workload of a traditional full physical inventory. Cycle count selection may be random or semi-random, based on the established methodology.
Cycle counting can be tailored for your operation and employ underutilized personnel. Multiple variables affect the number of daily or weekly counts required, including number of SKU’s, desired accuracy level, timeline needed for accuracy and the current state of your inventory and warehouse organization. When designing a program, variables include the number of counts and personnel available, count timing, availability of forklifts, scales and other resources, and the counting method (counts sheets, RFID, paper or digital record keeping, etc.).
Inventory planners often use a combination of methods to determine the initial number of counts that will be required. According to the Association for Operations Management (APICS), 50-60 percent of companies use a combination of methods to complete their cycle counts. An ABC classification is often the primary methodology to ensure adequate coverage. Inventory items classified as "A" are the most expensive or most critical items. "B" items are less expensive and less critical. "C" items are small, inexpensive items. Inventory that is expensed such as screws and packaging are often not included in the cycle count program.
An example ABC chart is shown directly below. However, an ABC chart should be tailored to the needs of your organization.
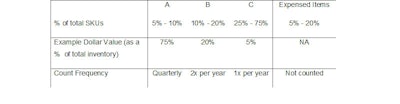
There can be some pitfalls with a cycle counting program without instituting a formal cycle count program or methodology and ensuring ownership/responsibility for inventory accuracy is in the correct hands. Sometimes, there may be insufficient resources to conduct the cycle counting on the determined day or during the time period. Also, available personnel may lack training, or equipment such as storage racks and bins, forklifts, scales, computers and scanners may not be available for inventory, or paperwork and labeling may be in poor condition. Also, multiple size and weight unit of measure terms and lack of consistency often come up versus how they typically are handled in a physical inventory.
Cycle counting requires good communications and coordination with the external financial auditor. Cycle counting has an effect on the financial statement audit process and your auditor will require full process documentation and verification of key controls over the cycle count process. Close upfront communication is necessary, including a discussion and review of the cycle count plan, count frequency and personnel involved. Your accounting and financial personnel should be involved up front and clear policies need to be developed for variance.
The effect of cycle counting on a financial statement audit varies by audit firm. Cycle counting can be viewed as reliable as an annual physical inventory and could eliminate the need for an annual physical inventory. However, it will not eliminate auditor test counts, nor will it eliminate the auditor’s need to visit multiple locations. It also creates new flexibility in the timing of auditor counts. The auditor will require a cycle count summary with number of counts and dollar and quantity variances, with verification of variances posted to the general ledger.
The financial statement auditor has a fiduciary responsibility to observe and verify the cycle count methodology and results. Timing for observation can be anytime during the year and multiple observations are common. Depending on the risk, the auditor may focus more counts towards the reporting date. All company locations are subject to observation. The auditor may observe the on-going cycle count, follow up on variances, or perform additional test counts.
Your accounting and IT personnel, along with your ERP (Enterprise Resource Planning) software, are important partners in setting up a cycle counting program. Involve them in discussions between Sales, Production and Purchasing as you develop the right methodology for your organization. Your CFO and other financial personnel will be strong advocates for improving inventory management and can help lead change in your organization through the internal audit function.
In addition to an ongoing accurate inventory methodology through cycle counting, other process improvements within the supply chain can have a positive impact on the bottom line.
- Purchase and manufacture based on customer demand, not on volume discounts or unit cost.
- Map the purchasing and production processes identifying non-value added activities, bottlenecks, constraints, etc.
- Formalize or strengthen your preventive maintenance program.
- Maintain discipline in maintaining bill of materials.
- For Sales, Marketing and Customer Service, map the sales forecasting and sales order processes, again, identifying non-value added activities.
- Commit to SKU rationalization using historical data with up-front sales team involvement.
- Across the board, compensation plans should be built around selling profitable SKU’s.
- Work with suppliers to reduce lead times, improve quality inspections and insist on shipping accuracy.
- Work closely with customers to encourage cooperative forecasting and tie on-line real-time orders to shipment tracking.
Inventory accuracy is not a pipe dream or cost prohibitive. Cycle counting is an effective way to make your supply chain efficient and world class.
About the authors
Rick Feldt, CPA, CGMA, is a partner in RubinBrown’s Business Advisory Services Group and also serves as vice-chair of the firm’s Manufacturing & Distribution Services Group, Food & Beverage Segment. Contact: [email protected] or 314-290-3220
Nathan Croll, CPA is a manager in RubinBrown’s Business Advisory Services Group. Contact: [email protected] or 314-290-3484