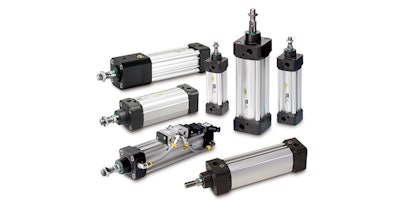
For food and beverage producers, pneumatic cylinders are practically as ubiquitous as sugar or salt because they’re used in wide range of production equipment, including product marking/identification, sensing, bottling, packaging and sealing lines and many others. Each year, new, more sophisticated designs come to market, which makes maximizing the return on investment (ROI) possible from a particular food production application pretty challenging.
This article offers some tips food and beverage industry machine designers builders should bear in mind to shorten the payback period.
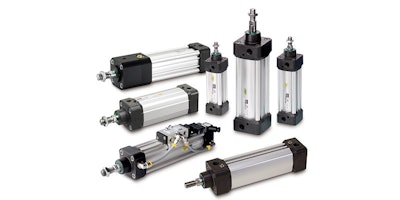
Tip #1: Avoid side-load mounting. Cylinders are designed to deliver push-pull stroke action, so side-load mounting can lead to several performance problems, including misalignment, off-center loads, rod deflections, imprecise tie-rod torque or long stroke action. During installation, the cylinder piston rod should be aligned with the mating machine component and then inspected in both the extended and retracted positions. Improper alignment can lead to excessive rod gland and cylinder bore wear, resulting in a shortened lifespan for the cylinder and lower productivity. Both of these unwanted effects can extend the payback period.
Tip #2: Prevent contamination. The life of a cylinder depends on preventing contamination; particulates, pipe rust, scale and thread sealant debris can all shorten the life of the seal and plug openings, and damage surface finishes. Therefore, until the system is fitted with piping, keep the port plugs supplied with the cylinder in place and always clean the piping thoroughly before making connections.
Tip #3: Keep moisture out. Stopping moisture intrusion is critical to preventing contamination. When moisture collects in components in all compressed air systems, it blocks the outlet flow-through. This can be potentially damaging to the performance of the cylinder because it can lead to diluted pre-lubrication grease, contaminated air-line lubricants, a damaged barrel or rod finish, and the potential to freeze in cold weather.
To prevent moisture and contamination problems, consider using stainless steel cylinders, which feature a smooth, hygienic exterior design. These are particularly useful for food industry applications because cleanliness is ensured via the use of stainless steel piston rods, cylinder tube and end covers. Also, the end covers have no recesses or other grooves that can collect unwanted contaminants or bacteria, while the scraper rings, piston rod bearings and seals are made from self-lubricating materials to allow for regular washing and degreasing of the piston rod. Food and beverage market customers will take more than the usual interest and care in the design of the product, the quality of the external surface treatment of the cylinders and the type and quality of the grease used inside the cylinders in order to ensure their compatibility with the process in which they are used.
Tip #4: Mind the wiper seals and cushioning. Maximizing piston cylinder ROI also requires paying close attention to both the wiper seals specified and the cushioning required. The end application will dictate the selection of wiper seals. For example, applications subject to extremely dusty conditions or very high operating temperatures will require seals designed to match the installed environment. The wrong seal choice can cause degradation, allowing particles and dirt to work their way into the cylinder, which ultimately risks cylinder failure, shortening cylinder lifetime and reducing ROI.
The right cushioning choices are directly linked to cylinder lifetimes. Cushioning is required to decelerate a cylinder’s piston before it strikes the end plate. Reducing the piston velocity lowers the stress on cylinder components, increasing the usable lifespan and ROI. Although cylinders that feature automatic adjustment are available on the market, using manual variants to achieve optimal cushioning is generally recommended because it allows matching the weight of the work piece to the dynamics of the movement. This method has been found to be much more accurate and efficient.
Tip #5: Watch out for extraneous oil. Preventing contamination means watching out for any oils that could result from air compressor lubrication carryover or synthetic oils, both of which are typically incompatible with air-line components. Such oils can swell the seal and plug openings. Consider using oil-compatible seals.
Tip #6: Prepare to be shocked. Cylinders operating at high or fast cycle rates will typically generate significant shock loads at end of stroke. Furthermore, the heat generated by the system can exceed the component’s temperature limits and affect the lubrication. To counter these effects, consider selecting a pre-lubricated or air-cushioned cylinder. Adding a shock absorber or lowering system pressure via a regulator on the return (non-working) side of the cycle are other options. Adding flow control to the cylinder can also help, as long as high speed is not required.
As many engineers will be aware, running cylinders over their capacity applies high levels of stress and unwanted friction to seals, resulting in broken rod ends and disintegrated actuators. In addition, if the system contains speed control or energy-absorbing devices, then pressure spikes can double or triple normal system pressures. That’s why it’s important to make sure rod accessories are shouldered firmly by threading all the way down or by using spacers or shims. Alternatively, consider increasing the rod thread size or using a studded rod end.
These tips can help facility engineers and machine designers maximize return on pneumatic cylinder investments. Best of all, most only require minimal time and effort to investigate, with any subsequent investments within reach of most budgets.