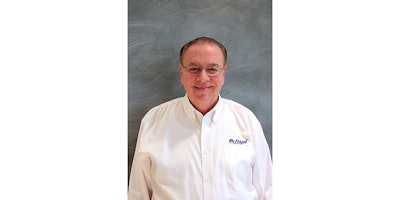
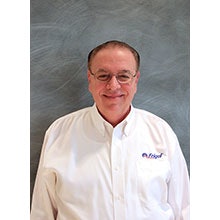
Former U.S. Congressman and motivational speaker Ed Foreman once said, “If you always do what you've always done, you'll always get what you've always got.”
It’s a quote worth paying attention to when it comes to the traditional method of delivering cooling water to any number of processes used in beverage packaging and processing. That’s because many in the industry who continue to do what they have always done are likely to experience inefficiencies and waste. Those who consider a different approach stand to benefit. Here’s why, along with seven reasons to rethink traditional methods used for process cooling.
Traditional method: one size fits all
The traditional method used to satisfy cooling loads for processes such as pasteurization, carbonation, hot filing and distillation, involves the use of a central chiller system that provides process-cooling water or ammonia refrigerant at the lowest temperature required for any given process within the plant.
It’s a one-size-fits-all approach. That means all process water or refrigerant is cooled to the single lowest temperature required and routed to other processes, regardless of whether the same temperature is needed elsewhere. Additionally, centralized chillers in many plants use ammonia as the refrigerant.
Decades ago, the industry determined that centralized chillers delivered the best cooling efficiencies based on the efficiencies of ammonia as a refrigerant. The traditional approach established decades ago also involves the use of open cooling towers to provide cooling water to centralized chillers.
Intelligent process cooling: new and better
A number of companies have begun to realize that doing things the way they’ve always been done when it comes to process cooling isn’t always best. Instead, they’re looking to an approach called “intelligent process cooling.”
The approach involves a closed-loop system with a closed-loop adiabatic fluid cooler that uses heat exchangers and an internationally patented adiabatic chamber to cool water and circulate it to and from smaller chillers positioned near each process cooling point within a plant. It eliminates the need for an open cooling tower and a centralized chiller. The advantages are clear. Seven of them include:
- Increased efficiencies: The approach delivers cooling water to each individual process at only the temperature required for that process rather than one set point and one flow rate for the entire operation. That means the system won’t have to do more work than necessary to provide cooling water at the right temperature and pressure where needed.
- Improved safety: An intelligent process cooling system doesn’t use ammonia as a refrigerant, eliminating significant safety risks and expenses associated with it.
- Water savings: The central cooler with its adiabatic chamber is unlike an open cooling tower in that it does not use an evaporative process to cool water. Instead, the adiabatic chamber pre-cools ambient air on hotter days before it enters the central cooler’s heat exchanger compartment. Cooled water is then re-circulated to the water cooled chillers or any process points that do not require cold temperatures. As such, water savings of as much as 95 percent can be achieved when it’s used instead of a cooling tower.
- Avoidance of the risk of proliferation of harmful bacteria, such as Legionella, due to the patented, enclosed design of the adiabatic misting chamber and the absence of stagnant water.
- Lower maintenance and chemical costs: Compared to cooling towers, a closed-loop system is far easier and less costly to maintain. The need for chemicals to treat process-cooling water is also drastically reduced when a closed-loop system is compared with a cooling tower.
- Reduced energy consumption: An adiabatic fluid cooler allows for “free cooling” because it uses ambient air to cool process water. That means there is no need for chillers to meet cooling loads when ambient conditions permit. Instead, the system automatically shuts down the chillers for any given process to capitalize on free cooling, in turn saving energy.
- Improved bottom line: Water savings, energy savings, reduced maintenance, less chemical use — in addition to the lower costs associated with reduced safety risks — translate to operational savings that contribute directly to the bottom line.
A path toward success
Intelligent process cooling is a concept that has been widely adopted in various industries. The reason is because progressive and forward-thinking companies decided it was time to move beyond the traditional approach to get ahead.
Leading companies involved in beverage processing and packaging are now starting down the same path because they’re no longer thinking about the way things have always been done. They’re thinking about the benefits they get with an advanced approach to process cooling.