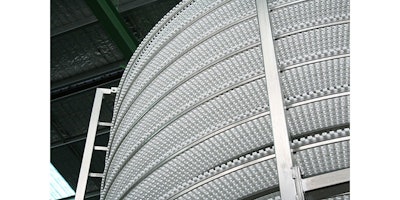
Virtually every sector of the food processing industry requires a controlled rate of cooling at one time or another. For anyone debating whether or not to commission one of these systems, materials handling specialist Industrial Conveying (Aust) Pty Ltd has identified six key benefits to consider.
1. Optimizes floor space
Spiral Chillers allow an efficient use of vertical space without sacrificing horizontal travel length or speeds while maintaining product orientation and pitching. Modular in design, the system is quickly and easily installed regardless of the shape and size of the premises.
2. Customizable temperature settings
Spiral Chillers convey products that require a precise rate of temperature drop. By conveying product in spiral configurations within a temperature-controlled environment, this solution provides a logical cooling and setting function in the food manufacturing and processing industry or any general engineering application. Spiral chillers can operate in temperatures as low as -40ºC. They also work efficiently across the entire humidity spectrum — from a completely saturated environment to that of low humidity. The spiral conveyor’s ability to operate across a wide temperature band ensures that it performs well, carrying product in chilling and/or freezing processes — anything from a controlled, gradual temperature drop through to a sudden blast freeze.
3. Customisable travel speeds
Facilitating continuous product flow, spiral conveyors allow precise set-up of travel speeds so that each unit of product arrives at the appropriate manufacturing process at exactly the right temperature and physical condition. This travel speed is set in relation to temperature-controlled drying and cooling times, so effectively product does not have to be stored on shelving or massive bench tops while waiting for the curing process to complete. At all times a first-in first-out configuration is possible. This allows goods to run at speeds and durations specific to each product.
4. Wide range of applications
- Baking
- Glazing
- Cooling
- Setting
- Defrosting
- Dairy
- Dehumidifying
- Chilling
- Freezing
- Product transfer
- Elevating/lowering
5. Hygienic
Spiral chilling conveyors have the capability to move food between several floors without human intervention. By reducing manual handling the chance of cross contamination is significantly reduced. When required, stainless units can be given hygienic wash downs.
6. Prevents bottlenecking
Often the solution implemented is vat-style cooling or freezing, which although effective can create a bottleneck in an otherwise fluent system and even create double handling. Spiral Chillers completely eliminate this problem.
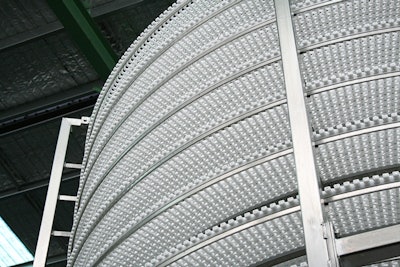