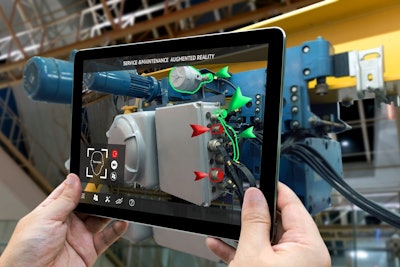
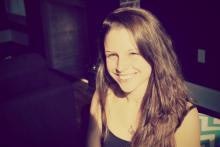
It’s easy to see the immense potential in wearable devices for the average consumer. Between fitness and health tracking, mobile notifications at a glance, and even contactless payments, a ton of cool features already exist. But the technology also shows a lot of promise in the business and enterprise world. Healthcare is a notable example, where wearables can be used to collect information about hospital patients. Or what about precise authentication for locked offices — employees could tap their wearable against a lock mechanism to gain access.
These tools also have a place in manufacturing, especially with the rise of IoT and connected machinery. Here are seven potential applications within this sector.
1. Safety Awareness and Injury Prevention
Manufacturing professionals could approach this concept in many ways. For starters, you can use simple wearables like wristbands, connected clothing or headwear to present safety and environmental information to the wearers. Imagine something like Google Glass that tells people which surfaces are too hot to touch, when machinery is malfunctioning or even when conditional hazards are present — like spilled fluids.
Another aspect relates to prolonged work injuries. Just being present and working long hours in the conditions of a large warehouse or manufacturing plant can be damaging to the human body over time.
For instance, standing for excessive periods can be bad for the back and limbs. It increases exhaustion that can also boost the potential for injury. Knowing this, BMW has deployed a unique “Chairless Chair” employees can wear to enhance their comfort on the floor. It’s essentially a harness-type wearable you can convert into a chair at the push of a button. This allows employees to sit down while working, even when no seating options are available.
2. Hands-Free Training on the Job Site
Unfortunately, training tends to be very hands-off by nature, especially in manufacturing. There's a good reason for this, too, as inexperience can lead to severe equipment damage, injuries or poor performance all around.
Employers can use wearable technology to make this age-old process more modern and efficient. General Motors, for example, leveraged Google Glass — augmented reality glasses — to provide a unique, improved training process for their employees.
With the help of Plex Systems, they deployed an experience that allows new workers to learn their trade, in active settings, on the production line. The headwear essentially helps them assess current conditions and performance while also providing solutions to any questions or problems they may have. Furthermore, the platform allows for truly hands-free working conditions. When a machine malfunctions or breaks down, workers can snap photos and share them with the appropriate parties, allowing them to keep their hands away from the hardware while doing so.
3. Improved Process Efficiency and Productivity
Workers can also use wearable technology to augment or improve existing processes and functions within industrial and commercial settings. On the production line, for instance, staff members could use the tech to stay focused on what they’re doing, obtain additional info or deliver remote orders or commands. In warehouse and order fulfillment settings, wearable technologies can speed up operations, too. Dutch fulfillment company Active Ants experimented with Google Glass, using the technology to help employees pick and prepare custom-designed products. The result was an immediate 15 percent improvement in speed with errors dropping 12 percent.
In a warehouse, the situational and contextual data allows order fulfillment employees to find goods or ordered products faster — the devices pinpoint exactly where an item or order is located and helps facilitate the next steps. It’s not a stretch to imagine this functionality adapting to fit any number of industrial scenarios.
4. Situational Awareness
This is especially true of construction and development, but it applies to manufacturing and warehouses, as well. The environment or setting is dynamic in that it's always changing to make room for more work, updated projects or even machinery and hardware. This is a bit different than general safety because it’s challenging to remain aware of hardware, shelving or even equipment that's always on the move throughout a space or area. Through the combination of IoT, connected sensors and body-worn wearable tech, workers can be more mindful and aware of what's going on around them.
For example, imagine someone is walking along a narrow pathway blocked in on both sides by tall, packed shelving. They cannot see what lies on the other side, nor can they know what's waiting for them when they leave that area. Smart wearables — like connected helmets or eyewear — can tap into a local network and pinpoint exactly where objects and equipment are. This would allow workers to avoid a situation like walking out in front of a top-loader or forklift that’s on the move.
This kind of setup could even notify employees when something within a plant has changed. For instance, if a hazardous spill is present somewhere, the managers can let everyone know to avoid that section of the property.
5. Augmented Reality and Predictive Modeling
Google Glass, Microsoft HoloLens and similar technologies merge the gap between digital and physical realities through something called augmented reality. These devices overlay digital content and information in the real world. That alone has immense potential in manufacturing and industry, specifically regarding predictive modeling.
Epson’s Moverio BT-350 Smart Glasses are a fitting example of this technology. Thanks to an embedded camera, the glasses will overlay digital information related to whatever the wearer is looking at. While building or assembling something, for example, workers can see the next and even future steps in the process as if they already completed them.
In manufacturing, staff members could use this for preventative maintenance to measure or inspect equipment, assembly and project design or planning.
6. Remote Management Opportunities
The beauty of IoT and connected sensors — especially in a manufacturing plant — is that they allows managers to see how everything is operating at a glance, remotely. Most everything is synced back to a central hub or system that enables administrators to review status info, makes changes or plan future actions.
But when an entire workforce has wearable technology, the same can happen for personnel. Managers and decision makers can see where everyone is, what they’re doing, how productive they are or even potential bottlenecks or problems. Employee X is walking this way, while Employee Y is walking the other way, and they may collide — keep in mind, this is an incredibly basic example. The real allure is the option to deliver commands and requests no matter where managers are or what they're doing. A project admin could be off-site entirely, yet remain in-touch and communicative with workers.
7. Authentication and Security Planning
In specific manufacturing and industrial settings, it's essential to maintain proper security protocols and authenticate workers or third-parties before they access particular areas of a property. For example, management might not want to risk allowing an equipment vendor access to an area of the plant with unannounced products or goods.
Wearable technology can block, allow and track specific movements of workers. Want to provide temporary access to a section? It’s possible to authorize their mobile device, headset or wristband to let them in. Once they’re done that assignment, you can then revoke their access or lock down the area once again. Did you identify someone who might not be following proper protocols and putting others at risk? Revoke their access to the equipment they’re using to prevent further injury or harm. Then, take action by referring them for additional training or scheduling a one-on-one meeting.
Technology Opens Doors for Modern Industry
The bottom line is that wearable technology — and modern tech, in general — is presenting so many new possibilities and opportunities for improving the way things operate. Both human workers and the equipment and tools they use can be modified to boost productivity, safety and efficiency.
From things like wearable headwear or glasses to wristband-like activity trackers, so many options exist for augmenting the current working conditions for the modern workforce. This helps management and project administrators stay informed, as well as provide proper maintenance and planning strategies for the work they’re doing. It contributes to the idea of a "well-oiled" machine, which is precisely what one would want in industrial settings.