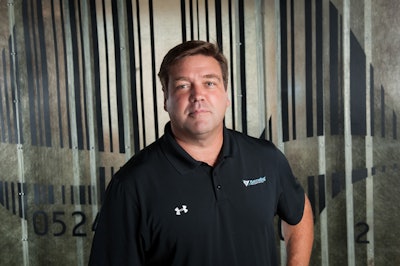
In an age where manufacturers are looking for new ways to cut costs and drive new efficiencies, automatic identification and data capture (AIDC) technology has become commonplace in day-to-day operations. Whether it involves barcode scanning, radio frequency identification (RFID), wireless networks, or a combination of solutions, AIDC technology has proven effective in a wide range of applications – from creating a chain of custody throughout the supply chain, to validating processes, to tracking assets.
But, now that manufacturers have these technologies in place and up and running, what are the next steps? They may have experienced significant results, like cutting costs, reducing manual process, or increasing throughput, but are unsure how to glean additional value from their investment. At the same time, manufacturers are honing in on better labor management, or the workforce that is utilizing the AIDC technology. In just-in-time (JIT) environments, there are no extra personnel, inventory, or resources sitting around, so manufacturers must make sure to have the tools to perform to the volume required by the end user. Also, trends such as changing skill sets and difficulties recruiting and retaining a stable workforce further complicate the situation.
There are a prolific amount of data sets and data sources available that can help overcome the aforementioned challenges. The problem is that “big data” is coming in from so many varied sources, and manufacturers simply do not know what to do with it or how to use it. The answer lies in supply chain analytics. With the right analytical tools, manufacturers can obtain actionable, meaningful, and supported insight from available data in order to make better business decisions. When it comes to AIDC, supply chain analytics are most useful in two chief areas: device optimization (the technology itself) and labor management (those who are using the technology).
AIDC Device Optimization
With supply chain analytics, manufacturers can receive timely and relevant feedback about their AIDC platform to determine how the technology is performing – feedback beyond what is provided by a typical Mobile Device Management solution. Through this insight, users can better understand the underlying causes of inefficiencies, identify areas for continuous improvement, perform predictive analysis, and more. For example, through dashboard and reporting tools, manufacturers can easily see device utilization data to determine user adoption rates. They can monitor battery performance of their devices in the field to prevent downtime. Or, they can even make sure that the right tools are available at the right time. As a result, manufacturers can optimize their mobile deployments to attain additional ROI.
Labor Management
The second component to this equation involves labor management. Using supply chain analytics, it is possible to match the right tools with the right people, and the right people with the work. Analytics platforms accomplish this by gauging and managing the labor resources that use the technology in terms of measurement of activity benchmarking, engineered labor standards, and dashboard reporting. These tools take into consideration production data (volume), integrated with labor, cost, customers, and time data.
With this information, manufacturers can answer the following questions: Do we have enough or too much staff? Is that staff working the appropriate kinds of hours? Are results consistent across all days of the week? Are employees working full time, part time, or working overtime to complete this volume of work? And, do we have the right kind of staff? Beyond staffing levels and mix, labor analytics can also identify occurrences and cost of early/late punches and impact on overtime and overall labor costs; determine cost impact and effectiveness of pay policies (differentials, for instance); and perform extensive analyses to promote awareness and understanding of how labor is currently utilized in an organization. As a result of the insight gained through supply chain analytics, manufacturers can increase worker productivity, reduce operational costs and remove business process inefficiencies to operate lean and meet the needs of JIT environments.
Achieving Analytics Success
Supply chain analytics tools can provide practical and fully actionable (fact-based decision making) information to help optimize the supply chain from an AIDC and human capital standpoint. Along with the right AIDC tools and support organization behind those tools, supply chain analytics can assist in driving more revenue, reducing your cost structure and improving the experience of your customers and your workforce. Yet, this is only a piece of the supply chain analytics puzzle. Looking forward, manufacturers will continue to extend the capabilities of analytics tools to gain insight into the overall performance of the manufacturing facility. With the influx of the Internet of Things (IoT), more data points are available than ever before, which allows manufacturers to gauge the efficiency of a particular production line or overall equipment effectiveness (OEE).
Remember: it is not enough to just put AIDC in place. You have to proactively manage the technology using analytics tools. And, even then, it’s not enough to proactively manage the tool set. You have to also proactively manage the labor force that is using those tools. With the combination of insight into AIDC tools and the workforce, manufacturers can readily improve technology, process, and people in the supply chain in order to operate more efficiently and accurately.