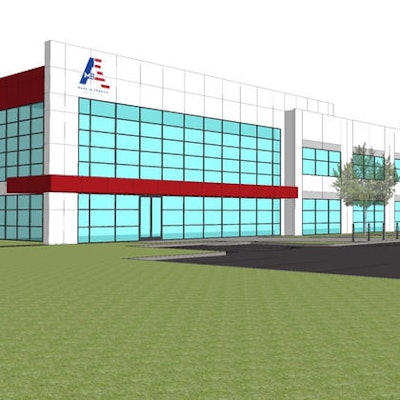
I spoke with Made In America Seating CEO Darius Mir about the company's new, state-of-the-art operations in Union City, Tennessee. Mir provided insight into the ups and downs of domestic manufacturing and discussed his formula for maintaining competitiveness with imported products while operating on U.S. soil.
Bridget Bergin (BB): I’d love to hear about your new operations in Union City. What made you choose that location?
Darius Mir (DM): We operate three factories, including our main office and distribution center out of Hawthorne, California. About 12 years ago, we started our own factory in China to manufacture some of the components we use in our chair manufacturing. We have been running that operation quite successfully, but we decided that Chinese manufacturing is not going to be the future for us.
Three years ago, we started looking at bringing manufacturing back to the U.S. We determined that if we put a few elements together, we would be able to manufacture what we need in the U.S., maintain a high-quality standard and compete with imported products. To accomplish this, we needed a good location. If if we can ship the product to most of our major markets within a day’s worth of tracking, it would be a tremendous benefit to our customers. Also, it would enable us to compete better because we wouldn’t have to absorb the cost of ocean transportation, the lead time associated with this and the inventory levels required.
We came across an opportunity in Union City, Tennessee. It offered us the advantages we needed: within a day, we could reach geographic areas from Texas to Illinois to Atlanta. Union City experienced some major plant closures, including Goodyear’s shut down in 2011. When we brought our project to Union City, we were met with open arms and offered a lot of incentives and a tremendous amount of cooperation.
Also, Union City is close to some major universities that specialize in engineering. This was very important to us, because the factory is a state-of-the-art manufacturing environment using high-tech equipment that requires high-talent engineers.
BB: Why were you interested in pursuing domestic operations?
DM: When we first started our factory in China, the advantages available were very different from what exists there today: There are inefficiencies in the work and instabilities in the environment. Mostly, we didn’t feel comfortable investing heavily in technologically advanced equipment outside of the U.S., and we realized that using such equipment could help us become more efficient.
As a manufacturer, it is our obligation to see what we can do to bring manufacturing back to the U.S. If we rely on technology, we have a chance to compete with imported products.
With the limited operations we have started, we have established that our theory is correct. For example, an operation that would take 22 people at our facility in China can be accomplished at a higher quality level with four people in Union City.
BB: What types of plant technologies does Made in America use, and what made you decide to implement those technologies?
DM: We rely very heavily on technology in terms of ERP programs. Our facility in California has been using a sophisticated ERP program, and we purchased more of that for our Union City facility. The program we are using covers all aspects of our business from manufacturing to the financial matters.
National and international retailers are importing very large numbers of office chairs at the moment. When we approached some of these retailers with our program, they were receptive to the idea of switching over to buying from us as opposed to importing. However, they told us that they would not be able to buy our product at a premium because price points are very important to their customers.
We did our calculations and determined that we would be able to compete. However, it was very important to us to have excellent visibility into our operations when we started processing some of these orders. When manufacturing a product that will be sold at a very tight margin, manufacturing costs must match the estimations.
BB: Is there anything else you’d like to add?
DM: If there is a possibility for small manufacturers like us to start researching domestic manufacturing, I’m sure they will come to our same conclusion. By putting certain elements together, U.S. manufacturing makes a lot of sense. I’m hoping that exposure for our project will be a platform that can help other manufacturers take a look at manufacturing in America.
*NOTE: A previous edition of this article said that Made In America Seating manufactured small components at a factory in China. The affiliate company 9to5 Seating has a factory in China and will continue to manufacture in China, but Made in America factories are located in the U.S.