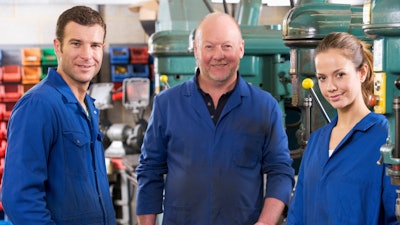
The last two years have been a tumultuous time in the talent market.
Before the pandemic, low nationwide unemployment made hiring and retaining good people a challenge for manufacturers. Then, as the pandemic drove unemployment to an unprecedented 14.8 percent - the highest monthly rate on record - the market was flooded with candidates at a time when health concerns made it unsafe for anyone to come to work even if they wanted to.
Now, even as workplaces reopen, extended unemployment benefits and continued coronavirus fears are keeping many people out of the job market. That means manufacturers are still struggling to hire, while also dealing with higher turnover and absenteeism related to COVID-19 quarantines and family challenges.
While most indicators show that we are turning the economic corner, staffing will continue to remain a challenge as competition for talent heats up and the number of open positions creates a job-seekers market. To overcome staffing shortages, manufacturers must embrace digital technologies in order to increase productivity and capacity. Here are 3 strategies that can help.
1. Process automation. Digital automation solutions can help you do more with fewer resources by streamlining workflows and eliminating redundancies and mundane tasks. And it can help reduce the risk of burnout, stress and low morale that can cause employee churn by lightening the load on the staff you do have in place.
For example, implementing Industrial Internet of Things (IIoT) technologies to monitor equipment and processes can reduce the need for human oversight. Or, automating workflows like maintenance requests or task tracking can help keep things moving forward while eliminating manual or redundant processes that are time-consuming and tedious. Both of these can increase HR efficiency by freeing up personnel to focus on mission-critical tasks.
While automation might require a bit of an investment, the potential ROI can make it worthwhile by both lowering full-time labor requirements and increasing productivity per hour by roughly 25 percent.
2. Adopt a digital KPI strategy. You can’t fix what you can’t see. Gaining real-time visibility into what’s happening with key performance indicators (KPIs) can give you a window into a whole world of opportunities to optimize workflows and enhance productivity. Implementing a digital KPI management strategy can illuminate key metrics from absenteeism to material flow and cycle times and help you understand both operational and individual capacity.
By establishing a baseline, setting a benchmark or goal, and then monitoring performance as you make adjustments, a digital KPI strategy will help you analyze what’s working and what’s not. It can also help to pinpoint root causes for process inefficiencies, which may be earlier or later in the process than you originally thought. By creating this “digital thread” of information, you now have hard evidence to identify where issues lie and the ability to simulate solutions before fully committing to changes that may not work.
3.Digitize onboarding and training. When talent is scarce, it’s imperative to accelerate the process of getting the staff you do have up to speed and on the job as quickly as possible. Begin by assessing the talent and skills you already have to optimize current resources. Conduct a talent inventory and create a database of who can do what tasks or fill specific roles. Then, you can compare this against your current training programs to identify gaps, add new programs or cross-train existing staff.
Next, implement digital training solutions that allow staff to access learning anytime, anywhere to make it as easy as possible for them to gain applicable new skills. With digital learning management solutions, employees can learn at their own pace and even on their own time. You can even incorporate video analytics recordings of work in progress to demonstrate proper procedures.
This can be especially valuable for employees who are off work on mandatory quarantine with asymptomatic COVID-19 or a direct exposure with no illness. By giving staff access to remote training options, they can use the downtime for upskilling or cross-training. This not only allows you to shift staff around to cover deficits once they’re cleared to return to work, but also gives employees a chance to bolster their own careers, which can fuel your leadership pipeline.
Although, onboarding and training is only the first step, digitizing HR is the beginning of cultural change. After all, HR is the first touch inside an organization. Incorporating technology and analytics into talent acquisition to forecast labor needs and skill gaps reduces the panic button companies are hitting far too often and far too late.
While staffing shortages might be particularly painful right now, the reality is that being prepared for the natural ebb and flow of the economy and the workforce is always a smart strategy. Implementing digital technologies can help manufacturers optimize their operations and amplify efficiency to overcome staff shortages now and down the road.
Shannon Gabriel is the Managing Director of Leadership Solutions at Dploy/TBM Consulting Group.