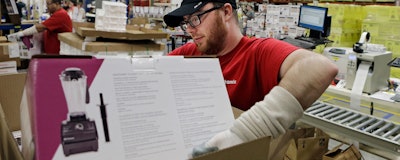
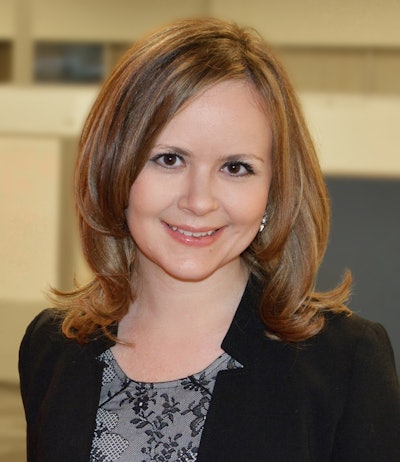
Today, the U.S. manufacturing industry faces many challenges, yet perhaps the most significant is the current — and growing — skills gap with six out of ten production positions going unfilled due to a talent shortage. Closing the gap is a priority, but it’s challenging given the magnitude of the problem — according to research from Deloitte, nearly 3.5 million manufacturing jobs will need to be filled in the next decade, and two million of those jobs are likely to go unfilled.
What is causing this gap? The primary factor is the significant increase in baby boomer retirements, as an estimated 2.7 million jobs will open as boomers continue to exit the workplace. Economic expansion will also play a role as 700,000 jobs will be created due to natural business growth.
Perception and Education Compound the Challenge
As the manufacturing industry loses its experienced knowledgebase to retirement, one would expect the next generation to be prepared to step in — but unfortunately, for many companies, that isn’t the case. Manufacturing can present a great opportunity for younger generations — millennials and Gen Z especially — as open positions are more technical, specialized, and demanding. However, finding qualified talent is increasingly difficult and the lack of it currently in place is creating situations where the talent isn’t there to step in for retirees. Many candidates don’t have the required STEM skills (science, technology, engineering, and math), which may be attributed to the decline in the amount of technical education programs offered at high schools today.
Perhaps the biggest obstacle in overcoming the skills gap, however, is the fact that many people have misconceptions or preconceived notions about what it’s like to work in manufacturing today. They picture an archaic industrial plant, complete with old-fashioned equipment or lines of manual laborers, and assume a manufacturing career isn’t right for them. If so, they’re not alone. According to a recent survey commissioned by Kronos Incorporated and conducted online by Harris Poll, more than 50 million Americans have limited to no knowledge about the modern manufacturing industry, and only 37 percent of respondents said they would encourage their children to pursue a career in manufacturing. As a result of these factors, manufacturers are at a severe disadvantage when it comes to attracting and retaining skilled employees for today’s advanced manufacturing environments.
What Can Be done?
To address these challenges — and tighten the growing skills gap — there are several practices manufacturers can implement to best position themselves for success.
Leverage Current Talent and Apprenticeships
Manufacturers can harness the potential within their existing workforce by implementing apprenticeship programs for their top-performing employees to learn new skills that will serve the needs of the business in the future. These programs combine classroom instruction and work-based learning with experienced workers serving as mentors who help transfer the necessary skills and knowledge to those with the drive and competency to take on new challenges.
This approach helps with succession planning and retention — manufacturers get the benefit of having an available talent pool to replace retiring workers, and high-potential employees can progress in their careers. If you are considering deploying an apprenticeship program, reference the Employer’s Playbook for Building an Apprenticeship Program, which was co-developed by The Manufacturing Institute, along with Alcoa, Dow and Siemens.
Apprenticeships are also a great way for manufacturers to partner with vocational/technical schools and community colleges to give students the opportunity to acquire highly-sought skills and streamline the transition to the workplace upon graduation.
Deploy Creative Education and Recruiting Strategies
Companies must play an active role in enlightening the next generation about the career potential in manufacturing by getting involved in community outreach and education programs for children, particularly those in middle and high schools. For instance, Manufacturing Day, an annual event occurring on the first Friday of October, was created to encourage manufacturers to host tours and programs for their communities. Participation in MFG Day is an easy start — valuable resources exist to help companies plan and promote their own events to generate excitement about the industry and STEM related careers.
In the near term, to fill the thousands of available positions today, companies should consider alternative sources for talent. One under-utilized and highly-skilled talent pool is the multitude of military service men and women who re-enter the civilian workforce each month. There are numerous resources available to help match qualified Veterans with open positions.
Focus on Retention by Increasing Employee Engagement
Hiring qualified employees is just the first step; manufacturers must concentrate on retention as the company in the next town will by vying for the same talent. One way to reduce turnover is to focus on employee engagement — in fact, engaged employees are 87 percent less likely to leave than those who are disengaged.
To drive employee engagement, manufacturers must foster a positive work experience and culture — one where competitive compensation and attractive benefits are a piece of the puzzle, as true engagement occurs when employees feel valued and supported by management, and when employees have the opportunity to learn, grow and maintain a work-life balance. Now more than ever, manufacturers need to institute flexible scheduling practices and provide access to technology and the information employees need to perform at their best. This can go a long way to increasing employee engagement, and ultimately, retention.
It’s a Team Effort
There is no single or simple solution to solving the manufacturing skills gap — it will take time and a multitude of strategies by the industry, government, educational institutions and community. Manufacturers can start to make traction by considering alternative sources for talent, educating the next generation on the opportunities in modern manufacturing, and creating work environments that foster a culture of engagement and excellence.
Kylene Zenk is Director of the Manufacturing Practice Group at Kronos Incorporated.