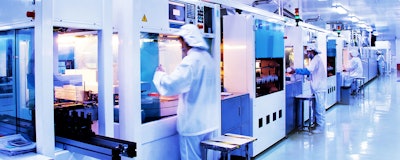
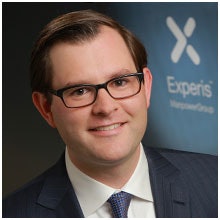
This election cycle there has been a lot of talk about how to protect manufacturing jobs and boost production in the United States. But we often forget that just having the jobs isn’t enough, we also need a workforce with the skills to do them. Looking ahead to the future of U.S. manufacturing, it’s worth asking — are we ready?
As labor costs go up in key markets like China and U.S. production gets more efficient and competitive, manufacturing jobs are slowly moving back. But these new roles are fundamentally different than those that went overseas in the 80s and 90s. Technology has transformed the shop floor, automating and streamlining work with more data and sophistication at every level. Workers today need to be higher-skilled — able to read, write, analyze and manage the software that controls the diverse array of machines involved in modern production.
In certain parts of the manufacturing industry, technology is changing so rapidly that training programs struggle to keep pace and the whole system gets out of sync. This leads to talent shortages, higher costs and lower growth. By some estimates, we could have up to two million unfilled manufacturing jobs in the U.S. in the next decade due to the skills mismatch. Even today, more than half of employers report their workforce lacks the necessary digital skills.
In an effort to get ahead of this, late last year the Chicago-based Digital Manufacturing Design & Innovation Institute (DMDII) — a Department of Defense-backed initiative that’s part of a wider network of manufacturing nodes around the country called Manufacturing USA — convened leading manufacturers, educators, policymakers and workforce experts from ManpowerGroup around an ambitious project: to identify the key roles that will power the digital manufacturing revolution and create a framework to describe and standardize them.
Specifically, we set out to analyze 20 roles that will be on the leading edge of digital manufacturing and create a “taxonomy” showing what skills they require; much like the Labor Department has for more mainstream roles. The purpose of the work is essentially to write the blueprint for a nationally recognized (locally deployed) workforce development plan, that ensures both students and current manufacturing workers are learning the skills that will actually lead to jobs. It will also give employers a better idea of who to hire going forward.
In the course of ManpowerGroup’s work with DMDII we are already seeing just how fast roles are changing, and how little understanding there is of the skills needed to really drive the growth of this industry. For example, I was recently talking with a client at a leading industrial automation company about their challenge finding embedded software engineers. As he put it, “we’re now competing for talent with every company putting a sensor on a device or machine.”
His comment highlights an important point: understanding and developing these skillsets is not just about manufacturing; the whole economy is shifting towards a digital future. And we’re just scratching the surface. Activities like data management, security and supply chain risk management will all look different in a world dominated by augmented reality and artificial intelligence technology. Given how digitization ripples through the economy, we can expect to see a lot more skills shortages in other sectors too if we don’t get a better at keeping up.
So what does it take for a person to be successful in an environment where skills needs are changing fast and harder to predict? As someone in the workforce solutions business, I’d argue the most valuable skill a person can have today is something we call learnability: the desire and ability to learn new skills to stay employable. This isn’t to say technical skills aren’t important; they are. But in a time of disruption and great uncertainty, employers need to focus on building sustainable talent pipelines, and that means hiring people with the curiosity and hunger to learn and continue developing themselves.
Creating a culture of learnability in organizations also makes it easier to do more on-the-job training, rather than holding out for a perfect skills match — thereby expediting the hiring process. With skills evolving as rapidly as they are today, this sort of practical, experience-based learning is a vital part of the training process. In this way, learnability is the ticket to success for both individuals and employers alike.
Meeting changing skills needs in the manufacturing sector is also going to take better coordination between employers, educators and policymakers. That is hopefully where our project with DMDII will help move the needle both by facilitating dialogue at the forefront of the industry, and by creating a common framework to describe the roles emerging. Putting a standardized system in place will also make it easier for more organizations to get involved in training and the industry generally — it will get us all aligned and lead to faster results.
These cutting-edge jobs are here now. Ultimately, the opportunities are wide, and the transition to a more digitized manufacturing sector will increase productivity, efficiency and innovation, breathing new life into the industry for years to come. The future is there for the taking — the readiness is all that is needed.
Chris Layden is Managing Director of Experis.