
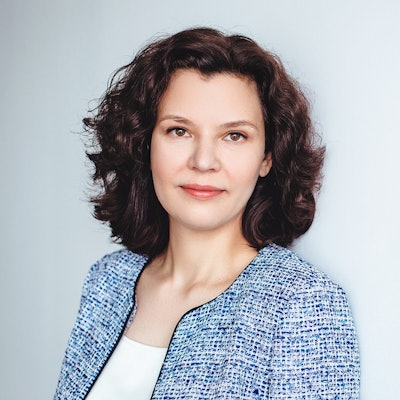
A rebirth of artificial intelligence (AI) is upon us and some manufacturers are struggling to get their heads around it.
AI is a well-known concept that many have been investigating since the early 80s. The first products featuring artificial neural networks were announced over a decade ago, and there have been multiple research papers written on the general principles of AI.
However, a new wave of AI has visibly emerged over the last couple of years — a negligible time frame for most traditional industrial operations. Many of the much-publicized applications — including AI winning in the game of Go, voice recognition or self-driving cars — seem to be quite far away from manufacturing business and their operational processes. Because of this, many industry players have been left wondering what this new technology really means for them.
Leaving aside the hype around digitalization and ubiquitous connectivity, there is an alternative way to look at AI in 2017 and it is all about dealing with uncertainty.
There have been two significant changes in the AI world since the 80s. Firstly, we have started to accumulate meaningful amounts of data. Secondly, we have developed the computing power that can perform the complex analysis of this data, enabling machines to make decisions without being explicitly programmed. The major implication being that manufacturers can now use AI to improve repetitive, routine decisions in much better ways than before.
The industrial world is a very complex one. There are fluctuations, uncertainties and unknown dependencies in almost every possible industrial process. There is, of course, extensive knowledge about the physics and chemistry of the processes that can be used at industrial scale. In fact, many universities and dedicated research teams have spent years using this knowledge to develop models that can be integrated into the systems that manage production processes. Unfortunately, such models are never exactly accurate. They are simply based on the best available assumptions of what might happens within those processes and are therefore always limited when dealing with this uncertainty.
Fortunately, over the course of many years, we have collected data that describes these processes as they run in the real world — on any given piece of equipment, for a specific production facility. And this is where AI becomes useful to the industrial companies. In contrast to the previous theoretical approaches that require a deep understanding of the process itself, AI instead uses this real-world data to learn what exactly happened in each process. Through analysing production logs, sensor data and so on, it can derive the weaker dependencies that are either not described in the formulas, overlooked by statistics or only partially recognized by some human experts. AI can enrich the existing assumptions — and formulas — about manufacturing processes through using real-world data and making better operational decisions in a fully automated way.
In practice, this means that we can eliminate the inefficiencies that are borne out of these uncertainties. When it is not understood with precision what happens inside of a complex technological process, possible variations must be provided and extra room given to account for any variabilities not considered. This often results in the excessive use of raw materials, overspending on energy or generated waste, simply because the tools are not available to make the perfect decision in each and every case.
Adding AI on top of existing processes, a new layer of intelligence that deals with these inefficiencies is presented. It does so by operating closer to the lower boundaries and personalising each operational decision, instead of following some set of general rules. For example, AI can choose optimal production routes for each individual product batch to improve speed and throughput, streamline logistics for the whole fleet to cut down on fuel consumption, or suggest best operating parameters for some complex unit, responding to every minor change in conditions, and so on.
And that is exactly the way we suggest manufacturers should look at AI technologies. It is not some disruptive power that will completely take over the world, it is a universal optimizer that can learn from past experiences and make operational decisions better than humans.
With a higher precision of forecasts and smart recommendations, not only is the efficiency of operations improved but also sustainability. Saving on operational costs because of optimized energy and fuel use, or reduced defects and scrap will help manufacturers to become greener at the same time. Is there a reason not to start embedding AI into your operations right now?
Jane Zavalishina is CEO of Yandex Data Factory.