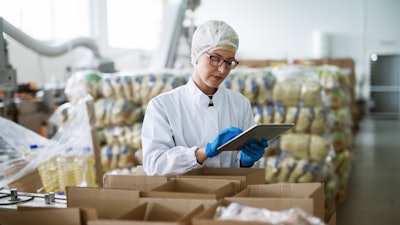
From pandemic disruptions to semiconductor shortages, manufacturing has faced unprecedented challenges in recent years. Amongst other strategies, the emergence of reshoring and friend-shoring has added another layer of complexity to an already dynamic landscape. The port strikes this fall served as just another reminder of the rollercoaster that supply chains have been on over the last few years. With so much volatility, leaders in manufacturing businesses are understandably struggling to navigate the shifts being driven by technology and geopolitical dynamics. We are beginning to see the impact of industry 4.0, and for leaders who are trying to determine how to make the most of technologies ranging from smart factories and digital twins to the industrial metaverse and AI, it can be overwhelming to decide on where to focus.
There is consensus that these technologies will be transformative – 83% of manufacturers believe that smart factory solutions will transform the way products are made five years from now. What is less clear is how, where and which technologies to deploy. As with most emerging technology, the answers are not immediately obvious, and a test-and-learn approach will be necessary. Manufacturers can still prepare themselves and their teams for ongoing uncertainty and a period of rapid change by adopting the following three strategies.
Balance Productivity and Agility
While not necessarily at odds, there are situations where productivity comes at the expense of flexibility. During the pandemic, these dual objectives came to the forefront since higher stock levels provide flexibility but come at a cost. The greater the uncertainty, the more important it is to build in flexibility. Gaming out scenarios can help manufacturers make better risk weighted decisions on where it’s worth sacrificing short term productivity for flexibility. Greater availability of data, increasingly sophisticated modeling and better predictive analytics can help determine the probability and potential impact of a severe weather event or a disruption to shipping lanes. Such tools can be game changing in optimizing the productivity-agility tradeoff.
Train and Engage the Entire Workforce
In our work with manufacturing organizations, we have often seen the best ideas and solutions come from frontline workers. When asked why these ideas were not surfaced before, the answer is often some version of, “Nobody ever asked.” Understanding how to best utilize emerging technologies cannot be done well without input from the individuals who will be most impacted by them.
When creating task forces or study groups to determine where and how to digitalize, leaders should include front line workers in addition to engineers. Decisions on where and how fast to deploy new technologies should be based on how long it will realistically take teams to adopt new skills. This needs to be accompanied by an investment in employees so they feel supported during any changes, which will not only help in making better decisions, but will also ensure buy-in during the technology implementation stage.
Many factories have not seen the immediate benefits they expected from introducing automation, because without the right skills to operate and maintain the new production lines, the expected uptime and efficiency numbers were not achieved. This dynamic will be even more amplified with AI powered technologies given that the current skills gap is even greater. Getting the most value out of technology requires a different workforce – the percentage of manufacturing jobs requiring a bachelor’s degree has been rising for some time and will continue to do so. Employers who are struggling to find and retain employees can make strides by investing in upskilling and training employees to work in new ways with new technologies.
Prepare for Quick Pivots
As companies experiment with new technologies, many will work, but some will not. Especially since the use cases for technologies like AI and IoT are still being developed. Technology deployment is unlikely to follow a straight path, and when you layer on changes driven by other forces like geopolitics or supply disruptions, even the most deliberately formed plans will require adjustments and pivots. The definition of “long” in long-term planning is shrinking and the need to re-evaluate and adjust is increasing. Readying the organization for fast pivots requires first, expecting change and second, being able to identify and make the necessary changes. Planning for different scenarios, leaning on experiments and pilots before full deployments, encouraging employees to highlight gaps or opportunities, and dispersing decision-making but centralizing learnings are all ways to help the organization learn, change and pivot.
There is no way for us to know for sure what the future will hold in terms of supply chain, technology and manufacturing. What is clear is that it will require greater agility from leaders and different skills from employees. Our new reality is that technology in factories is evolving and the demographics of the workforce are changing. Companies that can respond to these external changes proactively through reshaping, upskilling and reorienting their workforce towards enhanced flexibility, experimentation and speed will be primed to capitalize on the opportunities presented by change.
Gaurav Gupta is Managing Director and Head of R&D at Kotter. For more information, visit kotterinc.com.