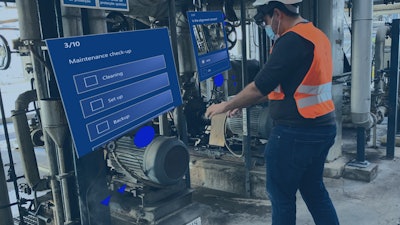
The COVID-19 pandemic sent shockwaves across the world that will continue to be felt for years (if not decades) to come. From posing global economic challenges and disrupting distribution chains, this health crisis was responsible for the most significant transformation in labor in decades: remote work and collaboration.
“Remote work spiked during the pandemic, from about 6% of full workdays in the U.S. to more than 50% in the spring of 2020.“ - Harvard Business Review
While remote working was introduced differently across different sectors and levels, there was widespread adoption of this new reality in the manufacturing sector and overall, in the industry. Due to its characteristics, manufacturing and field work-related activities rely on on-site personnel, however, businesses have been able to introduce tools to help reduce the number of trips to locations, boost remote management, remotely monitor operations and adapt to new demands.
While initially these changes were introduced to ensure that businesses managed to stay open and to reduce the disturbance of regular operations, they soon revealed key benefits to the productivity and economic sustainability of businesses.
Industry 4.0 Boom
“Overall, 94% of respondents told us that Industry 4.0 had helped them to keep their operations running during the crisis and 56% said these technologies had been critical to their crisis responses.” - McKinsey
The COVID-19 pandemic marked a turning point for Industry 4.0 technologies and served as a watershed moment for the greater digital transformation movement. As a result, by introducing new collaboration and monitoring tools, businesses turned to new innovative and emerging technologies to ensure their operations continued to operate smoothly.
Such technologies acted on different levels of production chain and industrial operations:
- Augmented and Connected Worker Technology: By digitizing different processes and centralizing information, businesses were able to enable real-time collaboration between teams and workers. Frontline workers can use mobile devices (such as smartphones, tablets, headsets and wearables) to perform tasks while all information is stored on a private cloud and can be accessed by different stakeholders.
- Visual Remote Assistance: By introducing visual remote assistance tools, organizations have reduced the number of on-site visits carried out by experts. This helped reduce travel costs and breakdown times and ensure that critical operations such as maintenance, set-ups and commissioning, could be performed by more workers. Virtual assistance sessions leverage Augmented Reality to help experts signal the precise location of specific steps.
- Training and upskilling: Industry 4.0 remote collaboration technology, including connected worker solutions, not only helps create knowledge bases for daily operations but can also be used to train new workers and equip existing ones with the necessary skills to perform a broader range of tasks. Augmented Reality and Digital Twins can be particularly useful as they can simulate real situations in controlled and safe digital environments.
- IoT Data and Remote Monitoring: New Augmented and Connected Worker digital solutions can not only integrate with a broad variety of software but also converge different sorts of information to provide managers, directors or field workers with accurate real-time information. Equipment and machines can be monitored remotely and key data accessed to ensure operations are always monitored.
Glartek
After the Pandemic
Following the decrease in infection cases and global vaccination programs, the industry and most professional activities resumed their normal activities. However, the pandemic kickstarted a series of changes that are here to stay. Analysts and industry insiders are now predicting that remote working and collaboration have become a normalized and growing trend.
That is particularly noticeable when comparing the number of workers fully working on-site in 2018 and 2023: the number decreased from 91.6% to 75.5%, according to Harvard Business Review. In fact, in many cases, flexible work has become a major factor for employees when deciding to apply for new jobs and accept job offers.
Inside the Industry
In the industry, such transformations have paved the way for a new reality and have had a profound impact on businesses. As a result, many of these solutions have stopped being considered temporary or aimed at helping deal with constraints related to the pandemic. They have instead become valuable additions that have revolutionized the daily lives of workers and introduced new operational strategies.
Remote collaboration technology has been leveraged for all sorts of activities and continues to play a crucial role in use cases such as remote assistance (to repair machines, perform setups or problem reporting), audits and quality assurance (remote monitoring of audits) and for training (both for new workers and for upskilling).
Such transformations have resulted in tangible benefits and operational results that go to show the importance of adhering to the digital transformation movement, including:
- Cost reduction related to trips – experts and specialists are no longer required to travel to different locations (which sometimes can be located on different continents) to assist frontline workers or help install new equipment.
- More efficient training – training can be more flexible, there is a reduced need for on-site shadowing, workers’ progress can be remotely tracked and experts can be consulted remotely.
- Breakdown times reduced - equipment malfunctions can be promptly resolved using remote assistance solutions that efficiently connect frontline operators and specialists and ensure that operations are halted for less time.
- Higher commitment to sustainability - reducing traveling needs helps businesses reduce emissions and meet sustainability goals. Additionally, remote monitoring and the digitalization of operations can end paper use altogether or reduce it substantially.
- Less on-the-job shadowing - more experienced workers are no longer required to fit time into their busy schedules for on-site training.
- More efficient decision-making - remote collaboration provides decision-makers with more information (automated data including reports, real-time metrics and other centralized information) to help them make decisions.
---
Glartek
Carlos Bonifácio is a copywriter for Glartek, a tech company that develops AR, AI, Digital Twin and IoT-based digital solutions for organizations operating in the industrial sector.