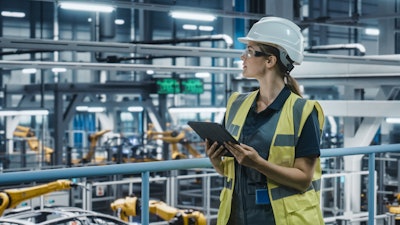
Manufacturing businesses are looking to adopt eco-friendly practices because of multiple reasons. The compliance standards are higher than ever, compelling manufacturers to abide by the environment-safety practices. Moreover, Kearney's study reveals that 80% of consumers consider the environmental consequences of making buying decisions.
Therefore, manufacturing companies are riding on the sustainability bandwagon and considering their moral duty, the existing legal obligations and customer appeasement practices.
Here, Industry 4.0 technologies are a great enabler in adopting sustainable practices. It helps minimize waste, reduce energy usage, optimize work procedures and ultimately enhance the quality of life for both present and future generations.
Industry 4.0 is a catalyst for manufacturing companies embracing sustainability through green manufacturing. It involves producing goods using economically viable methods that minimize detrimental environmental effects while preserving energy and natural resources.
Additionally, sustainable manufacturing prioritizes the safety of employees, communities and products.
Let's dig in more on sustainable manufacturing.
What is sustainable manufacturing?
Sustainable manufacturing refers to designing, producing and delivering goods in an environmentally, socially and economically responsible manner. It involves integrating sustainability principles into all manufacturing stages, from extracting raw materials to product disposal.
The goal is to minimize the negative impacts on the environment, people and economy. Moreover, sustainable manufacturing aims to meet present needs without compromising the ability of future generations to meet their own needs.
Industry 4.0 technologies that drive sustainable manufacturing
The Industry 4.0 revolution has significantly shifted manufacturing practices, promoting sustainability and efficiency by integrating advanced technologies. It leverages the integration of advanced digital technologies such as the internet of things (IoT), artificial intelligence (AI), machine learning (ML), big data, robotics and automation into the manufacturing sector.
By leveraging Industry 4.0 for sustainable manufacturing, businesses reduce waste, optimize their processes and improve their overall environmental impact.
Let us explore more.
1. Artificial Intelligence (AI) for process optimization
AI-powered solutions can analyze large volumes of data and identify manufacturing patterns to optimize production processes. Manufacturers can leverage innovations in machine learning algorithms to drive operational efficiency, plummet energy consumption and minimize waste generation.
One such innovative solution is integrating CPQ software for manufacturing that allows businesses to quickly and accurately configure complex products, determine pricing and generate quotes. It leverages AI algorithms and machine learning techniques that empower manufacturers to make informed decisions, offering personalized product options while maintaining optimal production schedules. This reduces errors, minimizes material waste and optimizes production processes, ultimately increasing efficiency and reducing costs throughout the manufacturing cycle.
There are AI solutions for production scheduling, process optimization, supply chain optimization and more. It can optimize production scheduling, analyze production data to reduce downtime and predict equipment failures by analyzing data collected from sensors installed in the equipment. All these factors contribute to timely maintenance, leading to sustainable manufacturing.
- Energy management: AI can optimize energy consumption by monitoring and controlling energy usage patterns in manufacturing plants. It helps identify energy inefficiencies and recommends actions to improve overall energy efficiency, reducing the carbon footprint of the production process.
- Supply chain optimization: Manufacturers can use AI to analyze and optimize the entire supply chain, from raw material sourcing to end-product delivery. Moreover, AI can reduce emissions and lowers transportation costs by reducing fuel wastage since it can optimize routes. Effective warehouse management and scheduling of production based on available resources.
- Material optimization: AI algorithms process large amounts of data on material properties, performance and costs. These algorithms leverage machine learning techniques to identify patterns and relationships between material attributes and desired product outcomes. This leads to improved efficiency, reduced costs and enhanced sustainability.
2. Smart Manufacturing
Businesses can use IoT devices, AI and ML to create smart factories where machines and systems are interconnected, exchanging data in real-time. This enables companies to optimize production processes, reduce resource consumption and minimize waste.
Here are several ways smart manufacturing can help implement sustainable practices:
- Energy Efficiency: Smart manufacturing systems help optimize energy consumption by monitoring and controlling energy use in real-time. The AI-enabled automated systems adjust energy usage based on demand, schedule production during off-peak hours and identify energy-saving opportunities. These measures reduce greenhouse gas emissions and lower operational costs to ensure sustainable manufacturing.
- Waste Reduction: Smart manufacturing also uses advanced analytics to identify inefficiencies and waste in production processes. Such insights offer process improvements like reducing overproduction, optimizing raw material usage and minimizing scrap materials. Such an approach reduces the waste generated by manufacturing processes and conserves valuable resources.
- Predictive Maintenance: IoT-enabled systems can monitor the condition of equipment and predict potential failures, enabling manufacturers to perform maintenance only when necessary. This helps reduce downtime, extend equipment life and minimize the need for part replacements. All such factors positively contribute to a more sustainable production process.
- Resource Optimization: By leveraging real-time data and analytics, smart manufacturing can optimize resource usage. This includes efficient scheduling of production runs, improved supply chain management and reduced transportation costs. Additionally, smart manufacturing can facilitate the use of recycled materials and promote circular economy principles, reducing the reliance on virgin resources.
3. Additive manufacturing (3D Printing) for waste reduction
Additive Manufacturing (AM), or 3D printing, is a key technology in Industry 4.0 that transforms how products are designed, manufactured and distributed.
Using traditional manufacturing methods may often lead to significant amounts of waste due to the subtractive nature of the processes.
Additive manufacturing offers a more sustainable alternative by building products layer-by-layer, using only the required material. This reduces waste and creates lightweight yet strong components, reducing energy consumption during transportation and product usage.
Here are some ways in which 3D printing supports waste reduction to drive sustainable manufacturing:
- On-demand manufacturing: Additive Manufacturing enables creating parts and products as needed, reducing the need for large inventories and storage space. This on-demand approach reduces waste associated with overproduction and product obsolescence, as well as the energy consumption and environmental impact of storage and transportation.
- Design for disassembly and recycling: Businesses leveraging AM can create products with fewer parts and less complex assemblies, making them easier to disassemble and recycle at the end of their lifecycle. This helps promote a circular economy (more on it in the next point), reducing waste and the need for raw materials.
- Rapid prototyping and iteration: Additive Manufacturing allows quicker and more cost-effective prototype development and iterative design improvements. This accelerates the innovation process and reduces waste generated during the design and development stages.
4. Circular economy through material recovery and recycling
The circular economy is a concept that focuses on reducing waste, maximizing resource efficiency and fostering a more sustainable and environmentally friendly approach to manufacturing. Waste and by-products are viewed as potential resources and products are designed to be reused, repaired, refurbished or recycled at the end of their life cycle.
Industry 4.0 technologies can also facilitate the implementation of a circular economy by enabling better material recovery and recycling. Integrating IoT devices, AI and automation into the production process help manufacturers track and sort materials more efficiently. And this leads to higher recycling rates and reduced wastage to ensure sustainable manufacturing.
Here's more to it.
- Resource efficiency: The circular economy promotes resource efficiency by recovering materials from end-of-life products and recycling them back into manufacturing. This way, manufacturers can reduce the demand for raw materials, conserve natural resources and lower the overall environmental impact of manufacturing.
- Economic benefits: Material recovery and recycling lead to cost savings for manufacturers since recycled materials are often less expensive than virgin materials. Additionally, the circular economy can create new job opportunities in recycling, remanufacturing and other related sectors.
- Energy savings: Manufacturing companies can recycle material by implementing closed-loop systems prioritizing waste reduction, material longevity and eco-efficiency. Systematically recovering materials and reintegrating them into production processes help minimize energy-intensive raw material extraction and reduce the carbon footprint of manufacturing operations.
Bottomline
Manufacturing industries are long criticized for negatively impacting the environment. But, technologies associated with Industry 4.0 are key to transforming production processes and adopting eco-friendly practices.
Manufacturers can streamline operations, minimize waste and lessen their ecological footprint by leveraging the above-mentioned methods. As more and more companies focus on sustainability, incorporating these cutting-edge technologies will be essential in fostering a greener manufacturing landscape.
---
Hazel Raoult is a freelance marketing writer and works with PRmention. She has 6-plus years of experience in writing about business automation, entrepreneurship, marketing and all things SaaS.