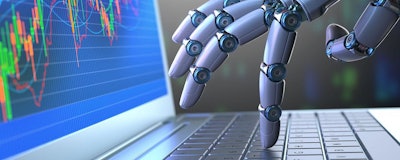
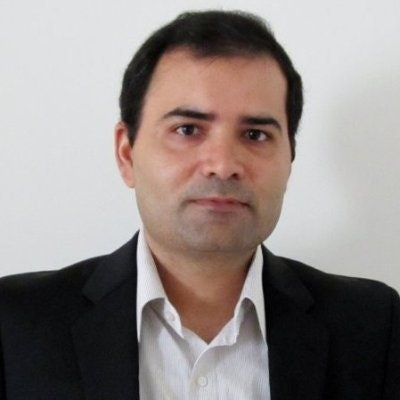
The manufacturing industry is one of the earliest adopters of automation, in fact they have been using machines and even robotics to assemble, test, and package their products for a long time. While robotics has helped manufacturers automate physical tasks for several decades, they are now looking to help automate their back-office functions through Robotic Process Automation (RPA). RPA can have a significant impact on your organization if you understand how it’s used - but, like any technology, it’s not a panacea: it must be implemented and managed correctly or you won’t realize its full benefits.
RPA tools automate highly repetitive, labor-intensive, and high-volume processes, in turn leaving employees to focus on priority, higher value tasks. Specifically, in the manufacturing industry it can help automate inventory management, waste and regulatory management. There are many existing business applications for RPA. Some forms of RPA use screen scraping tools to automate a sequence of human actions on applications. This is very useful for legacy or custom systems, because it enables the automation of tasks that can't be fully digitized using the current software, but it does not improve the underlying business process. It simply automates certain tasks, improving the speed of processing.
Automated workflows are a popular form of RPA used to automate simple tasks such as approving an invoice. However, the latest form of RPA, “bots,” can take this level of automation even further by completely automating, without any human intervention, any task by applying simple business rules and data validation.
Why Implement RPA?
RPA is quickly becoming essential for back-office functions because companies are not investing in these areas as much as before. Many manufacturing companies are reluctant to add to their back-office staff and often choose not to replace this staff if they leave. Yet, they need to find a way to process the same number of invoices with less resources.
This constant pressure to increase back-office performance without increasing investment is driving the need for RPA in many finance functions like accounts payable, accounts receivable, generation of bill materials, invoice processing and purchase order management. Bots can be used to automate simple processing tasks like coding invoices based on historic data or sending reminders for pending actions. Bots are well suited for these back-office functions as they are repeatable and predictable. More complex tasks can leverage RPA with machine learning or artificial intelligence capabilities to improve processing speed and accuracy. Employees are then free to focus to more complex tasks which require human intervention and deliver greater value to the organization.
Companies should carefully evaluate the procure to pay processes and identify areas where RPA can be used to completely automate tasks. When RPA is combined with intelligent workflows, the procure to pay process becomes faster and more efficient. It also ensures that the highly skilled procurement and Accounts Payable staff can focus on the tasks that are of the most value to the company.
According to a recent industry-wide survey conducted by Serrala to financial leaders across the globe, organizations are actively trying to identify areas where they can automate tasks. As 98 percent of the respondents said, “increasing automation” is a top priority for their organization, yet only 9 percent are fully automated. Within the manufacturing industry specifically, respondents believe the order-to-cash process has the greatest need for modernizing at 33 percent, followed by the procure to pay process at 17 percent. However, only 4 percent have actually fully deployed RPA within their organization.
What are the benefits?
In addition to freeing up high-value employees, RPA also improves productivity by ensuring work is done around the clock, 24/7.
RPA also has the potential to transform back-end operations by:
- Improving process efficiency and service effectiveness without a complete process redesign
- Optimizing KPIs, allowing management to gain greater transparency with a real-time view of data
- Remaining compliant with rapid data validation and a full audit trail
Understand both sides of implementation
When implementing classic rules-based RPAs, it is best to start by applying the technology to simple and straightforward tasks. RPA is very fast and efficient and if the wrong rules are in place, you risk gaining efficiency at the cost of effectiveness. RPA initiatives can fail if the technology causes errors. This is because people tend to place machines at higher levels of accountability compared to humans. The same is true of advanced Machine Learning-based systems, which are notoriously opaque. If a process requires complex or fuzzy logic, it is best to wait to introduce RPA until after the company gains confidence with the technology with other less complex processes. Companies need to be fully aware of both the pros and cons of RPA if they want to identify the processes that will truly benefit from this type of automation–in many cases, it is best to properly balance RPA with human oversight and processing.
Technology alone is not the answer
Always think about how to optimize processes before you consider applying RPA technology. Many manufacturing organizations think that RPA equals innovation - however, RPA is just a technology that facilitates better processing. When intelligently applied, RPA can deliver real value to the organization through greater speed, efficiency and employee satisfaction.
Vishal Awasthi is SVP of Technology at Serrala.