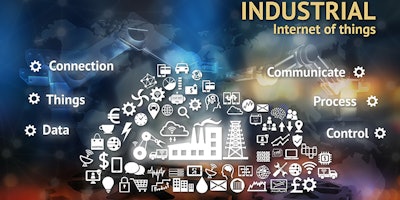
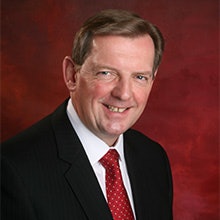
Across the food and beverage industry, there is a focus on avoiding or limiting recalls. However, according to the USDA, the amount of food recalled nationally increased by 37 million pounds between 2015 and 2016. This increase is most likely due to increased diligence on the part of food manufacturers. Viewed one way, food manufacturers are helping to raise the standard of food quality for both their brand and consumers. While increased vigilance for quality is good, recalls can still result in significant costs to the manufacturer and may still tarnish the brand, leading to poor market performance against competitors.
Food manufacturers are reducing risk with an assortment of new techniques. One example is DNA analysis — which senses when ingredients are unsafe and could affect food quality or product safety. While manufacturers have controls set up to monitor their own processes, they don’t have specific, beginning-to-end monitoring of their entire supply chain. This includes all raw materials from their suppliers through their entire production, all the way to the packaging process of the finished product. The final step is ensuring products are placed on the shelves through the distribution network. And it’s with this beginning-to-end monitoring that the Industrial Internet of Things (IIoT) can have a revolutionary effect.
Tracking Products with Smart Technology
Leveraging IIoT sensor technologies and real-time data analytics has allowed food manufacturers to adopt new techniques such as track-and-trace, which precisely monitors incoming ingredients. Taking farm-to-table to a new level, this technology can assist a manufacturer in exacting details about a crop, pinpointing the specific row in the field where a vegetable was grown. Similarly, IIoT technologies now make it possible for food manufacturers to monitor their finished product at every step on the path from the manufacturing facility to the consumer, in real-time. This added benefit of the IIoT provides peace of mind to the manufacturer since they know that their product is at the ideal temperature for the entire excursion, and gives manufacturers the opportunity to mitigate issues that could lead to a food safety issue or spoiled product.
Of course, this thorough, real-time visibility and traceability requires an unprecedented level of data sharing between food manufacturers, suppliers and distributors. To ensure data is safe, a secure, cloud-based system is required, which can present its own set of challenges. Additionally, this system must be able to first collect data throughout the supply chain and then make it available for shared data analytics engines to trace products at every step to flag potential issues as they happen.
For example, imagine that a farm has sprayed a particular insecticide on its tomatoes to control weed growth. However, the application of the insecticide is not uniform. Later, in the production process, tomatoes with higher levels of the insecticide interact with other processing steps that cause a safety issue. A real-time monitoring, IIoT-based sensor and analytics system could identify and gain insight into the problem — which batch of tomatoes was tainted with higher levels of insecticide, as well as the process interaction — quickly and accurately. In addition to limiting wastage, it will provide valuable insight to help avoid future issues.
Implementing IIoT into your Facility
There is no denying the new benefits that IIoT technologies could bring to the food industry in helping reduce recalls. Yet many manufacturers are slow to make investments in the IIoT. Thin margins and extreme competition are key points for the food manufacturing industry to consider when deciding to invest in the IIoT. Knowing how the investment will pay off and where to focus first will enable food manufacturers to make smart decisions when implementing the IIoT into current processes. Here are three key considerations:
1. Expanding IIoT with improved critical control points
In the short term, revamping the whole food production process with IIoT-based monitoring can seem cost-prohibitive for most food manufacturers. However, the long term payoff could be instrumental to a plant’s success. Instead of an all-or-nothing approach, start with the areas that are most essential to food safety and quality, starting with Hazards Analysis and Critical Control Points (HACCP). Gathering and analyzing data from the most critical supply, manufacturing and distribution points in real-time will provide the greatest return in terms of mitigating the risk of recalls and finding those potential issues before they become costly problems. As these HACCP processes are continually improved over time, your IIoT “footprint” can include updated critical points, along with less critical processes, to improve efficiency and create insights to make the business more competitive.
2. Use the IIoT to ensure compliance
Every food manufacturer understands the impact of the Food Safety Modernization Act (FSMA), which increased individual facilities’ obligation to prevent threats to the food supply. Implementing IIoT technologies can help food manufacturers face this challenge. For example, moving to automated, in-line quality analysis makes test results immediately available to centralized quality systems via the IIoT. Real-time chemical and spectroscopic analysis data allows manufacturers to identify potential problems early in production and respond proactively rather than reactively, after the product has been produced and shipped. This drastically reduces the risk of a recall, fines and brand damage. This is one of the many applications of IIoT technology for compliance within the supply chain. Others include tracking the time a temperature-sensitive product is in transit between the refrigerated truck and the refrigerated warehouse or store, a critical point for damaging temperature trips. Another benefit IIoT provides is that the data produced demonstrates to regulators that the manufacturer is monitoring food quality and safety, a key compliance requirement.
3. Leveraging data to decrease risk
Data is the life source of the IIoT — it keeps everything running. Protecting that data — from the systems gathering information throughout the supply chain to in-flight data in the cloud to permanent repositories — is essential. That means investing in systems that ensure continuous operation of critical production and monitoring equipment through high-availability, fault-tolerant systems that prevent data loss. In addition, having a high-availability system gives manufacturers more peace of mind and increases confidence in these systems. However, continuing to rely on clipboards and other legacy paper-based approaches as a backup defeats the purpose of the IIoT and won’t allow you to experience the true benefits of an updated, automated process.
The IIoT Migration
Implementing IIoT processes is a marathon, not a sprint. Most manufacturers will start slow with a few implementations that target the most essential quality control points. As value is recognized from intelligent tracking, tracing and analysis of the supply chain and production process, IIoT infrastructure can then extend into new areas with more technologies. Reducing the risk of recalls will continue to be a high priority worthy of investment. But the IIoT also allows for major enhancements that impact other areas of the business — from enhancing production efficiencies to responding in real-time to product diversion and theft in transit to quickly evaluating consumer preferences to improve business agility. Take the first step: Begin with a thorough assessment of your entire supply and demand chain, and production process, to identify the most critical control points that can get you started on your IIoT migration.