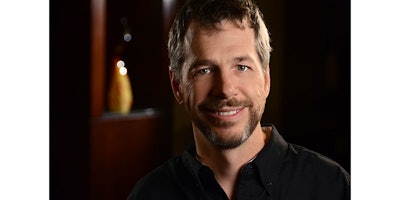
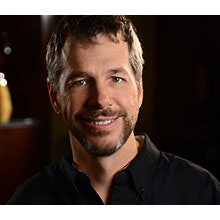
Maintaining quality is a constant, uphill battle filled with plant floor problems, right? That depends on how you look at it. If manufacturers re-imagine quality as an opportunity to unlock dramatic business improvements, they can stop using quality data in a reactive manner at the local level and, instead, use it for proactive, intelligent analysis that can transform the entire enterprise.
Today’s food and beverage companies grapple with managing quality across disparate manufacturing facilities and far-reaching global suppliers. In addition to being geographically widespread, these facilities and suppliers often have non-standardized quality processes and data collection procedures. As a result, data ends up siloed, quality initiatives focus only on individual lines and products, and each location operates like an island rather than a part of a greater whole. This makes it impossible for quality professionals and decision makers to conduct any high-level analysis for improvement opportunities.
By re-imagining quality and recognizing its transformative potential for your business, you can create a cycle of continuous improvement — an “Excellence Loop.” In the Excellence Loop, disparate data streams are unified and quality initiatives are extended throughout the entire enterprise with true enterprise visibility. Analyzing data from across operations uncovers operational insight that fosters global transformation in quality improvement, process optimization and your bottom line.
Enterprise Visibility
Many food and beverage manufacturers collect and house their quality data at the local plant level — in on-site databases, spreadsheets or filing cabinets. While locally stored data allows operators to take corrective measures after a process or machine fails or products fall outside of specifications at individual locations, data silos prevent quality professionals from sharing and applying improvements beyond a single line or plant. Further, these silos prevent key decision makers from seeing or analyzing what’s happening across operations.
But when data is unified, from all sources, it’s possible to visualize more than the quality of one product or production line. How? By turning to a cloud-based quality intelligence system and standardizing and centralizing data collection and storage in a single database. The result is real-time visibility of the entire enterprise, from end to end — including suppliers, incoming inspection, raw materials, in-process checks from shop floor operators and the quality lab, process data, packaging and finished products.
For instance, one of the world’s leading bottled water companies previously had a cumbersome paper-based system for collecting and analyzing data. When plant-floor issues arose that required immediate attention, its quality engineers had to disrupt operations to retrieve the necessary data from hand-written notes, which hurt efficiency. But by moving to a quality management system with data stored in the cloud, the company attained real-time visibility over production processes — both within individual sites and at the corporate level across 26 factories. By tracking trends in quality data, the company can now make more accurate and timely decisions about how to reduce overall defect levels and more efficiently run its manufacturing operations.
Operational Insight
With enterprise visibility, companies can leverage quality data to generate useful and actionable insight about their processes, suppliers and manufacturing operations. They can move from reacting to quality issues, to preventing them. Notably, a quality intelligence solution enables quality teams to see operational variances in real time. They can notice small changes in processes or machine performance, which can indicate the early stages of an issue, and thereby catch problems before they occur.
Furthermore, advanced analysis can be done to proactively identify opportunities for improvement that can significantly increase yield and efficiency across the enterprise. This changes quality professionals from reactive firefighters into quality and process strategists identifying continuous improvement opportunities. Suddenly, the answers to the organization’s most critical quality questions and concerns are available at their fingertips. Which production lines or sites are producing the most consistent products? What’s causing out-of-spec production? Where can I focus my improvement efforts and resources to get the biggest gains? Which products are at the highest risk, and where are these products produced?
For example, an innovative, international refrigerated food product company deployed cloud-based quality intelligence software and can now look across its enterprise to identify trends and improvement opportunities for cost reductions. And, it can identify the root cause of product variations and make adjustments before problems occur. Desktop dashboards with analyses and charts provide supervisors and executives with a real-time view across multiple plants, so they can see which plants, lines and products are running efficiently and consistently. Since implementing its quality solution, the company has reduced giveaway and the associated ingredient costs, and now produces a more consistent, higher quality product that consumes fewer resources.
Global Transformation
The resulting operational insights can be applied to streamline, optimize and transform processes and operations across the enterprise, elevating product quality, improving efficiency, impressing customers and creating exponential cost savings.
You can now tell which line or plant is running optimally. In addition, you can determine why and how to apply its best practices as standard protocol throughout the enterprise for global performance improvement and results. You see which factors matter, and which don’t. You begin to streamline all your processes. Consistency and efficiency increase throughout and across production sites. And you begin to see real, measurable benefits to your bottom line.
A leading North American consumer packaged food and beverage company implemented a cloud-based quality solution that pulls real-time manufacturing data from multiple locations into a secure, centralized repository. With all the data accessible in one spot, the quality assurance (QA) team can access and respond quickly to rising trends or make adjustments to variances and out-of-spec issues as they arise across different plants. This prevents waste, reduces “giveaway” and maintains a consistent taste profile for its products.
Flexible reporting capabilities and dashboards enable the quality team and management to slice and dice data to pinpoint new opportunities for improvement and perform predictive analyses. Plus, the power of cloud computing facilitates collaboration among facilities. Different locations can share their data and promote standardization to reduce plant-to-plant variations. With the ability to monitor and analyze real-time data from anywhere, the company has reported $2.1 million in savings due to waste reduction alone.
If your company is still looking at quality solely as fixing a problem on the plant floor, struggling with siloed data stored in local databases, or worse, employing manual or paper-based data collection processes, it’s time to re-imagine your approach to quality. With true visibility across the enterprise and actionable insight produced about your entire operation, you can streamline, optimize and transform processes and operations — across lines, across sites and around the globe. It’s time to take full advantage of your quality data and tap into the Excellence Loop.
For more information, download the InfinityQS white paper: “Quality Re-Imagined.”
About the Author
Michael Lyle is the founder and CEO of InfinityQS International, the global authority on data-driven enterprise quality. His leadership and vision for InfinityQS are the foundation of the company's success and rapid growth. Lyle’s adherence to a customer-driven development approach has ensured that InfinityQS’s solutions continue to address the growing, complex needs of the manufacturing industry.