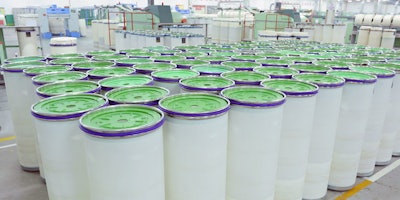
A New Approach To
Minimizing Downtime In
Highly Automated
Operations
White Paper
Facilities throughout the supply chain are increasingly installing large scale automation process and
handling technologies that require readily available routine maintenance supplies and spare parts
inventory to avoid costly downtime.
2 | P a g e
Introduction
Automated systems and technologies, long deployed by manufacturing facilities, are now moving
further into the supply chain to support distribution and fulfillment operations. Indeed, as The U.S.
Roadmap for Material Handling & Logistics noted:
The benefits of automation for material handling and logistics applications are many:
Machines are more reliable, do not tire or make routine errors; conveyors move
packages much more quickly than workers could carry them; automated systems incur
lower labor costs; workers are less prone to occupational injuries; and, in many
applications, automation is more cost-effective.1
Investment in automated systems and technologies shows no signs of slowing. Domestically, the
Manufacturers Alliance for Productivity and Innovation (MAPI) forecasts inflation-adjusted investment
growth of 10.3% in automation equipment for 2015.2 That aligns with the global market analysis for
worldwide automation investment, with an estimated compound annual growth rate (CAGR) of 8.08%
from 2013-2018.3
1 Kevin Gue, ed., โThe U.S. Roadmap for Material Handling & Logistics,โ http://www.MHLRoadmap.org, 47.
2 Modern Materials Handling, โMAPI Economic Forecast: Investment spending to drive growth,โ
http://www.mmh.com/article/mapi_economic_forecast_investment_spending_to_drive_growth, accessed November 24, 2014.
3 R and R Market Research, โSmart Factory Market by Technology (SCADA, DCS, PLC, ERP, MES, PLM, MOM), Field Devices (Industrial Network,
Robotics, RFID, And Motors & Drives, Relays & Switches, & Sensors), Application (Process, Discrete) - Global Forecast & Analysis (2013 - 2018),โ
http://www.prnewswire.com/news-releases/225b-smart-factory-market-automation-analysis-and-2018-forecasts-279319442.html, accessed
November 24, 2014.
Domestic Industrial Automation Growth
IHS Industrial Automationโs manager and principal analyst Alex Chausovsky saw 6.3 percent
growth in the automation machinery market in 2014, and anticipates the Americas becoming the
dominant growth engine for industrial automation sector, with sales growing by 6.9 percent.
DATA AND GRAPHIC SOURCE: Greenfield, Dave. โMotors and the Americas Drive Industrial Growth,โ Automation World,
http://www.automationworld.com/motors-and-americas-drive-industrial-growth, accessed December 4, 2014.
3 | P a g e
With expanding, multi-million-dollar investments in large-scale automation systemsโconveyors,
sorters, palletizers, robotics, case erectors and sealers, packaging equipment and moreโcomes
substantially greater emphasis on keeping everything running at peak levels of productivity. Ensuring an
automated facilityโs maintenance and repair operations (MRO) are properly equipped with routine
preventive maintenance supplies, tools and critical spare parts is essential to ensuring system uptime.
Types of maintenance4:
Corrective Maintenance โ Also known as Breakdown Maintenance, this is the
most common type of maintenance, and is performed when a piece of equipment
experiences a hardware or software failure. The goal is to get the equipment back to
working order as quickly as possible and minimize unexpectedโand costlyโ
production downtime. The repairs themselves can be considerably expensive, as
expedited spare parts acquisition and overtime man-hours are often required.
Preventive Maintenance โ Also known as Planned Maintenance, this involves
performing maintenance in an effort to avoid equipment breakdown and failures.
Preventive maintenance can be further broken down into Periodic Maintenance and
Predictive Maintenance.
Periodic Maintenance โ Time-based maintenance requiring periodic checks
that include inspecting, servicing and cleaning of the equipment. Replacing
gaskets, lubricating friction points and inspecting for wear are common
activities.
Predictive Maintenance โ Utilizing data about the equipment and its
operation to anticipate wear conditions. Through analysis of use trends,
deterioration diagnoses, and information about the expected useful life of
components, maintenance is scheduled and performed in a manner that
maximizes the partsโ useful service life.
4
CMMS Pro, โTypes of Maintenance,โ http://www.cmmspro.com/types-of-maintenance.asp, accessed December 4, 2014.
4 | P a g e
This white paper offers a formula to calculate the potential cost of downtime associated with automated
equipment failure, and outlines the benefits of a small-scale investment in automated storage and
retrieval equipment to maximize MRO efficiency.
The Potential Cost of Downtime
The shutdown of an automated system, whether scheduled for routine preventive maintenance
activities or unexpected due to a faulty or defective component that must be replaced, is costly. The
potential costs can be calculated based on three factors: labor costs, lost revenue and service costs. 5 6
Labor Cost = P x E x R x H
Calculate yours here:
Lost Revenue = (GR/TH) x I x H
Calculate yours here:
Service Costs
Further, and harder to calculate, are service costs. These might include:
๏ท Late delivery surcharges from customers
๏ท Overtime pay required to compensate for productivity losses
๏ท Delayed shipments that result in decreased customer satisfaction or loss of customers
๏ท Rush and overnight shipping costs associated with requiring a needed service part not
maintained in MRO inventory onsite
After adding up those (and other) service costs, divide the total by the number of hours of system
downtime to calculate cost-per-hour.
Careful consideration of all of these three areas of potential costs and losses from automated system
downtime has more companies evaluating alternative solutions to support in-house MRO practices.
5
North American Systems International, โThe True Cost of Downtime,โ http://www.nasi.com/downtime_cost.php, accessed
November 23, 2014.
6
Ibid.
number of people
affected
average percentage they
are affected
average employee
cost per hour
number of hours
of outage
gross yearly
revenue
total yearly
business hours
percentage impacted number of hours
of outage
5 | P a g e
Small-Scale Automated Storage and Retrieval Systems Support MRO
Because of the high value of these systems, and because of the potential high costs associated with their
downtime, many companies invest in hiring a team of in-house MRO professionals charged with
automation support. To do their jobs properly, companies also have to invest in a certain amount of
preventive maintenance supplies, tools and critical spare parts.
Yet, many operations new to automated systems have never had to maintain this type of MRO
inventory. Having the โright part, right place, right quantity and right time is as important in
maintenance as in order fulfillment. Itโs also a balancing act, since no one wants to shut down
operations because a repair isnโt available. At the same time, no one wants to invest more in expensive
repair parts than is needed to keep a facility running.โ7
To help companies find balance, large-scale automation solutions providers typically recommend a
package of key spare parts to keep on hand. But just having the parts somewhere in the building,
unaccounted for and in potentially questionable storage conditions, can leave them prone to becoming
lost or damaged.
Further, for companies that do designate a storage room or area for MRO supplies, tools and spare
parts, the space is usually small. Thatโs because most operations prefer to allocate valuable square
footage for profit-generating purposes, rather than facilities support.
As an alternative, small-scale automated storage and retrieval systems can provide highly dense storage
in an extremely compact footprint for a fraction of the dollars invested in the large-scale automation
equipment it supportsโparticularly when considering the costs of operational downtime.
7
Trebilcock, Bob. โMRO moves to materials handling,โ Modern Materials Handling,
http://www.mmh.com/article/mro_moves_to_materials_handling, accessed November 24, 2014.
A typical maintenance department with
standard shelving is shown on the left. A
Megamat RS vertical carousel provides clean,
organized and compact maintenance parts
storage, as shown below.
6 | P a g e
Three primary types of automated storage and retrieval include:
Vertical Carousels โ Comprised of a series of shelves that rotate
around a trackโsimilar to a Ferris wheelโthese automated
storage and retrieval systems deliver stored items safely and
quickly to an ergonomically positioned work counter at the
operatorโs command, eliminating walk and item search time.8
Vertical Lift Modules (VLMs) โ An enclosed automated storage
and retrieval system that consists of two columns of trays with an
inserter/extractor in the center. The inserter/extractor
automatically locates and retrieves stored trays from both columns
and presents them to the operator at a waist-high access window,
eliminating travel and SKU search time.9
Horizontal Carousels โ Consist of bins mounted on an oval track
that rotate horizontally to deliver storage locations to an operator.
These automated storage and retrieval systems eliminate
unproductive travel and search time by delivering
the product to an operator.10
How Automated Storage and Retrieval Systems Benefit MRO in Highly
Automated Operations
Highly automated facilities that implement small-scale automated storage and retrieval systems to
support MRO activities will benefit in a variety of areas. Among them:
๏ท Centralized Storage: By implementing an automated storage and retrieval system dedicated to
the storage of maintenance supplies, tools and spare parts, an operation can be assured that all
items are kept in a centralized, designated location. With everything stored in one or two
automated storage units, items can be easily found and accessed, minimizing search time.
๏ท Better Organization: To help maintenance technicians find the items they need even faster, the
equipment can be outfitted with partitioned trays or totes for organization and easy location of
small components, such as screws, nuts and bolts. If the machine is also integrated with
8
MHI, Order Fulfillment Solutions Industry Group, โVertical Carousels,โ http://www.mhi.org/ofs/solutions-guide/vertical-
carousels, accessed November 24, 2014.
9
MHI, Order Fulfillment Solutions Industry Group, โVertical Lift Modules,โ http://www.mhi.org/ofs/solutions-guide/vertical-lift,
accessed November 24, 2014.
10
MHI, Order Fulfillment Solutions Industry Group, โHorizontal Carousels,โ http://www.mhi.org/ofs/solutions-guide/horizontal-
carousels, accessed November 24, 2014.
7 | P a g e
inventory management software, stored items can be tracked and located by quantity, length of
time stored, or their association to each individual type of automated equipment and the
maintenance it requires.
๏ท Track and Trace Accountability: The inventory management software can also provide
traceability. To access stored contents, authorized operators can be required to first input a
software-traceable personal login and password. For operations that wish to keep track of
consumables (such as lubricants and filters) or shared tools and gear (from screwdrivers and
ratchets to welding helmets and other safety items) required to service equipment, this
additional measure of accountability allows depleted, missing or misplaced items to be quickly
tracked back to an individual.
๏ท Parts Protection: Because the automated storage and retrieval machines can be fully enclosed,
the supplies, tools and spare parts stored inside are protected from exposure to the dirt and
dust common to distribution and fulfillment operations. This maximizes the useful life of the
items, preventing scrap and waste.
๏ท Maximum Storage Density: Installing high-density automated storage equipment significantly
reduces the amount of square footage required to store MRO parts and supplies. The equivalent
amount of items held in 120 bays of static shelving can be condensed into two horizontal
carousels (66% space savings), two vertical carousels (75% space savings) or a single vertical lift
module (85% space savings). To further maximize cubic density, VLMs employ a sensor that
measures the height profile of each storage trayโs contents, then allocate the trays dynamically
at incrementally variable heights. This permits storage trays to be placed within 1-inch of each
other, producing up to 50% more storage capacity.
๏ท Enhanced Ergonomics: Because MRO spare parts, components and consumablesโsuch as
motors or bulk quantities of lubricantsโcan be heavy and difficult to move, technicians may be
reluctant to store the heavier items on shelving. But leaving these items on the floor can pose a
trip hazard. Alternatively, every item stored in an automated storage and retrieval system is
delivered at the correct ergonomic work height. Called the โGolden Zone,โ the unitโs opening is
positioned waist-high, eliminating bending to retrieve an item stored low, or stretching to grab
an item stored high. Further, the system minimizes unnecessary or excessive motions required
for retrieval of items from drawers or shelves, including lifting, reaching, walking, stretching,
bending, pushing, pulling, twisting, spinning or stooping. The automated storage equipment
substantially lessens the chance of injury and absenteeism, while also reducing insurance
premiums and claims for workerโs compensation.
To learn more about how implementing an automated storage and retrieval system to support your
automated operationโs MRO activities, contact your Kardex Remstar representative today.
# # #
About Kardex Remstar
Kardex Remstar, LLC, a company of the Kardex Group, is a leading provider of automated storage and
retrieval systems for manufacturing, distribution, warehousing, offices and institutions. For information
about the companyโs dynamic storage solutions, call 800-639-5805 or visit www.KardexRemstar.com.