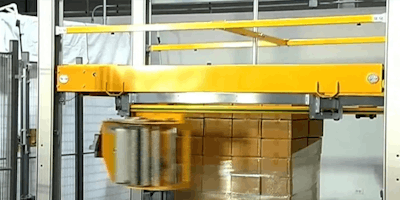
Variable Tension for Invariable Commitment
Muller’s Octopus Stretch Wrapper Proves the Right Solution
for Safely Delivering Hidden Valley Ranch with 30% Savings
The extraordinary tale of the Hidden Valley Ranch® dressing brand expansion is still evolving. A
local recipe that started on a Santa Barbara, CA, "dude ranch" in 1954 is now the dominant
salad dressing choice of Americans. However, The Clorox Company®, which bought the brand in
1972, has even bigger plans. The company has its sights set on the condiment/dip sector as the
next frontier to conquer.
The first thing that comes to mind when you think of Clorox might not be food. However,
besides Hidden Valley Ranch, the company also owns the popular K.C. Masterpiece® sauces and
the Brita® brand of water filters. What may come to mind more often with Clorox is a
commitment to quality. The Clorox Company protects its 20 or so brands obsessively with
rigorous production standards and thorough quality controls.
The Clorox commitment to quality control is top-to-bottom, and nothing escapes its watchful
eye. When the company recently sought to update the stretch wrapping equipment at its
Hidden Valley Ranch, Reno, NV, facility, it would accept no less than the safest, most user-
friendly, and cost-efficient equipment they could find. Having successfully incorporated Muller
stretch wrapping equipment across other Hidden Valley Ranch and Clorox facilities, the choice
was clear.
Clorox seeks out partners that share its commitment to quality. “We have pretty strong
corporate standards,” says Doug Rhoades, Process Blending Manager, Hidden Valley. “We felt
good about how responsive Muller was to all of our requests. From electrical standards to
safety standards, Muller met them all.”
Always Putting Safety First
The Clorox Company has nurtured a global reputation for the most demanding manufacturing
standards and specifications- known as their World Class Operations (WCO) standards. A top
priority within Clorox, and part of the WCO standards, are specifications related to the safety of
equipment operators. This concern includes complete operator-friendliness, ergonomics for
loading and maintenance, and easy access to all parts of the machine for service. Clorox’s
control over the production line is demanding because of its obsessive goal of keeping
machines running at all times. Easy access to all of the parts of the machine means faster
routine maintenance and quicker repair turnaround times.
While few companies require WCO, fewer can meet the criteria. However, Muller’s extensive
line of stretch wrapping machines meet high standards themselves, but are also highly
customizable. The Hidden Valley Ranch facility in Reno, NV ultimately chose the high speed,
steel frame Octopus automatic rotary ring machine - the versatile flagship of the Muller line of
pallet wrappers. Purchasing a new stretch wrapper afforded Clorox the opportunity to make
improvements to safety. They even expanded their commitment by retrofitting older Octopus
machines throughout their organization with new guarding and ring locking technology.
“The safety was important,” says Rhoades. “Our old equipment wasn’t as safe to get into. The
guarding and interlock systems of the Octopus machine are unmatched. Now we can virtually
rule out any chance of injury.”
“Muller always goes the extra mile,” says Dan Schmidt, Business Development Manager,
Muller. “Creating customer specific solutions is what we do best.”
Finding New Efficiencies All Around
At the Hidden Valley Ranch Reno facility, the Octopus machine replaced a turntable style
wrapper. The speed and reliability of the machine was important, as well as its ability to wrap
double stacked loads. The Octopus has the unique ability to start and stop anywhere on the
load because the cut and clamp components reside on the ring. This allows for unmatched
wrapping flexibility to meet the most challenging applications.
In addition, the variable tension capability of the wrapper creates many efficiencies on its own.
Instead of operating with a singular tension setting, variable tension control allows for
increased tension at locations on the load that require extra hold (the base of a sturdy box) and
lighter tension where reduced force is beneficial (sharp corners, the top of an open box). With
frequent changes in primary packaging design across many SKUs, it is crucial to have a system
that offers flexibility and variability in order to optimize the stretch wrapping function.
At the Reno facility, the faster new machines and variable tension were not easy sells at first.
The staff was worried about what film thickness would run best for all the 28 SKUs of Hidden
Valley Ranch products that the Reno facility shipped. The sticking point was that the old
wrapper had a difficult time running the lower grade stretch film that they had been using.
The previous machines were barely able to consistently run the 80-gauge material at 200% pre-
stretch. How could they effectively switch to a machine like the Octopus that was 2.5-times
faster than their old automatic turntable wrappers? They were afraid it would keep breaking
the film by wrapping as such higher speeds. Muller convinced Clorox to go with 250% pre-
stretch gears at two and a half times the rotation speed.
Muller’s confidence in the Octopus’ ability to perform at such a high level is a result of seeing
numerous other customers increase productivity and reduce film breaks by adding variable film
tension control. This allowed Clorox to program how much tension they desired per revolution
right at the HMI touchscreen. By adding this feature, not only were they able to run the same
film at much higher pre-stretch and faster speeds they were also able to increase the load
containment (force to load) on each pallet. This combination offered a tighter wrap and
reduced the chance of damaged loads.
As a result of the switch to the Octopus wrapper, Clorox reduced film consumption by about
30% in the first year on the main line in the Reno plant. “The variable tension is great,” says
Rhoades. “It worked as promised and helped us be more efficient- our material and cost savings
are considerable. The fact that the operator can adjust settings quickly and easily is an added
bonus.”
Everything World Class
Another aspect of Clorox’s high standards was the electrical specifications required of all
machines at Clorox facilities. The Octopus machine was put through its paces, but came
through unscathed. Muller brought tremendous value to the Reno plant by meeting all their
expectations and also made the machine more compatible with the parts inventory in the plant.
Meeting the WCO standards and exceeding the performance expectations of the customer are
key factors in a successful new Clorox installation. But it doesn’t stop there. New equipment
often means new training, so it’s up to the manufacturer to ease that transition, as well.
Early on, Clorox and Muller worked together to create training documentation that helped the
operators quickly learn all the different aspects of the machine. This produced operators that
understood the machine inside and out, were proficient at the HMI touch-screen control panel,
and were efficient with changeovers.
“Operator training went very smoothly,” says Rhoades. “Muller was always very helpful; we
never had any issues. From the onset to the factory test to commissioning, the transition went
effortlessly.”
The Reno plant wraps over nine million cases of Hidden Valley Ranch a year—heading toward
even more. The operations data since the switch to the Octopus has been impressive. The plant
reports virtually no downtime. For the past year, the line averaged 99.68% utilization on that
piece of equipment.
“The Octopus wrapper worked well from a world class operations standpoint, as well as for lean
manufacturing” says Rhoades. “We would definitely work with Muller again.”
www.mullerlcs.com