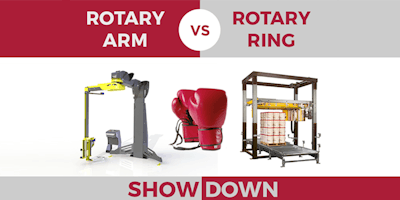
Muller LCS
R0 IARY ARM vs. R0 IARY RING
Going automated is the obvious choice when wrapping 60+ loads an 4 ‘V/
hour. But if you have a high volume job and a need for speed, it really I
only comes down to two options; rotary ring or rotary arm. In theory. “Ff ' j", flfi‘l
both these machines do the same job, right? They use the same basic .. "'Mr
principal to apply stretch film to the pallet by going around the load. _ ii
But there is of course, this not so subtle difference; one uses and arm c2“
. < L.
and the other a ring. 1—.
Octopus Rotary Ring
50, it’s time to answer the age old question;
Which is better and why? I I
—
Cobra Rotary Arm
Turning a ring around a load is inherently faster because it doesn't require as much inertia as a
rotary arm. Rotary arms don't hold up nearly as well to speed because of the wear and tear from
stress created by a less ergonomically friendly design. The centrifugal force causes the film end to
pull away from the machine base. In fact, if not lagged to the ground, this force would cause the
entire machine to topple over at high speeds. The ring model keeps the force contained and
balanced throughout the machine- making it easier to achieve higher speeds without
compromising the equipment or production.
:‘"
' FOOTPRINT WINNER: TIE
There isn’t a clear winner here. The size really depends on the model of machine. Sometimes the
arm is going to be smaller, sometimes the ring. In the end, both the rotary arm and rotary ring
provide similar footprints and can be installed in the similar locations throughout the plant.
Rotary arms have limited wrap patterns because you are always starting a wrap at the bottom,
working up, and finally clamping at the top. Many rotary rings, like our Octopus line, have over 200
different wrap patterns to choose from and can start and stop anywhere on the load. The ability to
pre-program wrap patterns also means various pallets can be wrapped without hesitation or
operator interface. For lighter loads, like cereal boxes, this advantage also enables users to add film
in weak or vulnerable spots such as the middle or the top.
O
0 MAINTANENCE W N N ER, RING
Ease of use makes the ring a clear winner. The ring frame can be brought down to ground level,
making it a comfortable and safe level to work on. If that wasn’t proof enough that the ring should
win in the maintenance category, no gear boxes at the top of the machine and the use of web belts
to lift the frame- virtually eliminating lubrication points—puts ring over the top. In contrast, rotary
arm machines have the chain drives and gear boxes at the top of the machine, creating the need for
a ladder-- and with more parts, chains and wires, the overall maintenance is cumbersome and
costly.
It goes without saying that having the ability to bring the rotary ring down to a comfortable position
is safer than having technicians climb ladders to troubleshoot equipment. But it also helps that you
can load film by bringing the ring to you. Rotary rings also offer the option of an Auto Roll
changer—this obviously reduces the chance of accidents because the machine is doing the work,
eliminating the need for operators to be near the wrap zone. For applications that require a top
sheet, manufacturers using rotary arm solutions need to install an overhead hoist and have two
workers hold the top sheet in place while the wrapper secures it with a couple revolutions of film.
Top sheet film rolls also weigh upwards of 70lbs. The weight alone requires a forklift or crane to
position the film. In contrast, the Octopus rotary ring solution is again brought to floor level for easy
loading. Then, with a push of a button, the top sheet is automatically positioned and applied
without operator involvement.
There’s also potential load contamination and slip hazards associated with rotary arm technology.
Since the lubrication and main pivot points rest on the top of the arm directly over the pallet of
goods, it's common for oil and grease to drip on product or the floor. This is especially troubling for
food manufacturers and general food handlers where this type of contact with oil and grease
creates contamination concerns. In contrast, rotary ring machines eliminate these problems since
there are no lubrication points overhead.
' SAVINGS WINNER: TIE (well, sort of)
If you are talking the upfront cost of the machine, the rotary arm tends to have a lower entry price.
But, if you are evaluating the total cost of ownership, with increased flexibility, less maintenance and
greater safety, the rotary ring solutions provide a greater return in the long run. Our Octopus users
save 25-30% in film usage alone with the ability to tailor film tension settings and wrap patterns.
—
In the end, either solution will get thejob done. Both solutions wrap quickly a m u I I e r
and effectively. There's a lot to consider, and we’re here to help you make
those decisions and support throughout the lifetime of your machine.