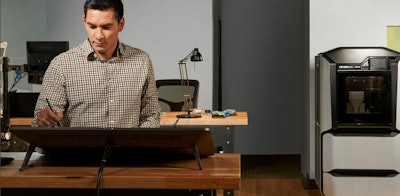
THE 3D PRINTING SOLUTIONS COMPANY™
3D printing’s contributions across the design, engineering and manufacturing disciplines
are not new. The technology has been available in various forms for over thirty years and is
often lauded as the next industrial revolution.
Breaking The Barriers
H O W W E M A D E R A P I D P R O T O T Y P I N G S M A RT E R , FA S T E R A N D
M O R E P R O D U C T I V E
Breaking The Barriers
H O W W E M A D E R A P I D P R O T O T Y P I N G S M A RT E R , FA S T E R A N D
M O R E P R O D U C T I V E
Despite some inflated claims, there’s no denying
that 3D printing, also referred to as additive
manufacturing, has achieved its place as a
valuable design and manufacturing methodology,
and a cornerstone of rapid prototyping (RP). It
lives up to the promise of making businesses more
competitive by giving them the tools to streamline
and enhance the product-creation processes.
This white paper will show there’s never been a
better time to invest in 3D printing, a fact made
possible by the introduction of the Stratasys
F123™ 3D Printer Series. These 3D printers
were designed to remove the barriers designers
and engineers face by making the RP process
more efficient and productive. You’ll see how the
Stratasys F123 Series addresses typical rapid
prototyping pain points and lets companies create
better products faster, reducing the time
to market.
MAKING YOU MORE
PROFITABLE
It’s no secret that businesses need to quickly
respond to changing customer and market
demand to stay competitive. That’s true for
small design firms as well as large, established
manufacturers. Getting a new product out before
your competition helps you generate new revenue
and maintain market leadership. But doing that is
not easy, particularly if you’re competing on the
same level as your competitors and using similar
technology and processes.
Changing your product development methodology
to incorporate additive manufacturing is a proven
means to gain a competitive advantage. It can
The Stratasys F370™ 3D Printer.
BREAKING THE BARRIERS / 2
Breaking The Barriers
H O W W E M A D E R A P I D P R O T O T Y P I N G S M A RT E R , FA S T E R A N D
M O R E P R O D U C T I V E
drastically reduce new product development time
and provides the ability to refine designs optimally
to ensure they’re ready for market.
However, embracing this technology or
broadening its use, is often avoided for a number
of legitimate reasons. Investing in professional
3D printers can pose a significant financial hurdle
and companies find it difficult to justify the
cost, especially for small to midsize companies.
Many types of additive manufacturing require
comprehensive knowledge of the process and
equipment. That typically means hiring new
employees, increasing the payroll.
Even companies that already use 3D printing for
rapid prototyping face challenges making the
most of this technology. If the 3D printers aren’t
readily accessible to the users, if the workflow is
cumbersome and complicated or the equipment
is unreliable, benefits will be minimal from
inefficient use.
Choosing to stay with the status quo using
traditional rapid prototyping methods poses risks,
too. In the race to develop new products quickly,
chances for field failures increase because there
is not enough time and resources to adequately
vet and test more than a few design iterations.
It’s simply too costly to develop multiple designs
using the old methods, particularly if portions of
the process are outsourced.
So what simple, reliable and efficient technology
is available to help product developers become
more competitive? The answer lies with a new
professional 3D printing platform designed to
increase the efficiency and simplicity of the rapid
prototyping process. This new technology is the
Stratasys F123 Printer Series. These FDM® (fused
deposition modeling) 3D Printers provide solutions
that help companies become more competitive
through RP adoption and improve their existing
RP processes.
This motocross helmet and the attached red accessories were
prototyped and 3D printed using the Stratasys F370 3D Printer.
BREAKING THE BARRIERS / 3
Breaking The Barriers
H O W W E M A D E R A P I D P R O T O T Y P I N G S M A RT E R , FA S T E R A N D
M O R E P R O D U C T I V E
To understand how they achieve this, let’s take
a closer look at how these 3D printers address
the typical challenges CEOs, engineering and
prototyping managers face in the product
development process.
The Challenge: Slow Process
“It takes too long to develop new products, which
increases the chance that our competitors will
get to market first. This can negatively impact our
ability to generate new revenue. We also don’t
have sufficient resources to fully test multiple
design iterations, leading to a higher risk of
field failures and declining revenue. We need a
simple system that speeds up all facets of the
RP process.”
How We Make Things Quicker
The hallmark of the Stratasys F123 3D Printer
Series is that it is designed to meet the needs of
the total RP process: concept verification, design
validation and functional testing. And it will do this
with economy and speed in a workgroup setting.
Rather than using less-optimal materials,
printers or service bureaus for early iterations,
Stratasys F123 Printers can quickly create multiple
options for design or customer review. Multiple
material choices include economical PLA or the
durability of engineering thermoplastics like ASA,
ABS and PC-ABS.
The same benefits apply to the design validation
phase. The ability to produce multiple designs
much faster gives you the time to refine and
optimize the design. The durability of engineering-
grade plastics also makes functional tests
possible, ensuring the final part will operate
as intended.
Prototyping in-house with local 3D printers also
protects your intellectual property. There’s no
Engineers went from concept to fully functional prototype for this traffic
signal that incorporates UV-resistant ASA material.
BREAKING THE BARRIERS / 4
Breaking The Barriers
H O W W E M A D E R A P I D P R O T O T Y P I N G S M A RT E R , FA S T E R A N D
M O R E P R O D U C T I V E
risk that confidential design information will fall
into competitors’ hands through outside machine
shops and service bureaus.
The Challenge: The Lack of Expertise
“We don’t have the expertise to operate a 3D
printer, nor the budget to hire additional specialists
to work with them. We need a rapid prototyping
technology that’s easy to use and can be shared
by multiple engineers in our group.”
How We Make Things Simple
Most 3D printing platforms require trained
individuals knowledgeable about printer operation,
file manipulation and troubleshooting. The
Stratasys F123 Series printers are designed for
ease of use, from the initial setup through the
design-to-print workflow.
The printers employ a plug-and-play architecture,
with automatic setup and test functionality. Once
the printer is powered up and completes these
steps, it’s ready to use. There’s no need for a
special technician dedicated to printer operation
and maintenance.
GrabCAD Print™ software makes the task of
printing parts easy too. It’s formatted similar to
CAD software, which is familiar to designers and
engineers. Once parts are designed, the engineer
simply hits the “print” command to print the parts.
File sharing is also possible through GrabCAD
Print, so members of a design or engineering
workgroup can collaborate in the design process
and share access to the 3D printer. Each printer is
also Wi-Fi-ready, making the 3D print function as
easy as 2D printing from an office computer. Or, if
Wi-Fi is unavailable, files can be printed via USB
or Ethernet cable.
Monitoring the progress of a print job is simple,
thanks to the printer’s built-in camera. Users
can check the print status directly from their
workstation with GrabCAD Print or through an app
on their mobile device.
This prototype smart-home switch with fine features was enabled by the
0.007-inch resolution on the Stratasys F123 Printers.
BREAKING THE BARRIERS / 5
Breaking The Barriers
H O W W E M A D E R A P I D P R O T O T Y P I N G S M A RT E R , FA S T E R A N D
M O R E P R O D U C T I V E
The Challenge: The Lack of Space
“We’ve considered using 3D printing for rapid
prototyping but it has a reputation of being a slow
process and needs a dedicated, separate space
because of the noise and materials that are used.
Our design and engineering office doesn’t have
any separate factory space to locate a 3D printer.”
How We Make Things Fit
For fast printing speed, Stratasys F123 Printers
include Fast Draft print mode, which operates
at twice the speed of the standard FDM print
operation while typically using only one-third
the material. This lets you 3D print models very
quickly, whether it’s for faster part iterations
to validate design concepts or to quickly print
multiple concept models for management or
customer buy-in.
More importantly, these 3D printers are
designed for the office environment. They use
a clean build process with no hazardous
chemicals or materials and operate using
standard 110-volt office electrical power.
3D printed models are built in an enclosed,
insulated build chamber with an auto-locking
door for safe operation and no risk of outside
physical interference. Noise insulation provides
exceptionally quiet operation, under 46 decibels,
which is similar to a residential refrigerator.
The Challenge: The Lack of Options
“Our 3D printer uses only one type of material
but we’d like to develop prototypes using several
different materials. Also, replacing empty material
cartridges is cumbersome and time consuming.”
How We Make Things Flexible
Designed with versatility in mind, the Stratasys
F123 Printers are capable of printing with
several materials, each one tailored to meet
specific requirements.
PLA is an economical choice, providing the
best option when you need fast model creation
and/or need to print them in greater quantity.
ASA, ABS and PC-ABS are engineering-grade
This prototype carabiner design has a flexible living hinge made possible
with Stratasys F123 Printer engineering plastics.
BREAKING THE BARRIERS / 6
Breaking The Barriers
H O W W E M A D E R A P I D P R O T O T Y P I N G S M A RT E R , FA S T E R A N D
M O R E P R O D U C T I V E
thermoplastics that offer flexibility when models
and prototypes need differentiation, such as UV
light resistance or high strength and durability.
These materials can also be printed in Fast
Draft mode.
To make material changes and replacements
much easier, Stratasys F123 Printers use self-
positioning filament spools designed for the
fastest replacement of any FDM 3D printer in the
marketplace. Changing or replenishing material
takes no more than a minute to remove and
replace the empty spool and feed the filament
into the bay drive. Spools are located in an easily
accessed drawer at the front of the printer. When
changing between different engineering plastics
(non-PLA), there’s also no calibration required nor
any need to change printer head tips.
The Challenge: Too Much Downtime
“Our 3D printer isn’t a very reliable system,
resulting in more downtime than is reasonable,
making it an unproductive investment.”
How We Make Things Reliable
Stratasys F123 3D Printers offer the most reliable
FDM capability in the market, fulfilling one of
their primary design requirements. It starts with
the deliberate decision to use industrial-quality
components coupled with design best-practices
from over 25 years of Stratasys FDM development.
More importantly, over 100,000 hours of reliability
testing was accomplished to prove out the
design reliability performance of the Stratasys
F123 Series.
MAKING IT FIRST
FDM 3D Printers create models and prototype
parts directly from digital data, quickly, easily
and locally, for concept verification, design
validation and functional testing. That’s a
game-changing advantage in a competitive
market where the winner is often decided by
who gets to market first. It antiquates traditional
methods of prototyping that rely on expensive
and time-consuming modeling machining or
injection molding.
As proof of this advantage, the Stratasys F123
3D Printer Series itself was developed using the
same time- and cost-saving FDM technology and
capabilities they are designed to offer: namely,
faster concept validation and functional testing,
resulting in a better product.
How We Made it Perfect
To provide faster print speeds and the capability
for multiple materials, the Stratasys F123 Printers
required a new print head design. Stratasys
BREAKING THE BARRIERS / 7
Breaking The Barriers
H O W W E M A D E R A P I D P R O T O T Y P I N G S M A RT E R , FA S T E R A N D
M O R E P R O D U C T I V E
engineers created multiple versions of the head
and 3D printed them. In total, over 20 design
iterations were created and 80 head housings
3D printed during the design development and
verification stage.
This seemingly repetitive process was necessary
to refine the design to ensure accuracy and
achieve a precise fit with mating parts. These
parts were also used for functional testing, going
beyond just concept and design validation, and
were even used in some of the initial printer
assembly prototypes. The capabilities of FDM
thermoplastics provided the durability needed to
mirror the engineering specifications required for
the injection molded final head design.
To achieve this level of rigor in design qualification
and testing without FDM technology would be
exceptionally expensive and time consuming.
Stratasys estimates that injection-mold
prototyping tools for the head unit would have cost
approximately $10,000 each. Producing molds
for 20 design prototypes would be exorbitantly
expensive, not to mention the lengthy lead time
required to produce them.
The ability to create multiple design iterations
not only helped distill the best configuration for
the print head quickly, it also gave engineers
substantial data from which to derive statistically
significant test results. Numerous design
iterations help unmask potential flaws that less-
rigorous methods may not detect until post-
The end cap on this stepper motor was 3D printed to perform functional tests for proper fit.
BREAKING THE BARRIERS / 8
Breaking The Barriers
H O W W E M A D E R A P I D P R O T O T Y P I N G S M A RT E R , FA S T E R A N D
M O R E P R O D U C T I V E
production, risking product callbacks and other
quality problems.
In total, engineers 3D printed over 1000 parts for
15 different components in the Stratasys F123
Series design verification phase.
Without the FDM process, these prototypes
would have been made with formed sheet metal,
CNC machining and injection molding, requiring
substantial time and cost outlay for this level
of design rigor. The capability to 3D print and
test many different designs produced the best
configuration to prove the reliability of the
final product.
Additionally, all of this development took place
within the security of Stratasys facilities. This
minimized the risk of confidential intellectual
property falling into the wrong hands, a possibility
when prototyping is outsourced.
Making Things More Precise
Perhaps the best illustration of where FDM
technology benefited Stratasys engineers was in
the creation of the oven air duct. The beauty of
additive manufacturing is that it frees designers
from design-for-manufacturability constraints,
allowing the creation of virtually any shape
and configuration.
Achieving the goal of consistent, reliable build
results from Stratasys F123 Printers required a
tightly controlled temperature profile within the
build chamber. To do this, Stratasys engineers
needed to create an air duct with the optimal
size and geometry for precise air management.
Mathematical and thermal modeling gets you in a
range of what is required, but it can’t provide exact
results. Trial and error through multiple 3D printed
design iterations allowed Stratasys engineers to
achieve the precise, organic duct configuration
that enabled the correct temperature profile. It
would have been very difficult, if not impossible,
to obtain the desired results with traditional, non-
FDM prototyping methods and materials.
Stratasys F123 print head design iterations developed with FDM rapid
prototyping technology.
BREAKING THE BARRIERS / 9
Breaking The Barriers
H O W W E M A D E R A P I D P R O T O T Y P I N G S M A RT E R , FA S T E R A N D
M O R E P R O D U C T I V E
Making Supply Easier
FDM technology not only provides the tools that
shrink the product development and improve
the opportunity for design optimization. It also
offers added insurance against supply chain
risks. In the development of the Stratasys F123
Series, engineers relied on a supplier for several
final-production parts for validation testing. The
supplier wasn’t able to meet the development
timeline, which threatened a six-week delay. To
avoid the setback, Stratasys engineers 3D printed
equivalent parts using FDM technology and kept
the unit production schedule on track.
MAKING IT COST-EFFECTIVE
Engineering departments humming with multiple,
productivity-enhancing 3D printers might seem
like the next logical evolution of the design office
as 3D printing becomes more accessible. This
is especially true as the technology continues to
mature and more low-cost, consumer-level 3D
printers enter the market.
Consumer 3D printers may seem like an attractive
RP solution because they’re often compact and
very affordable. They offer a low barrier of entry to
inexpensive, in-house rapid prototyping capability
and intellectual property security. While it’s an
appealing strategy, it’s not without risk. Yielding
to the seduction of low-priced equipment will
often limit your long-term prototyping capabilities,
growth plans and day-to-day equipment uptime.
In contrast, professional 3D printers like the
Stratasys F123 Series provide additional value
that justifies the investment, through increased
capability, efficiency and reliability, illustrated by
the following features and attributes.
Making Complex Projects Simple
Certain geometries can’t be 3D printed without
material that supports overhanging features and
nested assemblies during the build process. Most
consumer desktop printers lack support material
capabilities for complex geometries like internal
cavities and interlocking parts, which limits the
design complexities that can be printed.
In contrast, the professional Stratasys F123 Series
uses a unique and effective soluble support
material, enabling more complex designs and
fine details that include thinner walls and internal
cavities, enabling unlimited design freedom.
The hands-free removal process also saves
labor, making the RP process more productive
and efficient.
BREAKING THE BARRIERS / 10
Breaking The Barriers
H O W W E M A D E R A P I D P R O T O T Y P I N G S M A RT E R , FA S T E R A N D
M O R E P R O D U C T I V E
Make to Keep Its Cool
Controlling the temperature of the “oven”, the
enclosed build chamber of an FDM printer, is
critical for maintaining design specifications as the
part is built. Curl is an inherent behavior of plastic
as it cools from a melted state and controlling this
characteristic is essential to maintain part quality,
particularly for long, flat parts. This is achieved
with uniform airflow and complex temperature
control throughout the build area.
Desktop printers don’t have controlled build
chambers. This limits the type of parts you can
build as well as the consistency of obtaining
quality results. Stratasys F123 3D Printers achieve
tight temperature uniformity across the build
plane, with no “dead spots”, through a highly
specialized design of electronics and temperature-
control algorithms. This allows the creation of
large, flat parts that can be printed in a variety of
densities from sparse to solid fill modes without
the risk of curling.
Made to Last Longer
3D printers used in workgroup settings usually
experience high utilization, placing significant
demands on the mechanical components.
You don’t want your workgroup’s productivity
hampered by poor printer reliability, resulting in
frequent downtime. Stratasys F123 3D Printers
are designed and built for high utilization, using
durable components such as:
• Servo motors (vs. stepper motors) that are
quieter and more robust for high-torque
applications and dynamic load variations during
printer operation, providing better control and
more precise movement. Most low-priced
desktop FDM printers use less expensive
stepper motors, which typically produce a
The soluble support capability of Stratasys F123 Printers made it
possible to prototype this camera lens cover with an adjustable aperture.
BREAKING THE BARRIERS / 11
Breaking The Barriers
H O W W E M A D E R A P I D P R O T O T Y P I N G S M A RT E R , FA S T E R A N D
M O R E P R O D U C T I V E
high-pitch whine making them bothersome in an
office setting.
• Durable motion-control components like linear
profiled rails with ball bearings (instead of sleeve
bearings). They provide better repeatability
and accuracy of the 3D printed part, smoother
and quieter operation, greater load-carrying
capability and maintenance-free operation.
Many low-cost desktop printers don’t use linear
profiled rails, lowering the chance of repeatable
part accuracy.
Making You More Productive
Stratasys F123 3D Printers offer multiple features
that increase a workgroup’s productivity. GrabCAD
Print software enables print queue and multi-tray
management, giving your team visibility to each
member’s print jobs, the ability to manage the
print sequence and prioritize important jobs. The
software also imports native CAD files, making it
easier and faster to go from CAD model to print.
Stratasys F123 user interface touch screens
display in 10 languages, offering ease of use
across global markets. The user interface on most
desktop 3D printers has limited functionality and
minimal language options.
Made by the Name You Can Trust
There’s value in establishing your rapid
prototyping infrastructure on proven technology,
produced by a company with market tenure. 3D
printer manufacturers lacking this experience
may be here today but gone tomorrow, cutting off
access to spare parts, material and support. The
Stratasys F123 Series is a professional 3D printing
platform, based on over 25 years of Stratasys
experience developing and supporting 3D printers,
materials and customer solutions.
The Stratasys F123 3D Printer touch screen with multi-language display.
BREAKING THE BARRIERS / 12
BREAKING THE BARRIERS / 13
MAKE THE NEXT STEP
If you’re in the business of designing and
developing new products, the Stratasys F123
3D Printer Series offers the straightest path to a
positive impact on your bottom line. These 3D
printers enable your designers and engineers to
move rapidly from design concept through part
verification to functional prototype in a fraction of
the time, compared with traditional prototyping
methods. That gets your product to market
faster and reduces post-production quality
problems. It also increases your chances of
beating the competition.
These 3D printers are designed for ease of use
and shorter, streamlined workflows that give
your team the capability, reliability and simplicity
they need in an RP platform to iterate, refine
and perfect designs. They can do that in an
office environment with clean, safety-certified
3D printers that are the quietest on the market,
using three engineering-grade plastics, plus the
economical choice of PLA.
This solution is not only for companies new to
3D printing but for long-time practitioners of
the technology. That’s because Stratasys F123
3D Printers maximize yield through reliable
performance and simplified workflow, beyond
what’s currently available in professional or
consumer 3D printers.
Stratasys F123 3D Printers leverage the time-
tested durability and success of Stratasys FDM
technology to offer the highest level of reliability
out-of-the-box. Over 100,000 hours of testing
support that assertion.
How would your company benefit if you could
cut your product development time in half, or by
an even greater percentage, compared with how
long it takes today? How much more efficient
would your design and engineering workgroups be
with accessible, reliable 3D printers and a simple
CAD-to-print workflow? With Stratasys F123 3D
Printers, there’s never been a better opportunity
to take advantage of FDM technology to improve
your business operation.
A Stratasys F123 Series 3D Printer is designed
to be a team player, for the way you work. Learn
more at Stratasys.com or contact a Stratasys
representative, and take the next step to
smarter prototyping.
STRATASYS.COM
HEADQUARTERS
7665 Commerce Way, Eden Prairie, MN 55344
+1 800 801 6491 (US Toll Free)
+1 952 937 3000 (Intl)
+1 952 937 0070 (Fax)
2 Holtzman St., Science Park, PO Box 2496
Rehovot 76124, Israel
+972 74 745 4000
+972 74 745 5000 (Fax)
© 2017, 2018 Stratasys. All rights reserved. Stratasys, Stratasys signet and FDM are registered trademarks of Stratasys Inc. GrabCAD Print, Stratasys F123 and Stratasys F370 are trademarks of Stratasys, Inc. All other trademarks are the
property of their respective owners, and Stratasys assumes no responsibility with regard to the selection, performance, or use of these non-Stratasys products. Product specifications subject to change without notice. Printed in the USA.
WP_FDM_BreakingTheBarriers_0218a
For more information about Stratasys systems, materials and applications, call 888.480.3548 or visit www.stratasys.com
THE 3D PRINTING SOLUTIONS COMPANY™