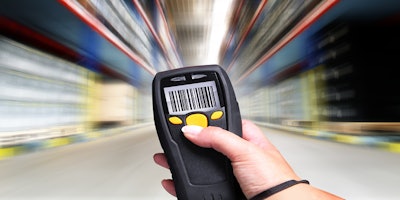
Inventory management has always been important, but
in today’s complex operating environment, it’s critical.
Reducing your turn rate can significantly decrease
working capital and increase profit margins, but without
the right change management you’re at a greater risk of
stock-outs and unhappy customers.
These steps all add up to a more efficient production line. But the right implementation is
key to preventing an increase in stock-outs and unfulfilled customer orders.
The three steps to
successful chemical
inventory control
Sage at-a-glance guide
Here are the three steps you need to take for a better approach to inventory.
Start planning for true demand
Optimizing your inventory is a great start, but accurate demand forecasting, or Materials
Resource Planning (MRP), is an imperative next step. And in a growing marketplace, it’s no
longer enough to simply look at historical orders to predict future demand.
Today’s chemical companies need a smarter approach that considers inputs from across the
business, including sales and marketing, finance, and production. Real-time information
from all your locations is critical for reducing stock-outs and customer lead times.
Optimize your inventory
At first glance, holding enough inventory to cover peak demand makes business sense,
enabling you to fulfill every customer order quickly and efficiently. But in practice, your cash
is nearly always better off deployed in other parts of the business. And for chemical
companies, surplus stock increases risks related to shelf life and lot control.
It’s why many enterprises are choosing to optimize their inventory: rationalizing the number
of ranges they carry and finding ways to reduce surplus inventory. They’re also calculating
significantly more accurate buffer levels, and buying smaller runs of stock more frequently.
Confirm your success
Effective reporting is key to determining the success of any optimization plan, improving the
accuracy of your demand planning based on facts, not guesswork. From lead-time variability
to forecast accuracy, you need real-time access to a single source of data truth.
But with many chemical companies still running disparate business systems across
functions and global locations, it can be difficult to extract the data that’s required without
extra staff or affecting day-to-day operations.
1
2
3
Start managing your inventory for the way chemical business works now.
Learn more about Sage X3. Call 866-530-7243 or visit: sageX3.com
© 2015 Sage Software, Inc. All rights reserved.
Fast to implement, easy to use
Sage X3 includes Sage Inventory Advisor,
which optimizes your inventory system by
automating your processes. The cloud-based
solution can be implemented cost-effectively
in just hours—and updated automatically in
the background. It’s designed for today’s mobile
world, with functionality available in a standard
web browser or on mobile devices. And, because
it’s built on highly scalable infrastructure, it
will grow right along with your business.
“The real-time nature of Sage X3 means we always
have accurate data available to our customer service,
accounting, and manufacturing departments.”
–Anne Robinson, IT director, Alloy Polymers
Quality forecasts, quickly produced
It’s important to be instantly up to date with the
latest activity. That’s why Sage X3 uses dynamic
forecasting and planning capabilities to manage
your inventory levels. A highly graphical tool
makes it quick to plan future replenishments and
optimize inventory across multiple warehouses
and locations to ensure virtually unlimited capacity.
Inventory monitoring shows stock movements and
provides early warning of the stock-outs or surplus
orders that would affect your customer service.
“We never seriously evaluated any other solutions.
Sage ERP X3 delivers what we need.”
–Myra Hager, chief information officer,
ABC Compounding, Inc.
Smart reporting, available anywhere
The user-defined dashboards and configurable
inquiries in Sage X3 provide you with the critical
insights you need, wherever you are in the world.
Identify your best- and least-capable suppliers so
you can make the most effective purchasing
plans and reduce your exposure to risk.
Choose from a huge library of predefined
reports or create your own, or output data into
a variety of Microsoft, HTML, or PDF files.
“Sage X3 offered the best combination of
functionality, technology, value, and implementation
methodology of the systems we evaluated.”
-Terry Steinberg, vice president and CIO,
Aceto Corporation
Sage at-a-glance guide
In the fast-moving chemicals industry, you need a best-fit inventory solution specifically
designed for today’s global operating environment. With an increasing focus on compliance,
consistency between runs, and the safety and efficacy of your products—as well as the
demand for greater personalization in local markets—inventory management is becoming
increasingly complex.
Sage X3 is the simple answer. It’s the enterprise business management solution that’s
designed to deliver maximum growth to chemical companies, with a minimum of complexity.
Accurate inventory and robust supply chain visibility across the enterprise. With
comprehensive inventory tools, your teams will spend less time on order management and
demand forecasting, and ensure the optimal stock situation for you, at every moment.
The modern solution? Your inventory, managed in an instant.