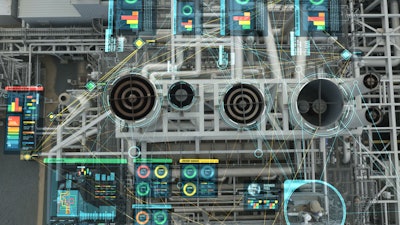
Over the next decade, the global population is expected to grow by 1 billion people to more than 8 billion, and everyone will need electricity. GE expects demand for power to grow 50 percent over the next 20 years, by an additional 3,000 gigawatts (GW) of power-generation capacity.
Getting there will require some creative engineering — both reimagining the usual suspects like turbines and generators as well as deploying new cloud-based digital tools and data analytics. GE has a few ideas.
Soon, the company says, every plant can become a connected, high-tech hub where plant operators will use insights from data pooled in “data lakes” and stored in the cloud to help make better decisions to keep power flowing and lower the cost of power generation. The company has invested over $1 billion to develop Predix, a cloud-based platform for the Industrial Internet. It will serve as the digital backbone of the power plant of the future, allowing operators to write apps and drill into data for insights needed for more efficient operations. GE’s November acquisition of France-based Alstom’s power and grid business also gave GE the capability to deliver an integrated power plant system.
The power plant of the future will stand on two key pillars: the digital power plant and the modular power island, which GE calls AdvantEDGE (see infographic at the bottom of the story). GE’s modular power island design helps significantly simplify the construction of power plants, as pre-fabricated and pre-commissioned modules are delivered to site. That helps reduce the amount of manpower needed on site and helps accelerate the construction time. The digital power plant then brings the modules to higher efficiency. The end result is power plants that cost less to build and generate more, affordable power.
GE introduced the digital power plant at the Minds + Machines conference in San Francisco in September. The company was able to finish the modular power island design with technology it acquired from Alstom this fall. It brought the technology this week to Power-Gen International, the world’s largest energy-generation conference, held every year. “The reason why we can provide this modular power island is that we now have all of the core components in-house,” says Flor Rivas, senior product manager for combined-cycle power plants at GE Power.
The system works like a giant set of industrial building blocks. GE first builds and commissions modules for scope like the ejector system, pipe racks and blowdown tanks. It then ships those prefabricated units to the worksite for assembly. “This new approach will allow GE to deliver the plant in a simplified way,” says Andreas Brautsch, general manager of product management for Integrated Systems. “The modular power island cuts the time needed to build a plant by 25 percent and doesn’t require a huge amounts of highly sophisticated site engineers, which can be expensive and difficult to secure, for the erection of the plant.”
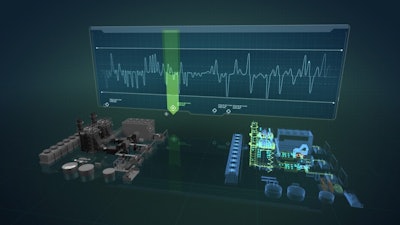
The other half of the power plant of the future is the digital power plant — adding software to power generation that, Rivas says, “will redefine the way customers operate their power plants.” Rivas says that sensors on equipment will constantly collect data about how well each component is working and send it to the cloud. Apps then analyze that data and provide engineers with crucial operational insights such as which parts to replace, which to fix and how to best maintain equipment to limit outages. It also helps them run plants more efficiently.
The data will also allow GE to build a “digital twin” of the entire plant in the cloud and run analytics and test scenarios before applying them in the real world. “With Alstom, we can be more accurate,” says Aaron Zurborg, portfolio architect for software solutions. “In fact, we can provide even greater accuracy across the entire generation fleet. From renewables, coal, nuclear and gas, we’re producing models that we can count on.”
But the technology will go beyond that and collect data from many plants. “With the digital power plant, you can run models and analytics for one plant and expand it across your portfolio,” Zurborg says.
Zurborg estimates that the digital power plant could deliver as much as $50 million in savings for existing combined-cycle gas-powered plants, which pair gas turbines with steam turbines, and up to $230 million in savings for a new plant. He says the digital power plant can be available for every kind of existing plant, even those that don’t run on GE equipment. Says Zurborg: “The world needs more power and we have a great way to get it done.”
All photos courtesy of GE Reports.