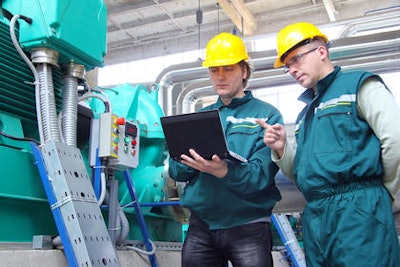
For better or worse, the Internet is woven into our everyday lives. We go online for everything, from looking up movie trivia to booking dental appointments, to buying new homes.
The Internet is so common that we take it for granted. But what many people do not realize is, the potential impact of the Internet on plant operations is just as sweeping. Industrial plants have an enormous opportunity to leverage the Internet to streamline processes, reduce cost, improve safety, and enhance customer service and much more.
Ways of using the Internet to improve plant operations can be quite simple to extraordinarily complex. This article will touch on two of the most important ways.
The Mobile Web: Improving Machine Maintenance, Reducing Downtime
One of the fastest and least expensive ways to put the Internet to use in your operation is to equip shift supervisors and maintenance crews with smartphones or tablets. Something as simple as this can have an immense impact on reducing downtime and increasing throughput. Consider some of these common examples:
- A machine breaks down in Ohio. The maintenance foreman shoots a 20-second video of the problem area and emails it to the manufacturer in Germany. This leads to an almost immediate diagnosis and quick repair, avoiding one or two days of downtime.
- A company is interested in a new, 7-figure machine for its production line — but can’t travel a long distance to see it in operation and make sure its maintenance crew can support it. An online webinar, viewed by all key team members on their mobile devices, features extensive video and Q & A that indicates the new machine can do the job and be properly maintained.
- Accessing online manuals and parts lists from mobile devices allows maintenance crews to identify and order needed replacement parts from the factory floor, not only saving time, but also reducing the chance of the wrong part being ordered.
These simple examples of the Internet at work and on the job suggest a host of ancillary benefits, including reduced travel time and expense, more efficient communication and documentation, along with fewer errors. None of these improvements necessarily requires additional internal software systems, IT support or training. In effect, the Internet offers substantive operational and machine-maintenance benefits — for free.
The Internet of Things: A New Strategic Landscape
This short, easy to understand article from Forbes offers a useful definition of the Internet of Things (IoT):
“Simply put this is the concept of basically connecting any device with an on and off switch to the Internet (and/or to each other). This includes everything from cell phones, coffee makers, washing machines, headphones, lamps, wearable devices and almost anything else you can think of. This also applies to components of machines, for example a jet engine of an airplane or the drill of an oil rig. As I mentioned, if it has an on and off switch then chances are it can be a part of the IoT.” – Jacob Morgan, Forbes Contributor
In a fascinating PDF report from Lopez Research, the impact of IoT (also referred to as Industry 4.0) on manufacturing operations is explained as follows: “By connecting machines a manufacturer can create intelligent networks along the entire value chain that communicate and control each other autonomously with significantly reduced intervention by operators.”
The impact of “smart” machines, components and systems will touch on every aspect of a plant operation. For instance, if finished goods are connected to the Internet with wireless sensors, environmental changes can be recorded and monitored. If a change in environmental conditions threatens to degrade the product, it can be anticipated and avoided.
Monitoring can be taken further. Predictive programs (think simple weather reporting) can alert companies to environmental changes before they occur. Sensors attached to a product can record and monitor environmental changes throughout the entire supply chain, enabling companies to assess issues and product damage that occurs during shipment or receiving, etc.
Fully capitalizing on IoT may require layering new functionality on existing software infrastructure, or completely revamping a legacy system. It requires thinking about raw materials, finished goods, physical plant locations and people as interconnected and interdependent parts of a complex informational whole.
If all this sounds complicated and theoretical — it is. For many plant operations that desire to leverage the Internet, two things must happen at the same time: First, implement small, tactical improvements quickly; and second, create teams to study the theory and practical applications of IoT and construct a long-term implementation plan.
Author Bio:
Amber Carpenter is the Product Specialist at Eaton Filtration Online, a leading online supplier of Eaton filtration products for a wide range of liquid handling and industrial filtration needs. Amanda has a strong understanding of how to solve customer problems based on specific product needs.