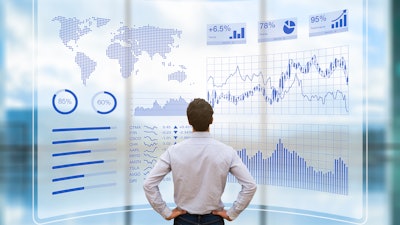
What are your physical assets telling you? Are they performing to design capacity? Are they providing the expected return on investment? Are they aging and in need of capital investment or replacement?
We live in an increasingly data-rich environment, and successful companies must take full advantage of transforming data to information. Among manufacturers there’s growing awareness of how data and analytics can drive operations and maintenance, predicting breakdowns and reducing downtime. However, it’s possible to go further. A mostly untapped opportunity for manufacturers exists in the use of operational data from the factory floor to inform better capital allocation decisions.
If you think about it, capital asset allocation decisions centered around four guiding principles:
- Balancing life-cycle costs and asset performance.
- Examining financial risks against competing capital and O&M expenditures.
- Prioritizing future projects in support of organizational objectives.
- The effect on the income statement – balance sheet or cash flow.
How to make this a reality? One key is to view productive assets as a portfolio. This requires that managers and executives have the data and analytics they need to examine return on investment - not just at one point in time when making the business case to purchase an asset, but over time. This also means having the ability to evaluate performance of assets not just in the context of one production line or one facility, but as part of a higher level, bigger picture command of the assets across the entire enterprise.
One way to think about this is getting the relevant data from the basement, where the maintenance records might be kept, to the board room – or from the factory floor to the CFO suite. That puts the data and information where it will most benefit the company in making better capital allocation and budgeting decisions.
Sources of Data
Available from disparate systems and sources, manufacturers have a lot of data to work with to monitor and understand their hard assets. There’s information that comes from the machine tools, pumps and injection molding machines themselves, from process controllers or from added sensors. Data and information also can come from an organization’s enterprise resource planning system, its manufacturing execution system, its enterprise asset management system, and so on. There may be spreadsheets in the finance department or maintenance logs, or invoices in a physical file cabinet somewhere that may also be relevant.
Fortunately, today we have the tools to upload and organize data from a wide variety of sources – and this is significantly less painful than it once was. Rather than setting up a data warehouse from scratch, an organization can create a data lake in the cloud. The latest software tools and advances in machine learning make the process of ingesting data faster and simpler.
The analysis is easier too. Data and information that was once mostly known to maintenance and operations managers can now be presented by enterprise dashboards that are useful and relevant to senior decision makers in finance and operations. What used to be compiled periodically in a report can now be accessed in real time. The actual performance of a capital asset over time can be tied back to the business case that was written to justify its purchase in the first place. This is something that too often is not done – at least not in any consistent, disciplined, or meaningful way.
Financial Ties
In evaluating capital assets, and data related to those assets, the goal is to support the broader strategic efforts of the enterprise. The data around those assets should be tied back to the three main financial statements: Is the capital asset improving cash flow? Is it helping the balance sheet? Is it supporting profits? When assets are viewed primarily from an operations and maintenance perspective, such ties get lost. When seen from the shop floor, the bigger financial picture gets blurred.
In other words, data and analysis should be focused on supporting capital allocation efforts, both to inform investment and to better manage existing deployed capital assets.
Consider a situation in which a production line makes a mature product, generating cash for the company but not growth and leaving equipment idle at times. Seen from an operation and maintenance viewpoint, the main goal is sufficient budget to keep the line running properly. Seen through a capital planning lens – viewing the equipment as part of the portfolio of capital assets – there may better ways to manage the equipment. Perhaps with additional capital spending or changes in maintenance, a new product can be added to use the line more fully.
For another example, think about a pump that’s a critical asset to keep a production facility in operation. There’s a huge variety of data available for that pump, ranging from hours in service and load information to failure rate data and wear and tear readings from real-time sensors. While this pool of data might be more often used for predictive maintenance scheduling and other operational decisions, there’s much here that can inform capital allocation. T
he full picture allows for better decisions about how the asset is used—whether the pump is at the end of its life cycle, should it be overhauled before it fails, or perhaps whether capital should be allocated for a different pump altogether.
The application of better data on capital assets for more sophisticated capital planning remains, for many companies, an untapped opportunity. Recent advances in data management and analysis make it possible, and now is the time to catch up to the technology.
At the same time, it’s worth at least a thought about where data on capital assets might take us next. As we get better at instrumenting factory equipment, capturing data and analyzing its meaning, there may be bigger innovations to come. Already we can see hints of a future in which a third party with expertise in data and prediction can come into a company, analyze a production line, and guarantee its uptime for a fee. That’s just one possibility for what might come next as our technology advances, but already there are many good reasons for every enterprise to dive deeper into the data.