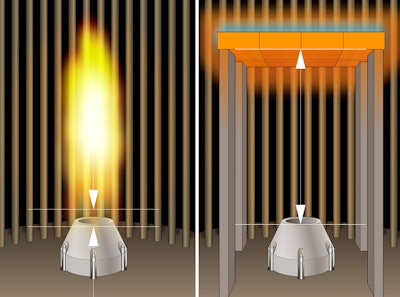
Air quality has improved substantially over the last 30 years due to stricter regulations and cleaner less-polluting technologies. Notwithstanding, new ozone regulations are requiring even tighter restrictions of NOx. Ozone is vital in the upper atmosphere, where it acts to block harmful ultraviolet radiation, but at ground level, ozone is an irritant to mucous membranes and lung tissue. Ozone is also a “criteria pollutant” as defined by the Environmental Protection Agency. Ground level ozone is formed in a complex reaction between NOx and reactive organic compounds. There are many natural sources of reactive organics but most NOx is produced mainly from combustion of hydrocarbon fuels such as natural gas, oil, and coal. Natural gas is the cleanest burning hydrocarbon fuel, but all flames owing to their high temperature have the potential to produce NOx — most commonly nitric oxide (NO) — a fusion of the naturally occurring nitrogen and oxygen in air exposed to high temperature.
Learn More: A Strategic Growth Factor For Manufacturing Firms
From the oil and gas industry to major manufacturing operations, organizations that rely on NOx-creating combustion systems are increasingly looking to slash emissions — without breaking their budgets. A number of technologies have been developed over the years to reduce NOx emissions from industrial sources. Here, we will examine the abilities and limitations of the industry’s most commonly deployed options, as well as emerging technologies that show considerable promise at the industrial scale.
Selective Catalytic Reduction (SCR)
First developed in the 1960s, SCR systems involve the injection of an ammoniacal regent such as ammonia, aqueous ammonia, or urea in the presence of a catalyst to convert NOx back to nitrogen and oxygen. Catalyst costs have steadily dropped since SCR’s early introduction. However, the cost of reagent, catalyst, and transaction costs to ship and store these make it the most costly of all NOx reduction strategies.
Flue Gas Recirculation (FGR)
FGR units redirect a portion of the flue gases produced during the combustion process to the burner with the fresh air. The addition of inert gases to the air cools the flame and dilutes reactive species, thereby reducing the formation of NOx. However, the recirculation of flue gas requires additional energy in the form of increased fan power.For this reason, some air quality districts have contemplated enforcing an upper limit on the amount of flue gases that may be recirculated. The lowest NOx burners currently recirculate up to 40 percent of the flue gas. That’s a lot of flue gas to send around in a circle, and it requires significant fan power to do so.
While SCR and FGR have succeeded in lowering air emissions, they do so at increased costs. More importantly, they are unable to reach the levels of NOx reduction mandated by evolving environmental regulations. Moreover, the use of required chemicals in some systems poses new environmental threats and safety hazards. These solutions also require potentially expensive system redesign with significant impact to both CAPEX and OPEX. Additional, the added complexity of these systems often cause operational issues such as increased corrosion, additional parasitic power, etc., while increasing preventative maintenance costs.
The higher costs of such systems to meet NOx requirements have been a major impediment and constant cause of conflict between the industry, environmental groups, and regulators. Cost reduction and preservation of industrial jobs has led technology providers to approach the issue of NOx gas formation from a different angle. Instead of addressing the problem in the post-combustion process with filters and scrubbers, engineers are turning to the source of the issue: the flame. Recently, a new generation of industrial advanced technology has entered the market, operating at the flame level to eliminate pollutants directly at the source.
Low-NOx (LNB) and Ultra-Low NOx burners (ULNB)
Low- and ultra-low NOx burners typically use some variant of staged combustion, often in conjunction with FGR, for the purpose of lowering NOx formation. In some cases requiring more modest NOx reduction, LNBs can operate without FGR.
Notwithstanding, LNBs and UNLBs are more expensive than the conventional burners they replace. Moreover, LNBs and UNLBs require a larger operating footprint and expensive furnace modifications and downtime. For production units, the downtime required to install UNLBs can exceed the cost of the burners several times. Additionally, these systems tend to create less stable and more elongated flames, which can lead to flame impingement (often severe) in process tubes. Flame impingement can cause increased outages due to maintenance to remove scale or internal coking. In severe cases, flame impingement may cause tube rupture, explosion, and loss of life. UNLBs typically operate over a smaller ratio of maximum to minimum firing rate (known as the turndown ratio). Lower turndown ratios mean less flexibility in meeting demand swings.
Distal Flame Architecture
Distal flame architecture provides a radically different approach to combustion, resulting in unprecedented NOx emissions reduction. By stabilizing the flame at a set distance from the fuel nozzles (Fig.1), distal flame technology optimizes heat transfer, fuel-air mixing, and thermal efficiency. The result is a record-breaking NOx reduction, typically 3 ppm (Fig.2), without additional flue gas, additional cooling air, or catalysts and injected chemicals.
Figure 1. Duplex Technology
Figure 2. Duplex Technology NOx Emissions Performance
Unlike LNB and ULNB options, distal flame architecture isn’t prone to creating flame impingement issues. Thus the technology can reduce maintenance outages and frequency of de-coking. Reduction in flame impingement significantly lowers tube failure rates and enhances tube lifetimes. Reduced maintenance also allows for greater operational savings.
Today, manufacturers and operators of combustion systems have the opportunity to choose from a variety of technologies to abate NOx emissions. As time has shown, the limited capabilities and high costs of traditional approaches will not adequately serve the market moving forward. By reducing pollutants directly at the source, advanced technology architectures are uniquely able to slash NOx emissions at a low cost of system ownership. For the first time, the industry has an economically beneficial means to meet the environmental requirements of today, and of tomorrow.
Joe Colannino is the CTO of ClearSign Combustion Corporation.